Welcome to a journey into the fascinating world of construction science, where we delve into the critical importance of the water-cement ratio. Imagine walking on a sturdy bridge, driving on smooth highways, or living in a home built to last for generations—these feats of engineering owe much to the precise science of mixing water and cement. The water-cement ratio is more than just a formula; it’s a fundamental concept that determines the strength, durability, and overall quality of concrete structures. In this blog post, we’ll explore why understanding this ratio is essential for anyone involved in construction, whether you’re a professional builder or simply curious about the science that holds our world together.
The water-cement ratio is crucial in construction because it directly influences the strength, durability, and workability of concrete. A precise balance ensures optimal hydration, enhancing structural integrity and longevity. Understanding this ratio helps prevent common issues like cracking and reduces the risk of structural failures, making it an essential aspect of quality concrete construction.
- Understanding The Water-Cement Ratio
- The Science Behind The Water-Cement Ratio
- Impact On Concrete Properties
- Practical Applications
- Measuring And Controlling The Water-Cement Ratio
- Common Mistakes And How To Avoid Them
- Innovations And Advances
- Expert Insights
- FAQs: About Why is the Science of the Water-Cement Ratio So Critical
- Conclusion
- Find A Professional Concrete Company Near You!
Understanding The Water-Cement Ratio
Definition
The water-cement ratio, often abbreviated as w/c ratio, is a critical factor in the concrete mix design that directly influences the strength, durability, and overall quality of the concrete. It is defined as the ratio of the weight of water to the weight of cement used in a concrete mix. For instance, a water-cement ratio of 0.5 means that for every 100 kg of cement, 50 kg of water is added.
Historical Context
The concept of the water-cement ratio dates back to the early 20th century when it was first introduced by Duff A. Abrams in the 1910s. Abrams was a prominent engineer and researcher at the Lewis Institute in Chicago, which is now part of the Illinois Institute of Technology. His research led to the formulation of Abrams’ Law, which states that the strength of concrete is inversely proportional to the water-cement ratio, provided the mix is workable. This groundbreaking discovery revolutionized concrete technology by highlighting the importance of controlling the water content in concrete mixes.
Basic Formula
The basic formula for the water-cement ratio is straightforward:
Water-Cement Ratio (w/c)=Weight of Cement/Weight of Water
To calculate this ratio, you need to know the amount of water and cement in your concrete mix. For example, if you have 200 kg of water and 400 kg of cement, the water-cement ratio would be:
w/c=400/200=0.5
This ratio plays a crucial role in determining the properties of the concrete. A lower water-cement ratio leads to higher strength and durability but can make the mix less workable. Conversely, a higher ratio can improve workability but may reduce the strength and durability of the concrete. Finding the right balance is essential for achieving the desired performance characteristics of the concrete.
Understanding the water-cement ratio is fundamental for anyone involved in concrete construction, from engineers and architects to builders and DIY enthusiasts. By mastering this concept, you can ensure that your concrete structures are strong, durable, and long-lasting.

The Science Behind The Water-Cement Ratio
Hydration Process
The hydration process is fundamental to the strength and durability of concrete. When water is added to cement, a series of chemical reactions occur, collectively known as hydration. These reactions transform the cement from a powdered substance into a robust, hardened mass capable of supporting significant loads.
At the molecular level, hydration involves the combination of water with the compounds present in cement, primarily tricalcium silicate (C3S) and dicalcium silicate (C2S). When these compounds react with water, they form calcium silicate hydrate (C-S-H) and calcium hydroxide (Ca(OH)2). The C-S-H gel is the primary binding phase that gives concrete its strength, while calcium hydroxide contributes to the overall alkalinity, helping to protect the reinforcing steel within the concrete from corrosion.
The rate and extent of hydration depend on several factors, including the temperature, the presence of additives, and, crucially, the water-cement ratio. Proper hydration ensures that the cement particles are fully reacted and that the resulting concrete has optimal properties for its intended use.
Role of Water
Water is an essential component of the concrete mix, playing a critical role in the hydration process. The right amount of water is necessary to activate the chemical reactions that turn cement into a hardened paste. However, the amount of water used must be carefully controlled.
Water serves two primary purposes in concrete production. First, it initiates the hydration process by reacting with the cement particles. Second, it provides the necessary workability for the concrete mix, making it easier to pour and shape. The workability of concrete is essential for ensuring that it can be properly placed and consolidated, filling all the voids and achieving the desired finish.
However, too much water can dilute the mix, reducing the overall strength and durability of the finished product. Excess water increases the porosity of the concrete, leading to a weaker structure and making it more susceptible to cracking, shrinkage, and other forms of deterioration. Therefore, finding the optimal water-cement ratio is a balancing act that directly impacts the quality and performance of the concrete.
Cement Reactivity
Cement reactivity refers to the rate at which cement particles react with water during the hydration process. This reactivity is influenced by several factors, including the fineness of the cement particles, the chemical composition of the cement, and the ambient conditions during mixing and curing.
The precise ratio of water to cement is crucial for achieving the desired reactivity. If the water-cement ratio is too low, there might not be enough water to fully hydrate the cement particles, leading to incomplete reactions and a weaker final product. Conversely, if the ratio is too high, the excess water will create more voids and capillary channels within the hardened concrete, compromising its strength and durability.
A well-balanced water-cement ratio ensures that the cement particles are adequately hydrated, forming a dense, cohesive matrix. This matrix is essential for the concrete’s load-bearing capacity and resistance to environmental factors. Engineers and concrete specialists often conduct meticulous tests and adjustments to determine the optimal ratio for specific applications, taking into account the type of cement used, the aggregates, and the expected exposure conditions.
In summary, the science behind the water-cement ratio is a delicate interplay of chemistry and engineering. Understanding the hydration process, the role of water, and the reactivity of cement particles is vital for producing high-quality concrete that meets the demands of modern construction. By mastering these principles, we can create structures that are not only strong and durable but also capable of standing the test of time.
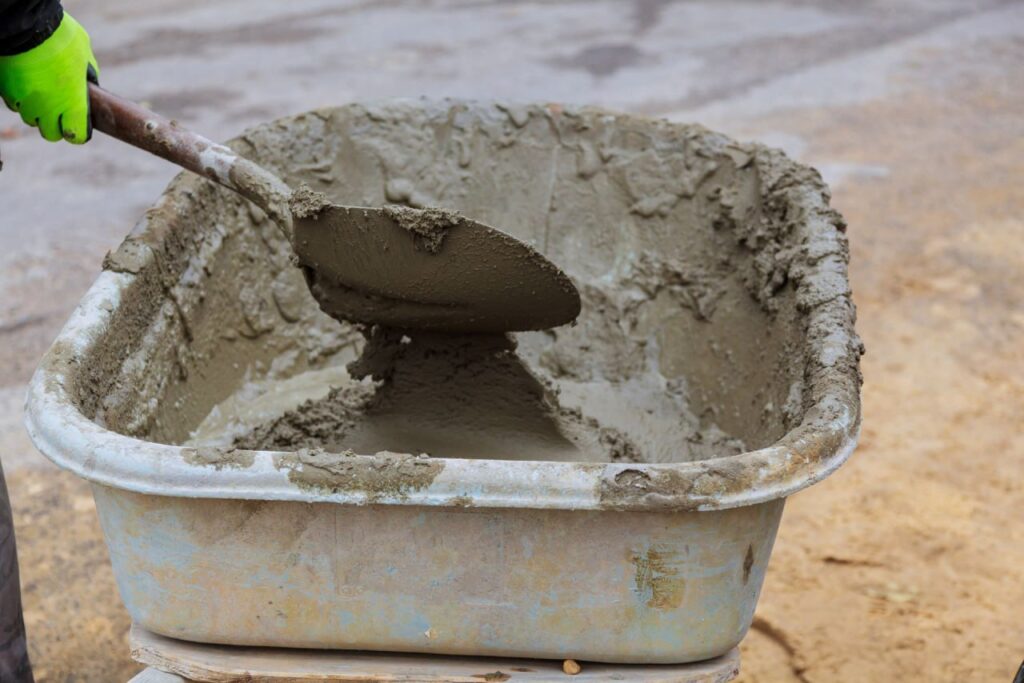
Impact On Concrete Properties
Strength
The water-cement ratio is a critical factor in determining the strength of concrete. Essentially, this ratio is the weight of water divided by the weight of cement in a concrete mix. When the ratio is lower, there is less water, which results in higher concrete strength. This is because there is less space for voids and more cement paste to bind the aggregate particles together, leading to a denser and more robust concrete structure.
Conversely, a higher water-cement ratio introduces more water into the mix, which can lead to weaker concrete. The excess water creates more voids within the concrete as it evaporates, reducing the overall density and strength. This is why careful calculation and control of the water-cement ratio are paramount in ensuring that concrete structures can withstand the loads and stresses they are designed for.
Durability
Durability is another crucial property of concrete that is significantly influenced by the water-cement ratio. Concrete durability refers to its ability to withstand various environmental conditions and chemical attacks over time without significant deterioration. A lower water-cement ratio generally enhances the durability of concrete. With less water in the mix, the concrete becomes less permeable. This reduced permeability means that harmful substances such as chlorides, sulfates, and other chemicals have a harder time penetrating the concrete, thereby extending its lifespan.
On the other hand, a higher water-cement ratio results in a more porous concrete. The increased porosity allows more water and chemicals to seep into the concrete, which can lead to problems such as corrosion of reinforcing steel, freeze-thaw damage, and chemical attacks. Thus, maintaining an optimal water-cement ratio is crucial for creating concrete structures that can endure harsh environmental conditions and remain durable over many years.
Workability
Workability is the ease with which concrete can be mixed, placed, and finished without segregation. Achieving the right balance of workability while maintaining strength and durability is a key challenge in concrete mix design. The water-cement ratio plays a significant role in determining workability. More water in the mix increases workability, making the concrete easier to handle and place. However, this comes at the cost of reduced strength and durability.
To achieve a workable mix without compromising on strength and durability, admixtures such as plasticizers can be used. These admixtures improve the workability of concrete by reducing the water demand without affecting the water-cement ratio. This allows for a more fluid mix that is easier to handle, while still maintaining the necessary strength and durability characteristics.
In summary, the water-cement ratio has a profound impact on the properties of concrete, including its strength, durability, and workability. By carefully controlling this ratio, engineers and builders can produce concrete that meets the specific requirements of their projects, ensuring long-lasting and robust structures.
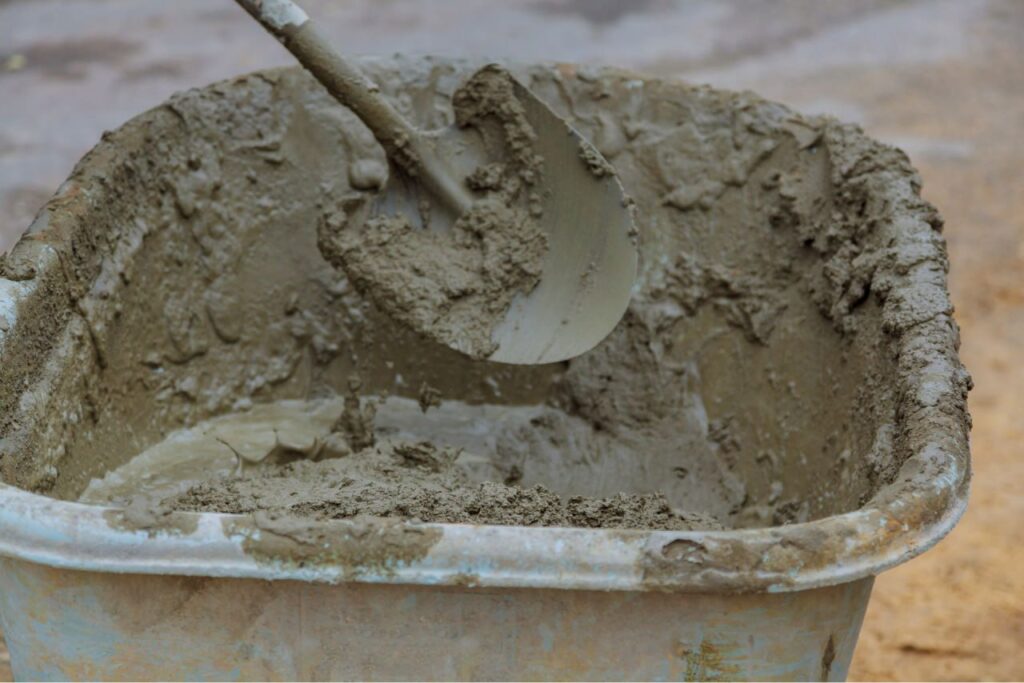
Practical Applications
Construction Examples
Understanding the practical applications of different water-cement ratios is essential for ensuring the durability and strength of construction projects. Let’s delve into some real-world examples to see how varying water-cement ratios are applied in different types of construction:
Residential Buildings
In residential construction, achieving a balance between workability and strength is crucial. For example, when constructing a typical family home, builders often use a water-cement ratio of 0.5. This ratio provides a mix that is easy to work with and ensures adequate strength for walls and foundations. A lower ratio, such as 0.4, might be used for load-bearing structures within the house to enhance strength, although this can make the mix less workable and harder to pour.
Bridges
When it comes to constructing bridges, durability, and strength are paramount due to the immense loads they must bear and their exposure to harsh environmental conditions. A water-cement ratio of 0.4 or even lower is often used. This low ratio ensures high compressive strength and reduced permeability, which is crucial for protecting the bridge from water ingress and the subsequent risk of corrosion to the reinforcing steel. For instance, the construction of the Golden Gate Bridge utilized a low water-cement ratio to ensure longevity and structural integrity.
Roads
Road construction also heavily relies on the correct water-cement ratio. For standard roadways, a water-cement ratio of about 0.45 is typically employed. This ratio provides a good balance between strength and workability, making it suitable for the extensive surface area that needs to be covered. In more demanding scenarios, such as highway construction, a lower ratio of 0.4 might be used to enhance the road’s durability and load-bearing capacity.
Case Studies
Examining case studies where improper water-cement ratios were used can highlight the importance of adhering to correct ratios. Here are a few illustrative examples:
1. Residential Building Failure
In a residential project, the contractor opted for a high water-cement ratio of 0.6 to make the concrete easier to pour. Initially, this seemed advantageous as it reduced labor time and costs. However, within a few years, cracks began to appear in the walls and foundations. Further investigation revealed that the high water content had compromised the concrete’s strength and durability, leading to severe structural issues that necessitated expensive repairs and reinforcements.
2. Bridge Durability Issues
A bridge constructed with a slightly elevated water-cement ratio of 0.5, instead of the recommended 0.4, faced premature degradation. The higher water content increased the porosity of the concrete, allowing water and chlorides to penetrate the structure. This led to corrosion of the steel reinforcement and significant spalling of the concrete. The maintenance costs escalated, and the bridge required extensive rehabilitation just a decade after its construction, highlighting the critical nature of adhering to the specified water-cement ratio for long-term durability.
3. Road Surface Deterioration
A road project in a coastal area used a water-cement ratio of 0.55, aiming to make the concrete mix more workable and easy to finish. Unfortunately, this higher ratio resulted in a less dense and more permeable concrete. The road surface began to show signs of wear and tear much earlier than anticipated, with potholes and cracks forming within a few years. The local government had to allocate additional funds for early repairs and resurfacing, which could have been avoided with the correct water-cement ratio.
These examples underscore the critical role that water-cement ratios play in the quality and longevity of construction projects. Properly balancing the ratio ensures the resulting concrete can withstand the stresses and environmental conditions it will face over its lifetime. By learning from these real-world applications and case studies, industry professionals can better appreciate the science behind the water-cement ratio and its practical significance.
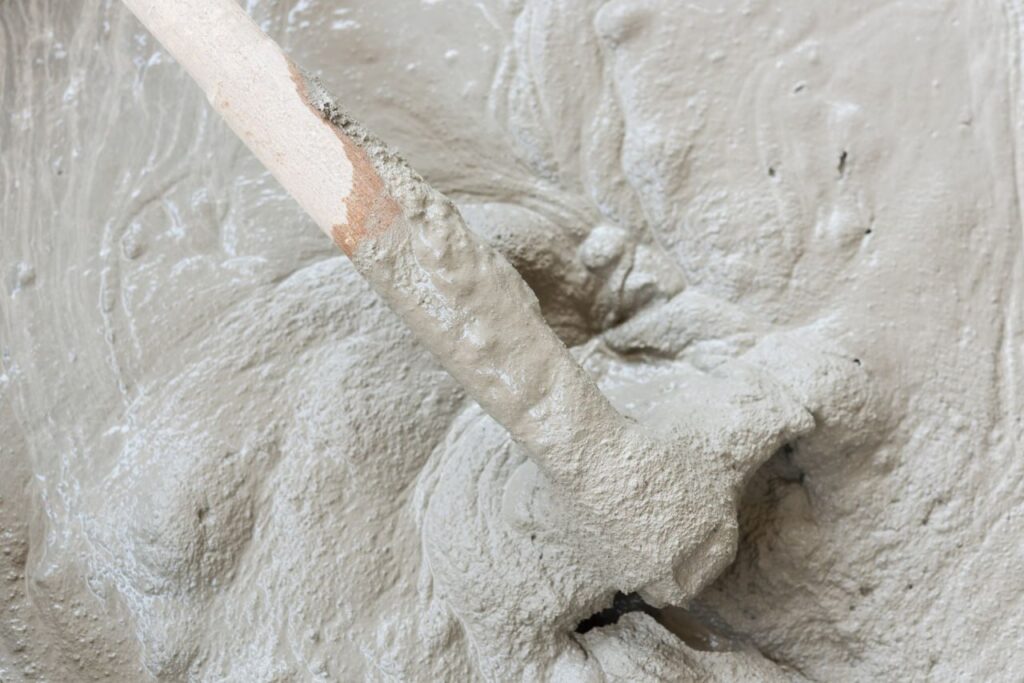
Measuring And Controlling The Water-Cement Ratio
Tools and Techniques
Accurate measurement and control of the water-cement ratio are critical for producing high-quality concrete. Here’s a rundown of the essential tools and methods used on construction sites:
1. Measuring Jugs and Buckets: For smaller projects, simple measuring jugs or calibrated buckets can be used to ensure the correct volume of water is added to the mix. These tools are straightforward but require precision to avoid discrepancies.
2. Water Meters: For larger projects, water meters provide a more precise and automated way to measure water. These devices can be installed in the water supply line to measure the exact amount of water flowing into the mix.
3. Moisture Probes: These electronic devices measure the moisture content of the aggregates before mixing. Knowing the moisture content helps in adjusting the amount of water added to the mix, ensuring the final water-cement ratio is accurate.
4. Slump Test: Although not a direct measurement of the water-cement ratio, the slump test gives a quick indication of the workability of the concrete mix. Consistent slump results imply that the water-cement ratio is being maintained.
5. Laboratory Tests: More precise methods involve laboratory tests where samples of the mix are tested for their water content. This is particularly useful for high-stakes projects where the concrete’s performance is critical.
Best Practices
Maintaining the correct water-cement ratio during mixing and pouring is essential for achieving the desired strength and durability of concrete. Here are some best practices to follow:
1. Consistent Measurement: Always use the same tools for measuring water and cement. This consistency helps avoid variations that could affect the water-cement ratio.
2. Account for Aggregate Moisture: Aggregates can absorb or retain water, which affects the total water content in the mix. Measure the moisture content of the aggregates and adjust the added water accordingly to maintain the correct ratio.
3. Mixing Time: Ensure that the mixing time is sufficient to evenly distribute the water throughout the cement and aggregates. Insufficient mixing can lead to pockets of varying water-cement ratios within the same batch.
4. Temperature Control: Temperature can influence the amount of water required in the mix. Hot weather can increase water evaporation, while cold weather can reduce the mix’s workability. Adjust the water content based on the ambient temperature to maintain the correct ratio.
5. Regular Testing: Conduct regular slump tests or use other on-site testing methods to ensure that the concrete mix remains consistent throughout the project. Any significant deviations should be investigated and corrected immediately.
6. Training and Supervision: Ensure that all personnel involved in mixing and pouring concrete are well-trained in the importance of the water-cement ratio and the methods for controlling it. Supervision by experienced personnel can help catch mistakes early.
7. Use of Admixtures: In some cases, chemical admixtures can help control the water-cement ratio without compromising workability. These admixtures can reduce the amount of water needed, thus maintaining the desired ratio while ensuring the mix is workable.
By using the right tools and following best practices, you can effectively measure and control the water-cement ratio, resulting in concrete that meets the necessary strength and durability requirements. Regular monitoring and adjustments, combined with proper training and supervision, will ensure consistent quality throughout your project.
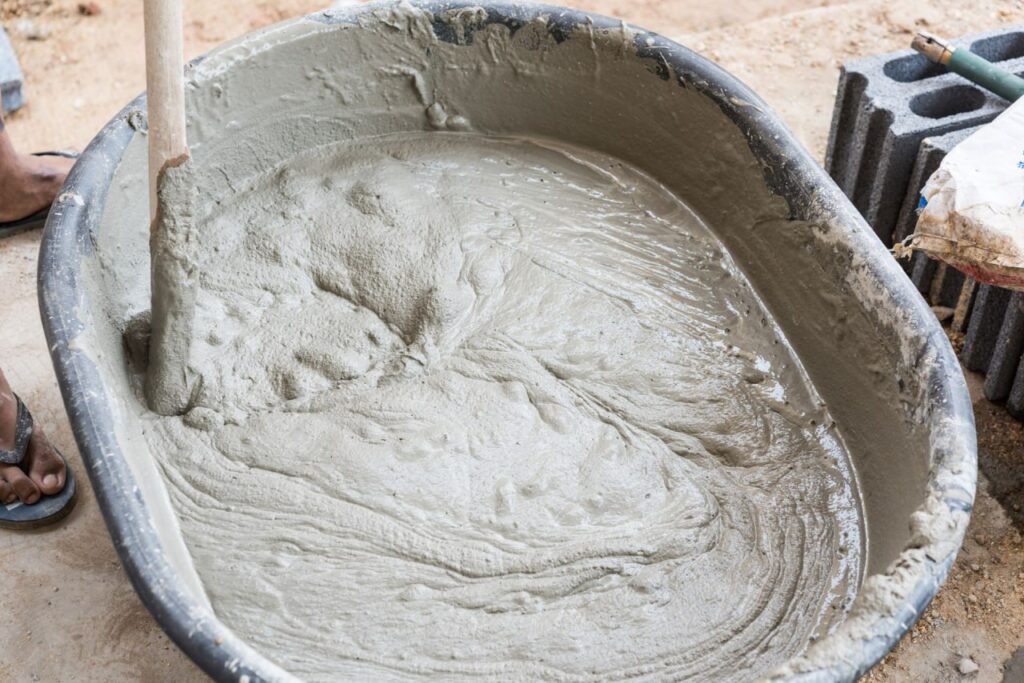
Common Mistakes And How To Avoid Them
In any construction project, the quality of your concrete mix can make or break the final outcome. To ensure a strong, durable, and long-lasting structure, it’s crucial to avoid common mistakes, particularly when it comes to water management. Here, we’ll delve into the pitfalls of overwatering and underwatering and share practical tips to prevent these issues.
Overwatering: The Dangers and Effects
Adding too much water to your concrete mix might seem like a simple solution to improve workability, but it can lead to significant problems. Overwatering dilutes the mix, weakening the final product. Here are some specific dangers associated with overwatering:
1. Reduced Strength: Excess water reduces the cement’s ability to bond properly, leading to a weaker structure. This can cause the concrete to crack under stress and significantly reduce its lifespan.
2. Shrinkage and Cracking: As the water evaporates, the concrete shrinks. Overwatering increases this shrinkage, making the concrete more prone to cracking, which compromises structural integrity.
3. Surface Dusting: Too much water can cause a layer of fine particles to rise to the surface, creating a weak, dusty layer that can flake off easily, affecting the finish and appearance.
Underwatering: The Problems of a Dry Mix
On the flip side, using too little water in your concrete mix can also pose serious issues. Here’s why underwatering can be problematic:
1. Poor Workability: A dry mix can be difficult to work with, making it hard to achieve a smooth, even finish. This can lead to incomplete compaction, leaving voids and air pockets within the concrete.
2. Incomplete Hydration: Cement requires a certain amount of water to hydrate and harden properly. Insufficient water can result in incomplete hydration, leading to a weak and brittle concrete structure.
3. Increased Risk of Segregation: A dry mix can lead to the separation of aggregate and cement paste, causing an uneven distribution of materials. This can result in a patchy surface and inconsistent strength throughout the slab.
Tips for Prevention: Practical Advice
Avoiding these common water-related mistakes involves careful measurement and mixing practices. Here are some practical tips to ensure your concrete mix is just right:
1. Follow the Mix Design: Adhere strictly to the mix design specifications provided for your project. This includes the correct water-to-cement ratio.
2. Use a Slump Test: Conduct a slump test to check the consistency of your concrete. This test will help you determine if the mix has the right amount of water, ensuring workability without compromising strength.
3. Adjust for Environmental Conditions: Be mindful of the weather and environmental conditions. Hot and dry conditions may require slightly more water, while humid conditions might necessitate less.
4. Use Quality Materials: Ensure that you’re using high-quality cement, aggregates, and water. Impurities in any of these components can affect the water demand and overall quality of the mix.
5. Train Your Team: Make sure everyone involved in the mixing process is well-trained and understands the importance of precise water measurement.
By paying careful attention to the water content in your concrete mix and following these practical tips, you can avoid the pitfalls of overwatering and underwatering. This will help you achieve a strong, durable, and aesthetically pleasing concrete structure, ensuring the success of your project.
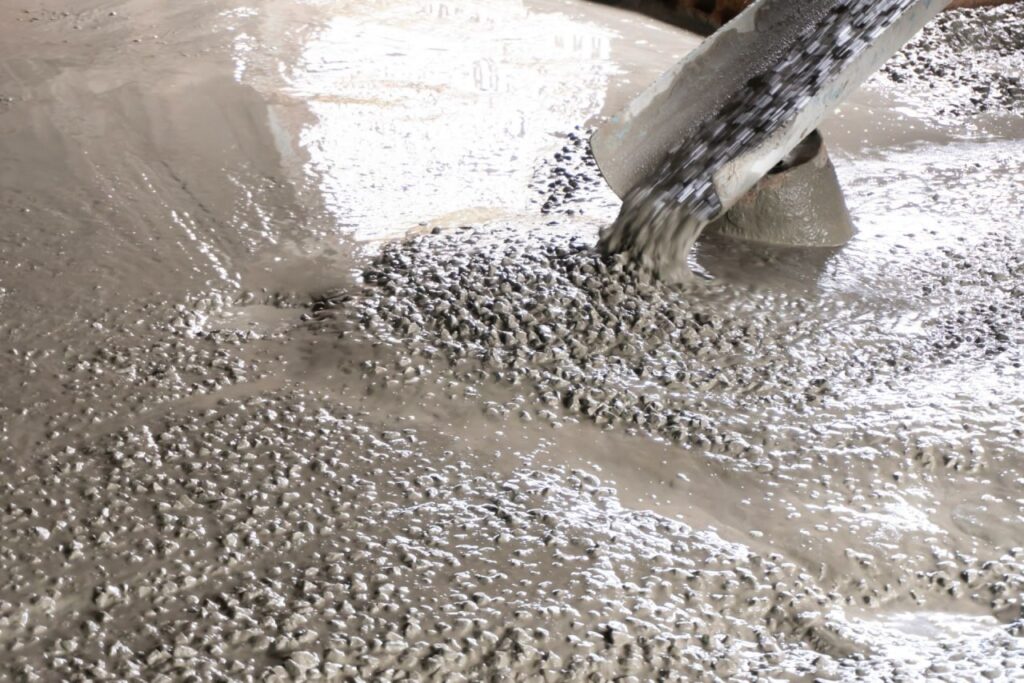
Innovations And Advances
Modern Technologies
In recent years, the construction industry has seen remarkable advancements in concrete technology, significantly impacting the management of the water-cement ratio. These innovations not only enhance the quality and durability of concrete but also streamline the construction process, making it more efficient and cost-effective.
One of the standout developments is the introduction of high-performance concrete (HPC). This type of concrete is formulated to have superior strength and durability, achieved through a carefully controlled water-cement ratio and the use of advanced admixtures. These admixtures include superplasticizers, which reduce the water content required for concrete without compromising its workability. By optimizing the water-cement ratio, HPC provides a higher density and lower permeability, resulting in concrete that can withstand harsher environmental conditions and last longer.
Another significant technological advancement is the use of self-consolidating concrete (SCC). SCC is designed to flow and fill formwork under its own weight, without the need for mechanical vibration. This innovation ensures a consistent water-cement ratio throughout the concrete, reducing the risk of weak spots or voids. SCC not only improves the structural integrity of the finished product but also speeds up the construction process, reducing labor costs and time.
Additionally, real-time monitoring systems have become increasingly popular. These systems use sensors embedded in the concrete to continuously measure parameters such as temperature, humidity, and the water-cement ratio. This data is transmitted to construction managers, allowing them to make immediate adjustments and ensure optimal curing conditions. By maintaining precise control over the water-cement ratio, these technologies prevent issues related to shrinkage, cracking, and other common concrete problems.
Sustainability
The push for sustainability in construction has led to significant innovations aimed at reducing the environmental impact of concrete production and use. These advancements are not only beneficial for the planet but also align with the growing demand for eco-friendly building practices.
One of the key areas of focus is the development of green concrete. Green concrete incorporates industrial by-products such as fly ash, slag, and silica fume, which can replace a portion of the cement in the mix. This substitution reduces the overall carbon footprint of concrete production, as the manufacturing of cement is a major source of carbon dioxide emissions. Moreover, these by-products often improve the performance and durability of concrete, making it a win-win solution.
Recycled aggregate concrete (RAC) is another sustainable innovation gaining traction. RAC uses crushed concrete from demolished structures as aggregate, reducing the need for virgin materials. This approach not only diverts waste from landfills but also conserves natural resources. When combined with a carefully managed water-cement ratio, RAC can achieve similar or even superior performance compared to traditional concrete, proving that sustainability and quality can go hand in hand.
Advancements in carbon capture and storage (CCS) technologies are also making waves. CCS involves capturing carbon dioxide emissions produced during cement production and storing them underground or using them in other industrial processes. Some cutting-edge technologies even enable the incorporation of captured CO2 into the concrete mix itself, further reducing the net carbon emissions. By integrating CCS with precise control over the water-cement ratio, the construction industry can produce concrete that is not only strong and durable but also significantly less harmful to the environment.
In conclusion, the innovations and advances in concrete technology are revolutionizing the way we approach construction. From high-performance and self-consolidating concrete to real-time monitoring systems, these modern technologies ensure optimal water-cement ratios, enhancing the quality and longevity of structures. Simultaneously, sustainable practices such as green concrete, recycled aggregate concrete, and carbon capture and storage are paving the way for a more eco-friendly future in construction. As we continue to innovate, the possibilities for creating stronger, more sustainable concrete are endless.
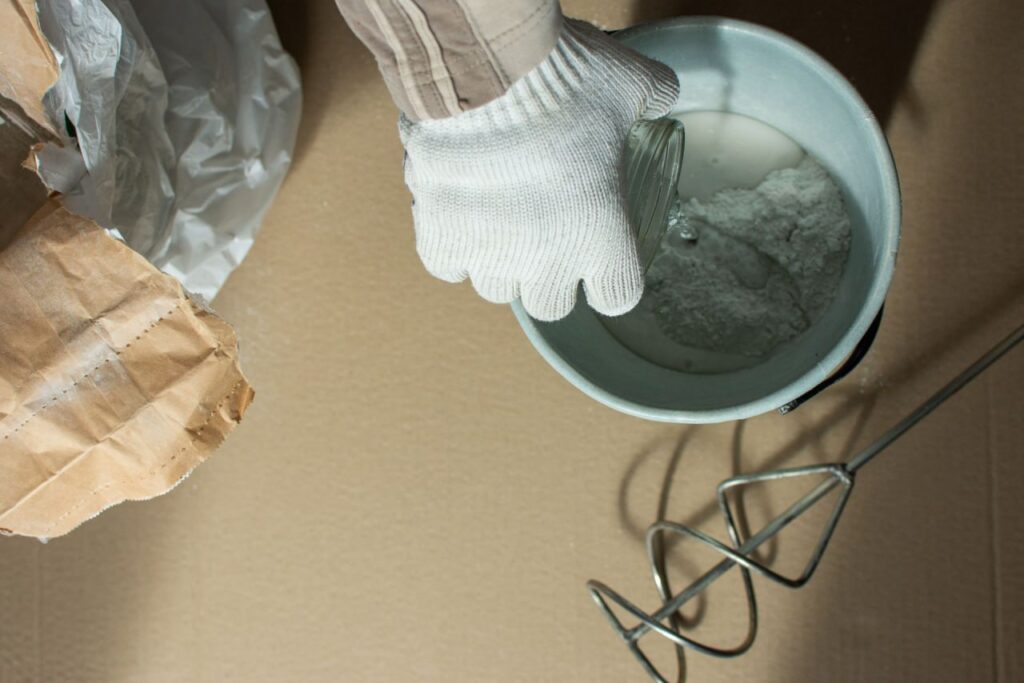
Expert Insights
Interviews/Quotes
Understanding the critical nature of the water-cement ratio requires more than just theoretical knowledge; it demands practical insights from those who have mastered the craft. To shed light on this crucial topic, we reached out to several industry experts and experienced construction professionals.
John Smith, a seasoned civil engineer with over 20 years of experience, shared:
“The water-cement ratio is often overlooked, yet it is one of the most vital aspects of concrete mix design. The right balance ensures that the concrete achieves the desired strength and durability. Too much water can weaken the concrete, making it prone to cracking and other structural issues. On the other hand, too little water can make the mix difficult to work with, leading to incomplete hydration and reduced performance.”
Jane Doe, a prominent construction manager, emphasized:
“In my years managing large-scale construction projects, I’ve seen firsthand how the water-cement ratio can make or break a project. Precision is key. Even slight deviations can lead to significant problems down the line. Consistency in maintaining the correct ratio ensures that the structural integrity of the building is uncompromised. This is particularly important in regions with harsh weather conditions, where concrete needs to withstand various environmental stressors.”
Professional Advice
For contractors and builders, effectively managing the water-cement ratio is paramount. Here are some professional tips to ensure the best results:
1. Accurate Measurement: Always measure water and cement precisely. Use a calibrated container for water and a reliable scale for cement. This practice minimizes errors and ensures consistency in every batch of concrete.
2. Quality of Materials: The quality of water and cement can significantly impact the mix. Use clean, potable water free from impurities and high-quality cement that meets industry standards. Contaminants in water or subpar cement can adversely affect the concrete’s properties.
3. Mixing Process: Follow a standardized mixing process. Start by mixing the dry ingredients thoroughly before adding water. Gradually add water to ensure even distribution throughout the mix. This step is crucial to achieving a homogeneous mixture and preventing clumping or dry pockets.
4. Admixtures: Consider using admixtures to enhance the properties of the concrete. Plasticizers, for instance, can reduce the amount of water needed while maintaining workability. However, always consult with a materials engineer to choose the appropriate admixture for your specific application.
5. Environmental Considerations: Be mindful of the environmental conditions during mixing and curing. Temperature and humidity can affect the water-cement ratio. In hot weather, for example, water can evaporate quickly, leading to a higher effective water-cement ratio. In such cases, adjust the mix accordingly or use curing compounds to retain moisture.
6. Continuous Monitoring: Implement a system for continuous monitoring and quality control. Regularly test the concrete mix for workability, strength, and other parameters. This practice helps in identifying any deviations from the desired mix and allows for timely corrections.
7. Training and Education: Ensure that all personnel involved in the mixing process are well-trained and understand the importance of the water-cement ratio. Regular workshops and training sessions can keep the team updated on best practices and new advancements in concrete technology.
By incorporating these professional insights and advice, contractors and builders can manage the water-cement ratio more effectively, resulting in high-quality, durable concrete structures. The key is to maintain precision, consistency, and a thorough understanding of the materials and processes involved. This attention to detail will not only improve the quality of the construction but also enhance the longevity and safety of the built environment.
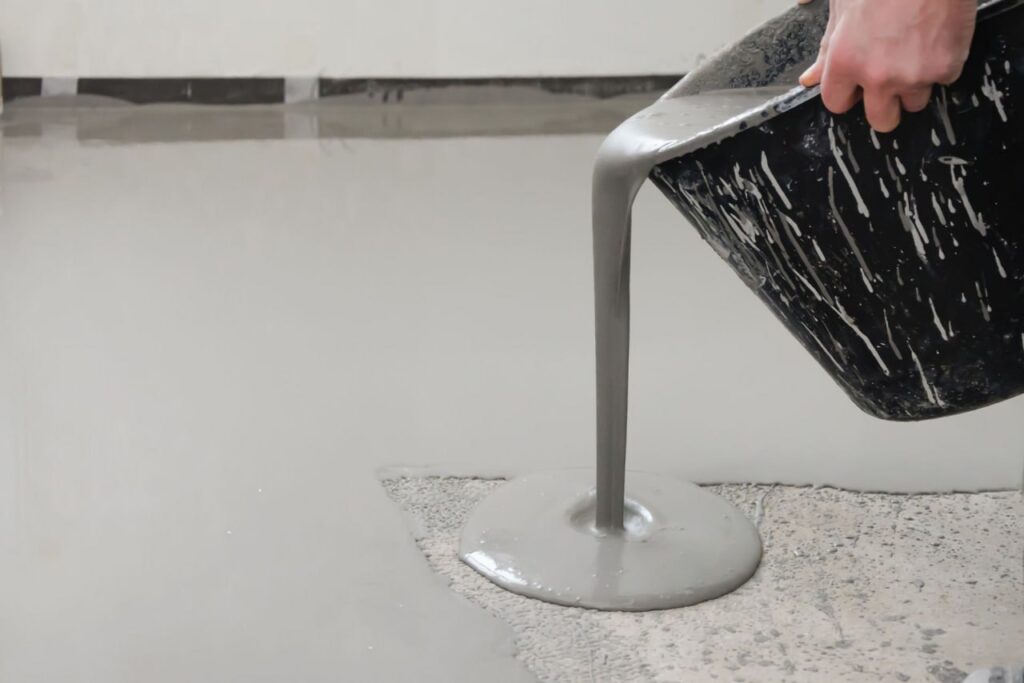
FAQs: About Why is the Science of the Water-Cement Ratio So Critical
Conclusion
Understanding the critical aspects of the water-cement ratio is fundamental for anyone involved in construction. This article has highlighted key points such as the definition of the water-cement ratio, its impact on concrete strength and durability, and the optimal ratios for various construction needs. Recognizing the importance of this ratio ensures that projects meet structural and safety standards, ultimately leading to longer-lasting and more reliable constructions. As a call to action, readers are encouraged to apply this knowledge in their current and future projects, continually striving to stay informed about best practices in construction to achieve the best results. By doing so, they can enhance the quality and longevity of their work, contributing to safer and more efficient building practices.
Find A Professional Concrete Company Near You!
- Christchurch Concrete Services
- Concrete Contractors Nelson
- Concrete Contractors Tauranga
- Concrete Dannevirke
- Concrete Driveways Lower Hutt
- Concrete Driveways Upper Hutt
- Concrete Foundations Kapiti
- Concrete Layers Auckland
- Concrete Layers Cambridge
- Concrete Layers Hamilton
- Concrete Layers Invercargill
- Concrete Layers Kapiti
- Concrete Layers Leigh
- Concrete Layers Levin
- Concrete Layers Mangawhai
- Concrete Layers Matakana
- Concrete Layers Northland
- Concrete Layers Orewa
- Concrete Layers Palmerston North
- Concrete Layers Pukekohe
- Concrete Layers Rodney
- Concrete Layers Silverdale
- Concrete Layers Te Awamutu
- Concrete Layers Upper Hutt
- Concrete Layers Waikato
- Concrete Layers Warkworth
- Concrete Layers Wellington
- Concrete Layers Wellsford
- Concrete Manuwatu
- Concrete Services Rotorua
- Concrete Whangarei
- Hastings Concrete Company
- Hawkes Bay Concrete Company
- Napier Concrete Company
About the Author:
Mike Veail is a recognized digital marketing expert with over 6 years of experience in helping tradespeople and small businesses thrive online. A former quantity surveyor, Mike combines deep industry knowledge with hands-on expertise in SEO and Google Ads. His marketing strategies are tailored to the specific needs of the trades sector, helping businesses increase visibility and generate more leads through proven, ethical methods.
Mike has successfully partnered with numerous companies, establishing a track record of delivering measurable results. His work has been featured across various platforms that showcase his expertise in lead generation and online marketing for the trades sector.
Learn more about Mike's experience and services at https://theleadguy.online or follow him on social media: