Welcome to our comprehensive guide on aluminium cladding costs per m² in New Zealand! Whether you’re renovating your home or embarking on a new construction project, understanding the cost of aluminium cladding is essential for effective budgeting. In this blog post, we’ll explore everything you need to know about the pricing, factors that influence the cost, and why aluminium cladding has become a popular choice for Kiwi homeowners and builders alike. We’ll break down costs, offer comparisons with other materials, and provide tips on how to estimate and potentially reduce expenses all in a straightforward, human tone that makes it easy to plan your next project with confidence.
The average cost of aluminium cladding per m² in New Zealand ranges from $100 to $300, depending on factors such as material quality, design complexity, and regional labor rates. Aluminium cladding is a durable, low-maintenance option that offers long-term value for both residential and commercial properties, making it a popular choice in NZ’s varied climate.
- What Is Aluminium Cladding
- Overview Of Aluminium Cladding Costs Per M² In New Zealand
- Breaking Down The Costs: What's Included In The Price Per Square Meter
- Comparison: Aluminium Cladding Vs Other Cladding Materials
- Why Choose Aluminium Cladding For Your NZ Property
- How To Estimate The Total Cost Of Your Aluminium Cladding Project
- Tips For Reducing Aluminium Cladding Costs In NZ
- Case Studies: Real-Life Aluminium Cladding Projects In New Zealand
- Answering Common Questions About Aluminium Cladding Costs In NZ
- FAQs: About Aluminium Cladding Cost Per M2 In NZ
- Conclusion
- Find A Professional Cladding Company Near You!
What Is Aluminium Cladding
Definition
Aluminium cladding is a modern building material used primarily as an exterior layer to protect and enhance the appearance of buildings. It is essentially a type of external wall covering made from aluminium sheets or panels, designed to offer both functional and aesthetic benefits. By acting as a protective barrier, aluminium cladding shields buildings from harsh weather conditions, such as rain, wind, and UV radiation. At the same time, it serves as a decorative feature, adding a sleek and contemporary look to the structure. This combination of durability and style has made aluminium cladding a popular choice in both residential and commercial construction projects.
One of the key advantages of aluminium cladding is its lightweight nature, which makes it easier to install compared to heavier materials like brick or stone. Despite being lightweight, it remains highly durable and resistant to corrosion, making it suitable for a wide range of environments. The material also requires minimal maintenance, as it doesn’t rust, peel, or fade easily, which enhances its long-term value as a building material.
Types of Aluminium Cladding
Aluminium cladding comes in various styles, allowing architects and builders to choose the perfect fit for their projects. Some of the most common types include.
- Flat Panels: These panels are sleek and smooth, offering a modern, minimalist appearance. They are often used in urban environments where clean lines and contemporary aesthetics are desired. Flat panels are available in various finishes, from matte to glossy, and can be painted or anodized to achieve different colors.
- Corrugated Sheets: Corrugated aluminium cladding features ridges or grooves, adding texture and depth to the exterior of a building. This type of cladding is not only visually appealing but also provides added structural strength, making it ideal for both residential homes and industrial buildings. The ridges can vary in size and spacing, offering flexibility in design.
- Textured Finishes: Textured aluminium cladding can mimic the look of other materials, such as wood, stone, or even brick, while providing the durability and low maintenance benefits of aluminium. These finishes are often used to add character and interest to the façade of a building, without compromising on functionality.
In addition to these types, aluminium cladding can also be customized with perforations, patterns, or geometric designs, allowing for even greater creativity in architectural design. Whether it’s used to create bold visual statements or to blend seamlessly with the surroundings, aluminium cladding offers an abundance of design possibilities.
Popularity in New Zealand
Aluminium cladding has gained significant popularity in New Zealand, largely due to its ability to withstand the country’s diverse climate. From the wet and windy coastal regions to the colder mountainous areas, aluminium cladding performs exceptionally well. Its resistance to corrosion makes it ideal for buildings near the ocean, where salt-laden air can cause other materials to deteriorate quickly.
Additionally, aluminium cladding is favored for its sleek and modern appearance, which aligns well with contemporary architectural trends. New Zealanders appreciate the clean, minimalistic aesthetic that aluminium cladding can provide, particularly in urban and suburban settings. Furthermore, the low maintenance requirements of aluminium cladding appeal to homeowners and property developers alike, as it reduces long-term upkeep costs while ensuring the building maintains its fresh look over time.
Aluminium cladding is a versatile, durable, and visually appealing building material that is used to protect and enhance the exterior of buildings. With its range of styles and finishes, along with its suitability for New Zealand’s varied climate, it’s no wonder that aluminium cladding has become a top choice for architects, builders, and homeowners alike.
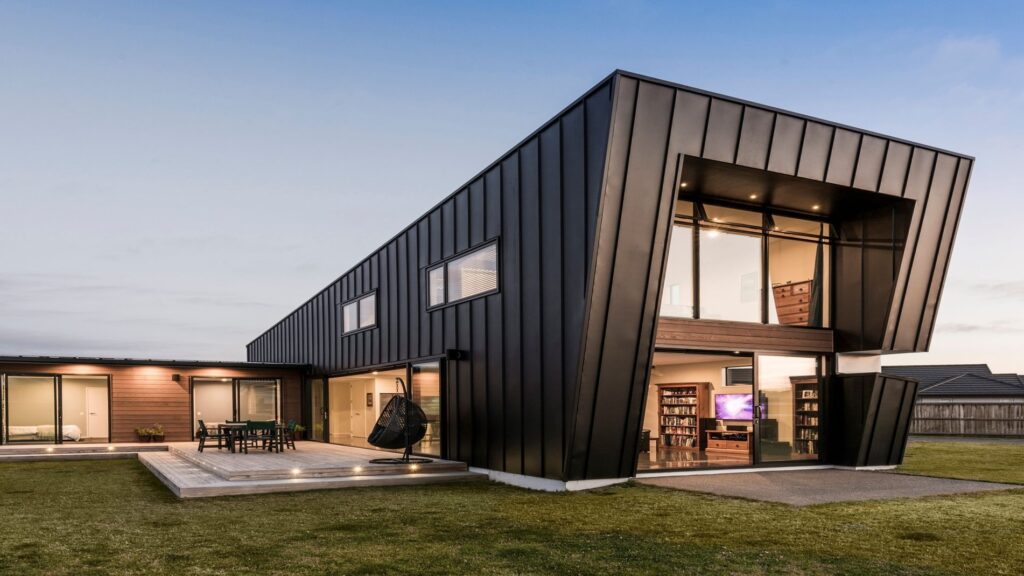
Overview Of Aluminium Cladding Costs Per M² In New Zealand
When considering aluminium cladding for your home or commercial building in New Zealand, understanding the cost is crucial. Aluminium cladding is a durable and modern solution that is growing in popularity, but prices can vary based on a number of factors. Below is a comprehensive breakdown of the typical cost range and the variables that influence aluminium cladding pricing across the country.
General Cost Range for Aluminium Cladding in New Zealand
The cost of aluminium cladding per square meter in New Zealand generally falls within the range of $100 to $300 per m². This wide range is dependent on several factors such as the quality of the materials, the complexity of the design, and labor costs. For basic installations with standard materials, you can expect to be on the lower end of this scale. However, projects requiring higher-end materials or more intricate designs will push the price toward the upper limit.
Factors Influencing Aluminium Cladding Price in New Zealand
1. Material Quality
The grade of aluminium used in cladding plays a significant role in determining the overall cost. Higher-quality aluminium, which may be thicker, more durable, or have enhanced corrosion resistance, will typically cost more. The coatings applied to the aluminium, such as powder coatings or anodized finishes, can also drive up the price. These coatings not only contribute to the aesthetic appeal but also provide added protection against the elements, particularly in coastal areas where saltwater corrosion is a concern.
2. Style and Design
Aluminium cladding comes in a wide array of designs and finishes, from sleek and smooth surfaces to more complex patterns or textured finishes that mimic materials like wood or stone. More intricate or custom designs can substantially increase the cost per square meter. These bespoke finishes may require additional manufacturing processes or specialized materials, both of which contribute to higher expenses. Additionally, specific colors or treatments that enhance the visual appeal of the building may also result in higher costs.
3. Installation Costs
Labor costs in New Zealand vary significantly depending on the region and the complexity of the installation. For instance, urban centers such as Auckland and Wellington typically have higher labor rates due to demand and cost of living. In contrast, smaller towns or more rural areas might offer more affordable labor. However, in all cases, the installation cost is a key component of the overall project budget. Complex installations that require additional customization, adjustments for unique building shapes, or challenging working conditions will increase labor costs.
4. Building Size and Shape
The size and shape of your building can also influence the price of aluminium cladding. Larger buildings will naturally require more material, which drives up the total cost. However, economies of scale may come into play, potentially reducing the cost per square meter for very large projects. Irregularly shaped buildings or those with many architectural features, such as curves or varying elevations, can be more difficult and time-consuming to clad, increasing both material waste and labor expenses.
5. Local Market Conditions
The cost of aluminium cladding can also be influenced by local market conditions within New Zealand. For example, in Auckland, where construction activity is high and demand for materials is strong, prices may be higher due to market competition and availability issues. In contrast, regions like Christchurch, where the market may be less saturated, could offer slightly more competitive pricing. Additionally, regional variations in transportation costs, supplier availability, and local building regulations can also affect the overall cost.
Aluminium cladding offers a durable, stylish, and low-maintenance exterior solution for buildings across New Zealand. When planning your project, it’s important to account for not only the base material costs but also the influence of factors such as design complexity, labor, building dimensions, and regional market conditions. By understanding these variables, you can better estimate the total cost of your aluminium cladding project and make informed decisions tailored to your budget and aesthetic goals.
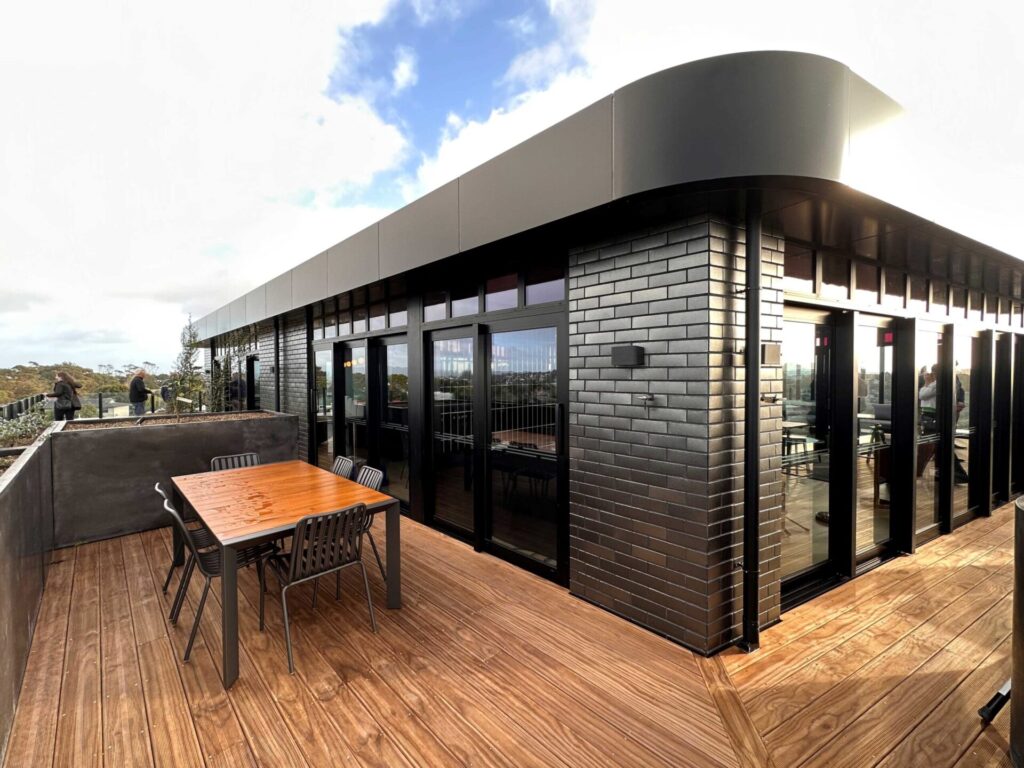
Breaking Down The Costs: What’s Included In The Price Per Square Meter
Understanding the cost per square meter (m²) when it comes to construction or installation projects is essential for budgeting accurately. Whether you’re undertaking a home renovation or a commercial build, every aspect from materials to hidden costs can affect the final price. Below, we break down the typical components that go into the price per square meter to help you better grasp the financial side of your project.
Materials: What’s Included
The bulk of the cost per square meter often revolves around the materials used. In construction projects, this usually includes essential components such as.
- Cladding Panels: These are the primary materials used to cover and protect the exterior of a building. The type of cladding, whether it’s aluminum, composite, or timber, significantly affects the overall cost. Higher-quality materials come with a higher price tag but usually offer better durability and performance.
- Fixings and Brackets: These are the hardware components necessary to securely attach cladding panels to the structure. The price of these fixings can vary depending on the materials and specifications required by the project.
- Insulation: In many cases, insulation is included in the material costs. Proper insulation is critical for maintaining energy efficiency and ensuring the building meets local regulatory standards.
- Sealants and Adhesives: Often overlooked, sealants are crucial for ensuring that the materials are watertight and properly bonded, adding a layer of protection against the elements.
Labor: Average Rates and What It Covers
Labor is another significant part of the cost per square meter, often charged based on the complexity of the project. Labour costs typically cover.
- Preparation: This includes site clearing, surface preparation, and laying down any underlayment or foundational work before installation can begin. This phase ensures that everything is ready for the next steps.
- Installation: This is the core work where materials are fitted to the building. Labour rates may vary depending on the expertise required, the intricacy of the work, and the time taken to complete it.
- Finishing: After installation, finishing touches such as painting, sealing, or minor repairs ensure that the project looks polished and meets aesthetic standards. This step is often more labor-intensive than expected and can add to overall costs.
Labor rates can fluctuate based on your location, the experience level of the tradespeople, and the project’s timeline. It’s worth noting that projects requiring specialized skills, like installing premium materials, may incur higher labor costs.
Additional Costs to Consider
While materials and labour make up the bulk of the cost per square meter, several additional expenses could also impact your budget.
- Scaffolding: If you’re working on a multi-story building or complex installations, scaffolding will likely be a necessary expense. The cost of scaffolding can vary based on the height, length of time it is required, and safety measures needed for your specific project.
- Weatherproofing: Depending on your location’s climate, you may need extra treatments or layers to ensure your building is weatherproof. These can include protective coatings or additional layers of waterproof materials that help shield the structure from the elements.
- Waste Removal: Don’t forget about the disposal of old materials or project offcuts. Depending on the project’s scale, this could involve hiring a skip or paying for a waste removal service. Neglecting this step could lead to unwanted delays or fines for improper disposal.
Hidden Costs: What to Watch For
When planning your project, it’s easy to focus on the obvious expenses, but hidden costs can quickly add up. These may include.
- Custom Orders: If your project requires specially manufactured materials, such as custom-shaped cladding panels, expect to pay extra. Custom materials typically come with longer lead times and higher costs due to the bespoke nature of the production.
- Delivery Charges: Depending on your location and the size of the materials, delivery costs can be significant. Make sure to ask your suppliers if these are included in the initial price or if they will be billed separately.
- Urgent Installation Fees: If your project is under a tight deadline, you might have to pay for expedited services. Urgent installation fees can quickly escalate the overall cost, especially if you require overtime work or fast-tracked material deliveries.
When breaking down the cost per square meter, it’s crucial to account for every aspect of the project. From materials and labour to scaffolding, weatherproofing, and waste removal, each element contributes to the total price. Be mindful of hidden costs like custom orders, delivery fees, and urgent installation charges, as these can significantly impact your budget. By thoroughly understanding these factors, you can better plan your project and avoid unexpected financial surprises.
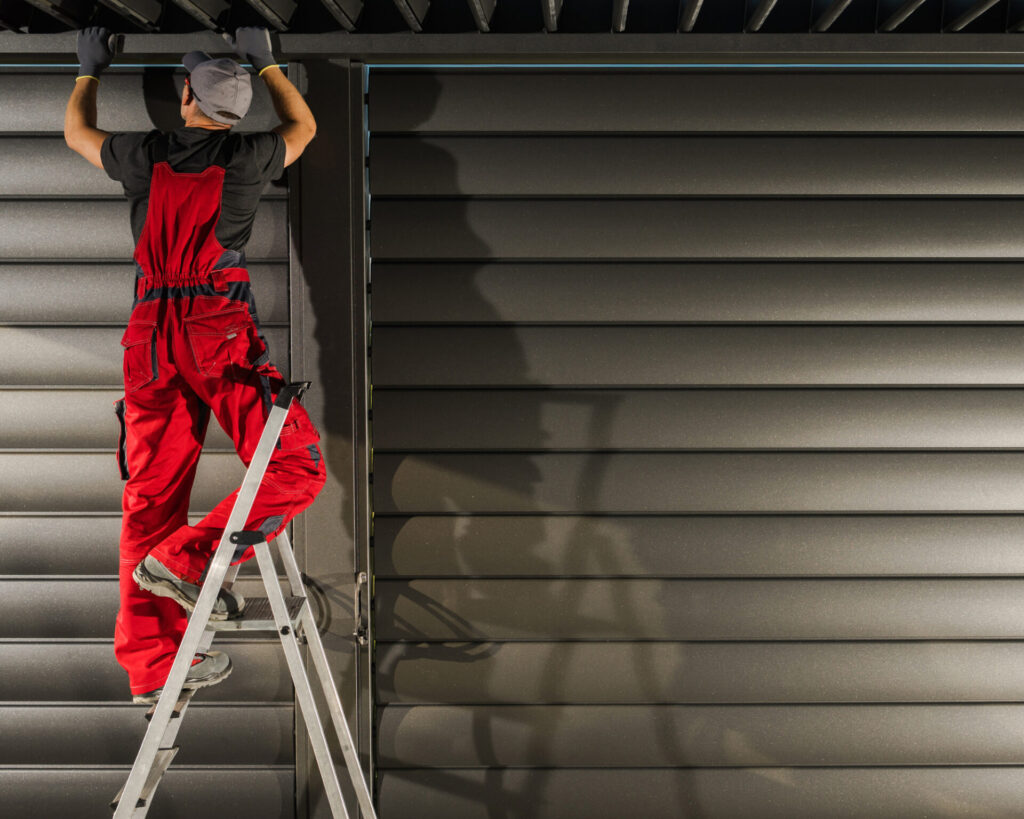
Comparison: Aluminium Cladding Vs Other Cladding Materials
When it comes to choosing the right cladding material for your home or commercial building, the decision can be daunting. The market offers a variety of cladding options, each with its own benefits, costs, and drawbacks. In this section, we’ll dive into a detailed comparison of aluminium cladding with other popular cladding materials—vinyl, timber, and fibre cement. By the end, you’ll have a clearer understanding of the differences and be better equipped to make an informed decision for your project.
Vinyl Cladding
Cost Comparison and Key Differences
Vinyl cladding is often regarded as a budget-friendly option for exterior finishes. It’s usually less expensive than aluminium cladding, making it an appealing choice for homeowners on a tight budget. However, while it may save money upfront, it’s important to weigh the long-term implications.
- Durability: Vinyl cladding doesn’t have the longevity of aluminium. Although it can last up to 30 years, it is more susceptible to cracking, warping, and fading over time, particularly when exposed to extreme weather conditions. Aluminium cladding, on the other hand, boasts impressive durability, often lasting 40 years or more with little to no maintenance.
- Appearance: When it comes to aesthetics, aluminium cladding tends to offer a sleek and modern appearance. Vinyl cladding is available in a range of colours and styles, but it can sometimes have a plasticky look, especially compared to the high-end finishes available with aluminium.
- Maintenance: Vinyl requires occasional cleaning and may need repairs if damaged, whereas aluminium is virtually maintenance-free. Its resistance to rust, corrosion, and weathering means that it can maintain its appearance for decades without significant upkeep.
Timber Cladding
Cost Comparison, Advantages, and Disadvantages
Timber cladding, known for its natural beauty, comes at a higher price point than vinyl but can vary depending on the type of wood used. It’s typically comparable to aluminium cladding in cost, but the true comparison lies in the trade-offs between the two.
- Advantages: The primary appeal of timber cladding is its warm, organic appearance. It offers a classic, natural look that’s hard to replicate with other materials. For homeowners seeking a rustic or eco-friendly aesthetic, timber is often the preferred choice.
- Disadvantages: The downsides of timber cladding mainly revolve around upkeep and longevity. Wood is highly susceptible to weather damage, insect infestations, and decay. To maintain its appearance and structural integrity, timber cladding requires regular maintenance, including staining, sealing, and repairs. Without consistent care, it can deteriorate much faster than aluminium. Additionally, timber cladding doesn’t perform as well in areas with high humidity or frequent rain.
When considering timber vs. aluminium, it’s essential to weigh the charm of wood against the practicality and low-maintenance appeal of aluminium.
Fibre Cement Cladding
Cost Differences and When Fibre Cement Might Be a Better or Worse Choice Than Aluminium
Fibre cement cladding strikes a balance between cost and durability, sitting between vinyl and aluminium in terms of price. It’s more expensive than vinyl but often slightly less costly than aluminium, depending on the manufacturer and specific product.
- Advantages: Fibre cement cladding is highly durable and can mimic the appearance of timber, brick, or stone at a lower cost. It’s resistant to rot, insects, and fire, making it an appealing choice for those who want a strong, versatile material. In many cases, it outperforms aluminium in terms of fire resistance, which can be a crucial factor depending on your location and building code requirements.
- Disadvantages: However, fibre cement is heavier and more challenging to install, which can increase labour costs. It’s also prone to cracking if not installed correctly or if subjected to significant impacts. While fibre cement is low maintenance, it still requires occasional repainting and cleaning. In comparison, aluminium cladding generally requires less upkeep over its lifetime and is less prone to impact damage or cracking.
- When to Choose Fibre Cement: Fibre cement may be a better option if fire resistance is a top priority or if you’re seeking a cladding material that can imitate the appearance of more expensive materials like stone or brick. However, if longevity, ease of installation, and minimal maintenance are more important, aluminium cladding could be the superior choice.
Ultimately, the decision between aluminium cladding and other materials such as vinyl, timber, or fibre cement depends on various factors, including your budget, aesthetic preferences, and maintenance tolerance. Aluminium cladding stands out for its durability, sleek appearance, and minimal maintenance needs, but vinyl may be a more economical choice for budget-conscious homeowners, while timber appeals to those looking for a natural, timeless aesthetic. Fibre cement, meanwhile, offers a middle ground with fire resistance and versatility but may not match the long-term durability of aluminium. By weighing the pros and cons of each material, you can select the cladding that best suits your project, climate, and lifestyle.
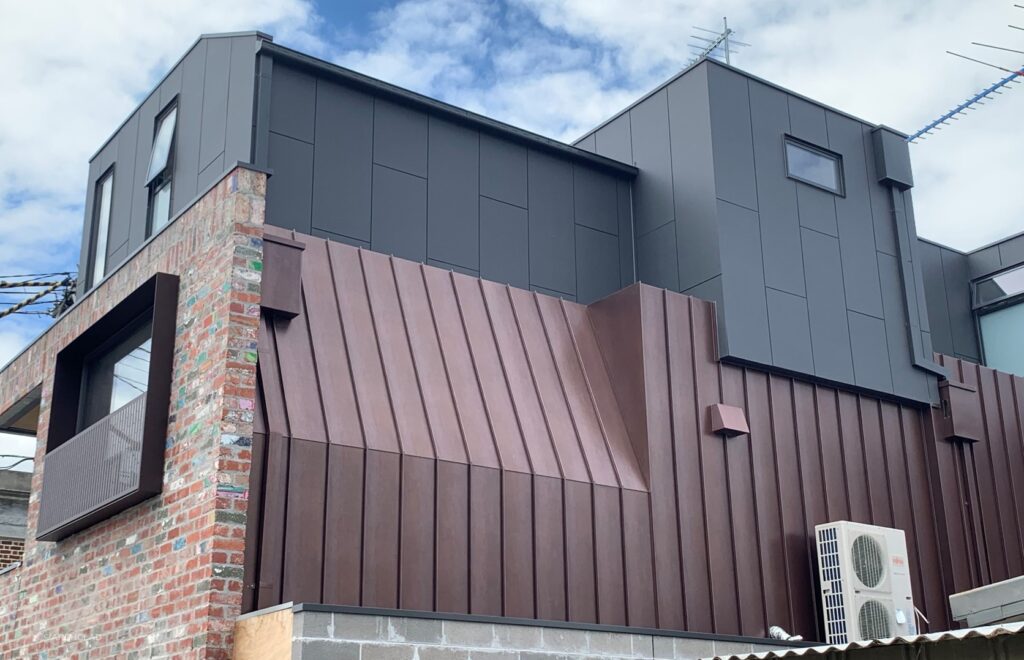
Why Choose Aluminium Cladding For Your NZ Property
Aluminium cladding has become an increasingly popular choice for homeowners across New Zealand. It’s not just because of its modern appeal but due to several practical benefits that make it ideal for New Zealand’s unique environment. If you’re contemplating an upgrade for your property, here’s why aluminium cladding should be at the top of your list.
Durability and Longevity
New Zealand is known for its diverse and sometimes harsh weather conditions. From intense UV exposure in summer to heavy rain and wind in the colder months, homes are constantly subjected to environmental wear and tear. Aluminium cladding offers exceptional durability, making it a perfect match for these conditions.
Aluminium doesn’t rust, corrode, or warp when exposed to the elements, which is a huge advantage in areas prone to high rainfall or coastal exposure. Its resistance to corrosion is particularly beneficial for homes near the coast, where saltwater air can deteriorate many other materials over time. In fact, aluminium’s natural oxide layer forms a protective barrier, helping it withstand whatever nature throws its way. This durability ensures your home remains well-protected for decades, without the constant need for repairs or replacements.
Low Maintenance
One of the most appealing features of aluminium cladding is its low-maintenance nature. Unlike timber, which needs frequent painting, sealing, or staining to maintain its appearance, aluminium simply requires the occasional wash to remove dirt or debris. It’s highly resistant to pests like termites and doesn’t absorb moisture, meaning there’s no risk of rot or decay.
For busy homeowners or property investors, this translates to fewer hours spent on upkeep and lower ongoing maintenance costs. It’s a material that stays looking sharp and sleek with minimal effort, giving you peace of mind while preserving the aesthetic of your property for years.
Energy Efficiency
In an era where energy efficiency is more important than ever, aluminium cladding offers a surprising benefit. Its reflective properties help to reduce the amount of heat absorbed by your home, which can significantly cut down on cooling costs during hot New Zealand summers. By deflecting the sun’s rays rather than absorbing them, aluminium cladding keeps your home cooler, contributing to a more energy-efficient living environment.
This energy efficiency isn’t just a win for your wallet—it’s also an environmentally friendly choice. With the growing emphasis on sustainable living, choosing materials that contribute to reduced energy consumption helps lower your carbon footprint, making aluminium cladding a responsible option for eco-conscious homeowners.
Aesthetic Flexibility
Beyond its practical benefits, aluminium cladding offers a strikingly modern, sleek aesthetic that can elevate the appearance of any home. Whether you’re going for a contemporary look or something more traditional, aluminium cladding is incredibly versatile, with a wide array of finishes, textures, and colors available to suit your vision.
From sleek matte finishes to more textured or woodgrain-like options, aluminium cladding allows you to customize your exterior to reflect your style while maintaining a clean, polished look. It’s a material that effortlessly combines form and function, offering both visual appeal and long-lasting performance.
Choosing aluminium cladding for your NZ property is not just a practical decision—it’s a long-term investment. It provides robust protection against New Zealand’s ever-changing climate while requiring minimal maintenance, improving energy efficiency, and offering a stylish finish to your home. If you’re looking for a durable, low-maintenance cladding option that adds value and beauty to your property, aluminium is an excellent choice.
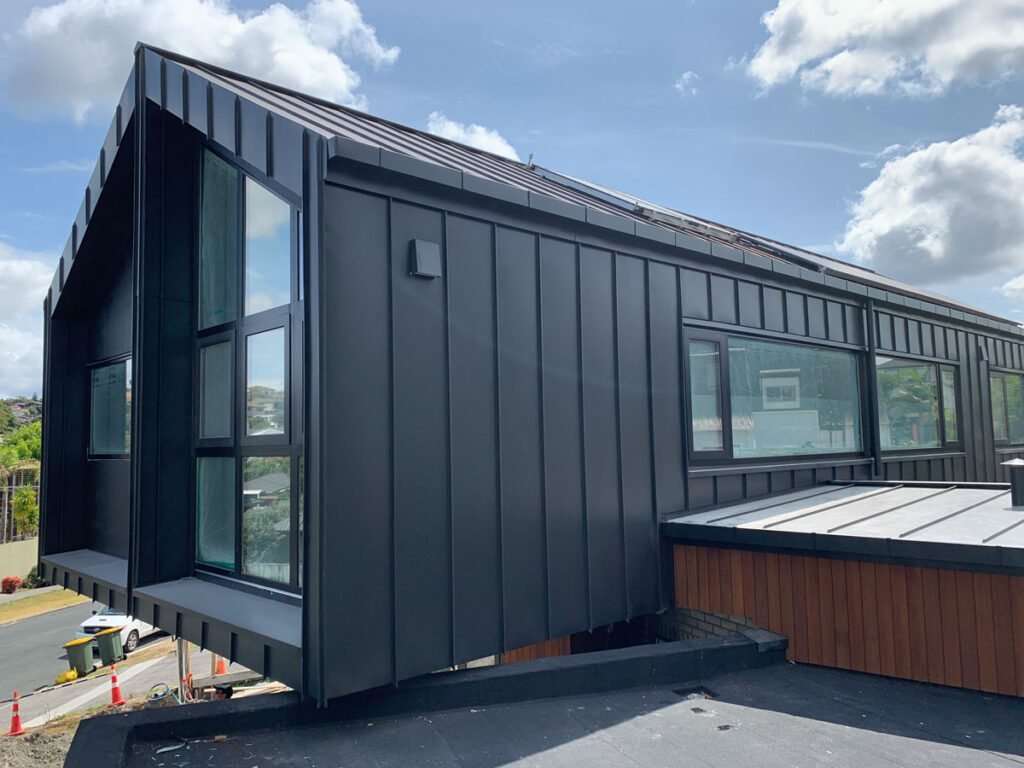
How To Estimate The Total Cost Of Your Aluminium Cladding Project
Estimating the total cost of your aluminium cladding project is essential for staying within your budget and avoiding any surprises along the way. Here’s a detailed guide to help you accurately calculate the costs involved, ensuring a smooth and stress-free cladding project from start to finish.
Measuring Your Building
The first step in estimating the total cost of your aluminium cladding project is measuring the external surface area of your building. This is a crucial step as it determines the amount of material you will need. Here’s how to go about it.
- Prepare the Tools: You will need a tape measure, a notepad, and a calculator. If possible, digital measuring tools can provide more precise measurements, especially for larger projects.
- Divide the Building into Sections: Break down the exterior of your building into manageable sections, such as walls, windows, doors, and any other structural features. For each section, take note of the height and width.
- Measure Each Section: Start by measuring the height and width of each wall individually. Multiply these numbers together to get the total square footage of each section. For example, if a wall is 10 meters wide and 5 meters high, the area would be 50 square meters.
- Subtract Openings: Once you have the total surface area, subtract the area of any windows, doors, or other openings. You don’t want to include these spaces in your cladding material calculations, as they won’t require cladding. Measure the height and width of each opening, then multiply those numbers together to get the area. Subtract this from your overall square meter total.
- Calculate Total Square Meters: Add up the square footage of each section and subtract the openings. This will give you the total square meters that need to be covered with aluminium cladding.
- Factor in Extra Material: It’s always a good idea to order more material than you think you’ll need, especially if your building has complex shapes or features. Typically, adding an extra 5-10% to your total square meter calculation is sufficient to account for wastage or cutting errors.
By following these steps, you’ll have a solid understanding of the material requirements for your aluminium cladding project, which forms the foundation of your cost estimation.
Requesting Quotes
Once you have a clear idea of the material requirements, the next step is to gather quotes from contractors. Here are some tips to keep in mind when requesting quotes.
- Ask for Detailed Breakdown: When reaching out to contractors in New Zealand, it’s essential to request a detailed breakdown of costs. This should include the cost of materials, labor, and any additional fees, such as scaffolding, equipment hire, or waste disposal. A detailed breakdown allows you to understand where your money is going and helps you compare quotes more effectively.
- Check for Inclusions: Make sure to ask the contractor what is included in their quote. For instance, does the price include the cost of site preparation, such as removing existing cladding or repairing the surface? Does it cover the delivery of materials? Understanding what is and isn’t included will prevent unexpected charges later on.
- Get Multiple Quotes: Don’t settle for the first quote you receive. Instead, get at least three quotes from different contractors. This not only helps you find a competitive price but also gives you an idea of the standard costs for your project. Comparing quotes will also allow you to spot any inconsistencies or red flags.
- Look for Experience and Expertise: While price is important, don’t make your decision solely on cost. Look for contractors with proven experience in aluminium cladding projects. Ask to see examples of previous work and check for any certifications or industry accreditations.
Budgeting for Contingencies
Even with the best planning, construction projects often come with unforeseen challenges. That’s why it’s wise to budget for contingencies. Here’s how to do it.
- Allocate 10-20% for Contingencies: When planning your budget, it’s advisable to set aside an additional 10-20% of your total project cost for contingencies. This cushion can help cover unexpected costs such as delays in construction, changes in design, or an increase in material prices.
- Plan for Design Changes: Sometimes, once work has started, you may decide that you want to change the design or materials. These changes can increase the cost, so having a contingency budget in place will allow you to make adjustments without derailing your project.
- Account for Rising Material Costs: Material costs can fluctuate due to various factors, such as supply chain issues or market demand. By including a buffer in your budget, you’ll be prepared if prices rise unexpectedly.
- Prepare for Delays: Weather, supplier delays, or unforeseen site issues can sometimes cause delays. These delays can lead to increased labor costs or the need to hire equipment for longer than anticipated. Having extra funds in your budget will help manage these situations without stress.
By following these tips, you can create a more accurate and realistic budget for your aluminium cladding project, ensuring you are prepared for any challenges that may arise.
Estimating the total cost of your aluminium cladding project involves careful planning, accurate measurements, and thorough research. By measuring your building’s surface area, gathering detailed quotes from contractors, and budgeting for contingencies, you can approach your cladding project with confidence and control. Doing this legwork upfront will not only help you avoid unexpected costs but also ensure that your project stays on track and within budget.
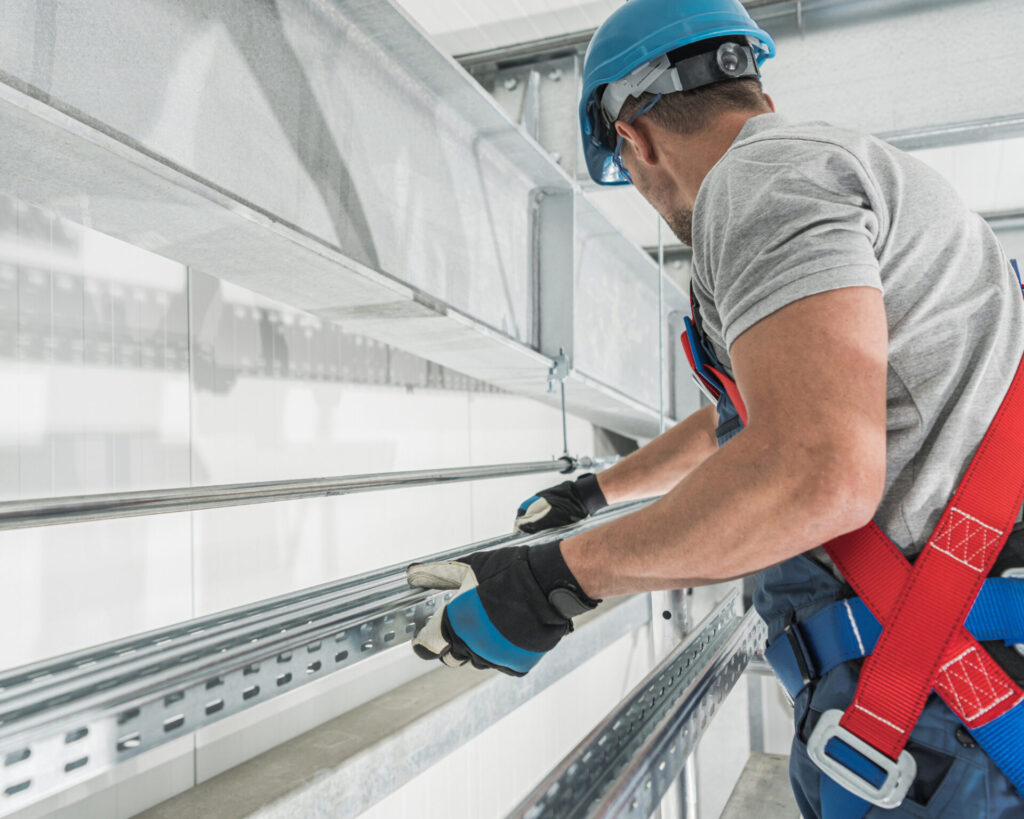
Tips For Reducing Aluminium Cladding Costs In NZ
Aluminium cladding is a popular choice for many New Zealanders due to its durability, sleek appearance, and low maintenance requirements. However, the costs associated with installation can add up quickly. Fortunately, there are several smart strategies you can implement to help reduce these expenses without compromising on quality. Below, we explore practical tips that homeowners and builders in New Zealand can use to cut down on aluminium cladding costs.
Sourcing Locally
One of the most effective ways to reduce aluminium cladding costs in New Zealand is to source materials locally. Choosing local suppliers and contractors can have several advantages. For starters, you can avoid hefty import taxes that are often associated with purchasing materials from overseas. Additionally, when you source locally, you can save significantly on transport costs. Shipping large quantities of aluminium from overseas can be expensive, especially given New Zealand’s geographical isolation. By buying locally, you’re not only supporting the local economy, but you’re also reducing the overall cost of your project.
Beyond cost savings, sourcing local materials allows for quicker turnaround times, meaning your project is less likely to face delays due to shipping issues. Local suppliers often have established relationships with local builders, creating a smoother workflow for your cladding installation.
Bulk Purchasing
If you’re working on a large-scale project, such as cladding an entire building or multiple units, buying your aluminium cladding materials in bulk can lead to considerable savings. Many suppliers offer discounted rates for bulk purchases, and even a slight reduction in price per square meter can add up to substantial savings over a large area.
When you purchase in bulk, you also reduce the likelihood of needing additional orders later in the project, which could be subject to fluctuating material costs or added transport fees. Planning ahead and working with your supplier to negotiate bulk rates can keep your project within budget and help you stretch your dollars further.
Off-Season Installation
Another cost-saving tip is to schedule your aluminium cladding installation during the off-peak season. In New Zealand, demand for construction and renovation services typically peaks during the warmer months, particularly in the spring and summer. During this time, contractors are in high demand, which can drive up labour costs.
By scheduling your installation in the off-season, such as during the colder winter months, you may find that contractors are more available and willing to offer lower rates to secure work. While winter weather may seem less ideal for construction, modern cladding materials and installation methods allow for work to continue in most conditions. The trade-off can be a significant reduction in labour costs, making the timing of your installation a key factor in controlling your overall budget.
DIY vs. Hiring Professionals
One of the biggest cost-related decisions you’ll need to make is whether to take on a DIY installation or hire professionals. Each option has its own set of advantages and drawbacks.
Attempting a DIY installation can certainly reduce labour costs, as you won’t need to pay a contractor. If you have some construction experience and are confident in your abilities, this could be a viable option. However, it’s important to note that aluminium cladding installation requires precision and expertise to ensure the panels are properly aligned, sealed, and secured. Mistakes during a DIY installation could lead to increased costs down the line due to repairs or reinstallation. Additionally, an improperly installed cladding system could compromise your home’s weatherproofing and energy efficiency.
On the other hand, hiring a skilled professional brings peace of mind. Contractors who specialise in aluminium cladding are familiar with the best practices for installation, ensuring that the job is done correctly the first time. While this does involve higher upfront costs for labour, the long-term benefits of a professional installation often outweigh the savings from a DIY approach. For many homeowners, hiring professionals can be a more cost-effective choice in the long run by preventing costly errors and ensuring the longevity of the cladding system.
Reducing aluminium cladding costs in New Zealand requires thoughtful planning and strategic decision-making. Sourcing materials locally, taking advantage of bulk purchasing, scheduling installations during off-peak seasons, and weighing the pros and cons of DIY versus professional installation can all help you save on your cladding project. By implementing these tips, you can ensure that your aluminium cladding project remains within budget while still delivering a high-quality result that enhances the durability and aesthetic appeal of your home or building.
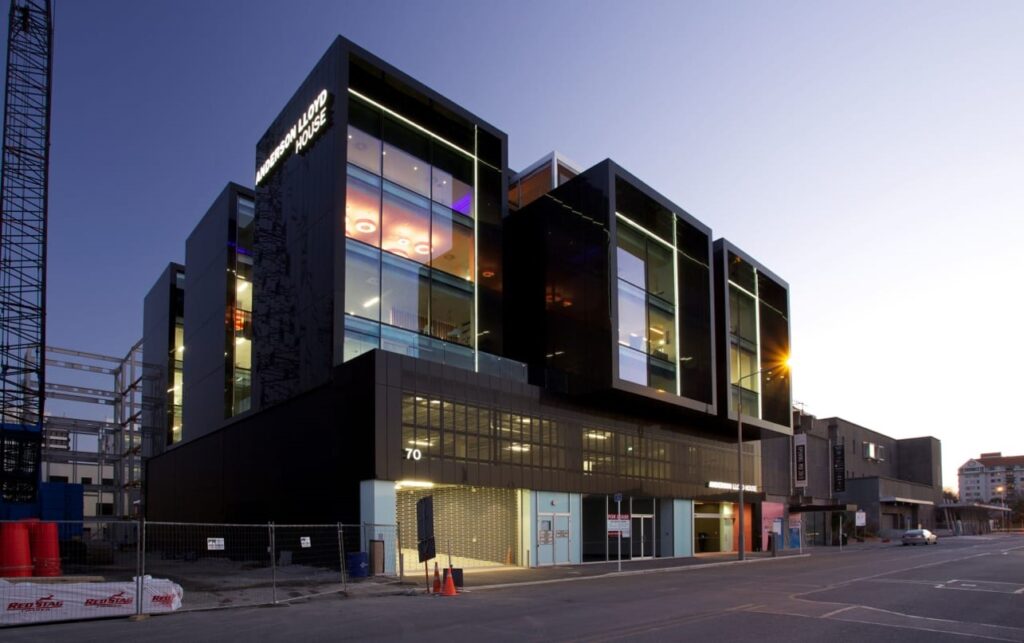
Case Studies: Real-Life Aluminium Cladding Projects In New Zealand
When considering aluminium cladding for construction projects, real-life examples can offer valuable insight into its practical application, cost-effectiveness, and aesthetic value. In New Zealand, both residential and commercial buildings have embraced this durable, low-maintenance material, and the following case studies provide a closer look at the impact of aluminium cladding on various projects.
Example 1: A Residential Home in Auckland
The Project: A modern family in Auckland sought to renovate their home with a focus on durability, energy efficiency, and a sleek, contemporary look. After exploring various exterior cladding options, they decided on aluminium cladding for its minimal upkeep, resistance to harsh weather conditions, and stylish appearance.
Challenges Faced: The family faced some initial challenges during the selection process, such as finding the right supplier and ensuring the cladding would complement their existing architectural design. Additionally, there were concerns about potential heat retention due to Auckland’s warm summers.
Installation and Costs: The total cost for installing aluminium cladding on their 220 square meter home came to approximately NZD $60,000, which included both materials and labor. This cost breakdown is as follows:
- Materials: NZD $40,000 – High-quality aluminium panels designed to withstand New Zealand’s varying climate.
- Labor: NZD $15,000 – Professional installation, including preparation and weatherproofing.
- Miscellaneous: NZD $5,000 – Scaffolding, delivery fees, and any necessary repairs.
End Result: The family was highly satisfied with the finished project. The aluminium cladding gave the home a modern, polished look while providing excellent insulation and weather resistance. Notably, the material’s low maintenance and longevity made it a cost-effective solution in the long run, eliminating the need for frequent repainting or repairs. The project was completed within six weeks, and the family immediately noticed improved energy efficiency, with the home feeling cooler in summer and warmer in winter.
Example 2: A Commercial Building in Christchurch
The Project: A large-scale commercial office building in Christchurch was undergoing a significant renovation to modernize its exterior and improve energy efficiency. The project involved cladding a 1,500 square meter surface area using aluminium panels. The aim was to not only update the look of the building but also to take advantage of economies of scale to minimize costs.
Economies of Scale: One of the primary benefits of this commercial project was the ability to leverage bulk purchasing and large-scale installation. The developers were able to negotiate lower material costs due to the volume required, and installation efficiencies were achieved through repeated processes across the building’s uniform facade.
Installation Process: The installation was conducted over the course of 12 weeks, with the aluminium cladding being installed in sections to ensure the building could remain operational throughout the renovation. The process involved:
- Site Preparation: Ensuring the surface was smooth, clean, and ready for cladding.
- Cladding Installation: Aluminium panels were attached using a hidden fastener system, which provided a clean, seamless look while allowing for thermal expansion.
- Final Touches: Sealing joints and adding protective coatings to enhance durability and weatherproofing.
Cost Breakdown
- Materials: NZD $450,000 – Bulk pricing significantly reduced costs per square meter.
- Labor: NZD $200,000 – Skilled labor required for the intricate and large-scale installation.
- Logistics and Permits: NZD $50,000 – Included scaffolding, permits, and specialized equipment.
End Result:
The project successfully modernized the building’s appearance while enhancing energy efficiency. The sleek, metallic finish provided by the aluminium cladding improved the building’s thermal performance, reducing heating and cooling costs by up to 20%. Additionally, the building’s value increased due to the updated aesthetic and enhanced durability. Despite the large scale of the project, the economies of scale helped keep costs manageable, and the client was pleased with the quick turnaround and minimal disruption to their business operations.
These two case studies in New Zealand illustrate the versatility and benefits of aluminium cladding in both residential and commercial settings. For the Auckland family, aluminium cladding offered a modern, maintenance-free exterior that enhanced their home’s energy efficiency and weather resistance. Meanwhile, the Christchurch commercial project showcased how economies of scale can reduce costs and streamline the installation process in large-scale developments. Aluminium cladding continues to be a popular choice for property owners looking to combine aesthetics, durability, and sustainability, making it a smart investment for any building project.
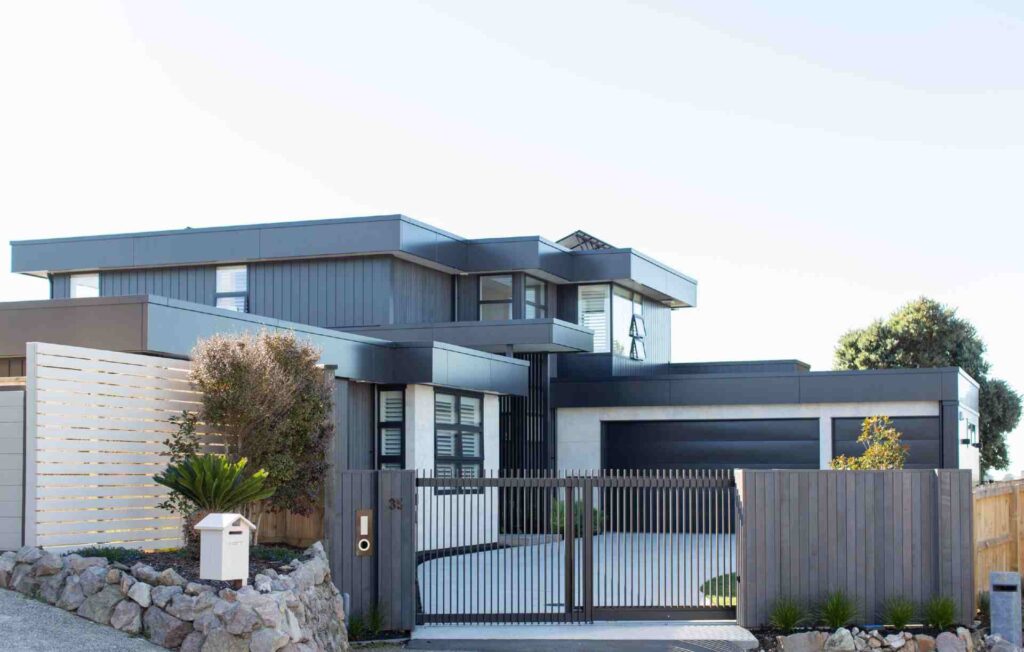
Answering Common Questions About Aluminium Cladding Costs In NZ
Is Aluminium Cladding Worth the Investment
When considering the costs of aluminium cladding, it’s essential to balance the initial investment against the long-term benefits. While aluminium cladding might come with a higher upfront cost compared to other materials, such as timber or vinyl, its durability, low maintenance requirements, and sleek modern aesthetic make it a worthwhile investment for many property owners in New Zealand. Over time, the reduced need for repairs or replacements, combined with its ability to withstand the elements, can lead to significant savings. Moreover, aluminium cladding can improve energy efficiency by reflecting heat, potentially lowering cooling costs in warmer months. If you’re looking for a material that offers longevity, minimal upkeep, and strong visual appeal, aluminium cladding is often well worth the initial expense.
How Does Climate Affect the Durability of Aluminium Cladding in NZ
New Zealand’s climate is famously diverse, ranging from subtropical in the north to temperate and alpine in the south. Aluminium cladding is a highly durable material, making it well-suited to withstand these varying weather conditions. It is resistant to corrosion, which is particularly beneficial in coastal regions where saltwater can cause significant wear and tear on other materials. Additionally, aluminium’s natural resistance to UV rays helps prevent fading or warping, even in areas that experience intense sunlight. In colder regions, aluminium cladding offers strong protection against frost and snow. Given New Zealand’s wide range of climates, the durability of aluminium cladding makes it a reliable choice that can protect your property against weather extremes across the country.
Can Aluminium Cladding Be Installed on Older Buildings
One of the major advantages of aluminium cladding is its adaptability. Whether you are working on a new build or retrofitting an older structure, aluminium cladding can often be tailored to suit your needs. For older buildings, aluminium cladding can provide a modern facelift without the need for extensive structural alterations. It’s lightweight, which means it places minimal stress on the existing framework, making it a viable option for older homes or commercial properties that may not be able to support heavier materials like brick or stone. Additionally, aluminium cladding can be customized to complement the architectural style of older buildings, blending modern performance with classic design. This flexibility makes it an ideal option for enhancing the exterior of older properties while ensuring long-lasting protection.
These offer valuable insights into aluminium cladding, helping property owners in New Zealand understand its costs, durability, and adaptability. Whether you’re considering it for a new build or looking to update an older property, aluminium cladding presents a strong case for being a worthwhile investment, especially given the range of climates across the country.
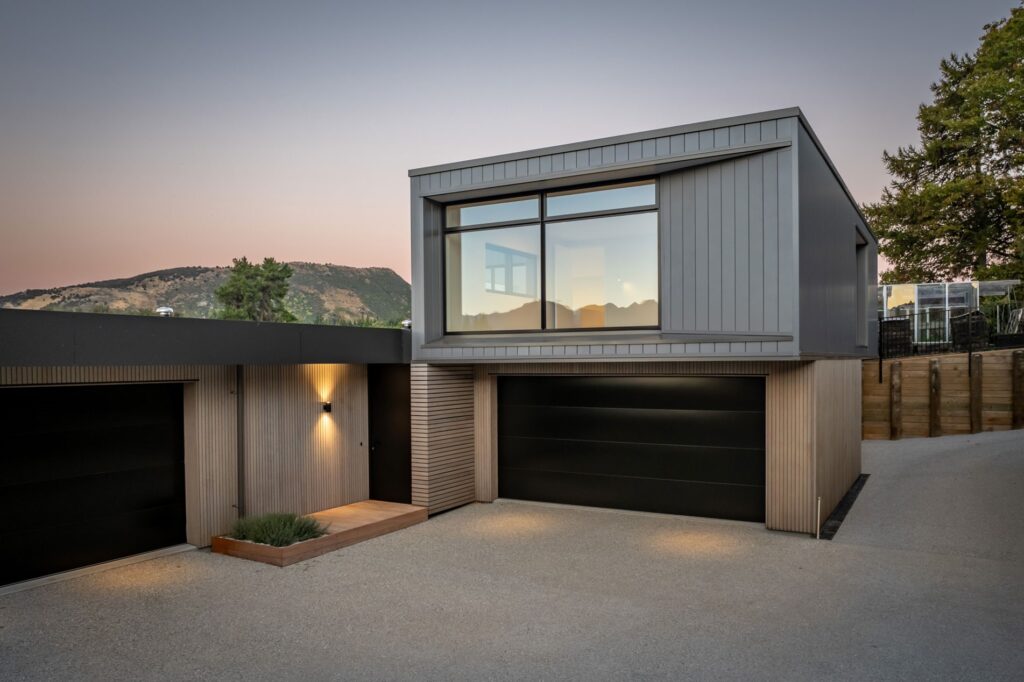
FAQs: About Aluminium Cladding Cost Per M2 In NZ
Conclusion
To wrap up, aluminum cladding offers an affordable, durable, and aesthetically pleasing option for both residential and commercial properties. Key factors influencing the cost include the type of aluminum used, the size of the project, and installation requirements, while the benefits range from weather resistance to energy efficiency. If you’re considering aluminum cladding for your next renovation project, now is the time to explore your options by reaching out to local suppliers for detailed quotes. To stay informed about the latest trends and materials in building, subscribe to our newsletter or download our cost-estimate checklist for aluminum cladding today.
Find A Professional Cladding Company Near You!
Cladding Warkworth
Cladding Christchurch
Leaky Home Repairs Auckland
Cladding Auckland
Cladding Hamilton
Cladding Napier
Cladding Hastings
Cladding Hawkes Bay
Cladding Specialists Wellington
About the Author:
Mike Veail is a recognized digital marketing expert with over 6 years of experience in helping tradespeople and small businesses thrive online. A former quantity surveyor, Mike combines deep industry knowledge with hands-on expertise in SEO and Google Ads. His marketing strategies are tailored to the specific needs of the trades sector, helping businesses increase visibility and generate more leads through proven, ethical methods.
Mike has successfully partnered with numerous companies, establishing a track record of delivering measurable results. His work has been featured across various platforms that showcase his expertise in lead generation and online marketing for the trades sector.
Learn more about Mike's experience and services at https://theleadguy.online or follow him on social media: