Welcome to your ultimate guide on the cost of concrete in NZ! Whether you’re a homeowner planning a driveway upgrade, a DIY enthusiast looking to tackle your next project, or simply curious about the price breakdown, understanding the true cost of concrete is crucial before diving in. Concrete is one of the most popular and versatile construction materials in New Zealand, valued for its durability, affordability, and wide range of uses, from patios and driveways to house foundations. In this post, we’ll break down the typical costs of concrete in NZ, the factors that influence pricing, and how you can save money on your project while ensuring quality results. Let’s get started!
On average, the cost of concrete in NZ ranges from $150 to $300 per cubic meter, depending on factors such as the type of concrete, project complexity, location, and additional fees like delivery and labor.
- What Is Concrete And Why Is It Important?
- How Much Does Concrete Cost In NZ?
- Factors That Affect The Cost Of Concrete In NZ
- Types Of Concrete And Their Costs
- Tips To Save Money On Your Concrete Project
- What To Expect When Hiring A Contractor
- Environmental Impact And Sustainable Options For Concrete In NZ
- FAQs: About Cost Of Concrete NZ
- Conclusion
- Find A Professional Concrete Company Near You!
What Is Concrete And Why Is It Important?
Concrete is one of the most fundamental building materials in the world. In its simplest form, concrete is a mixture of cement, sand, gravel, and water. The cement acts as a binder that, when mixed with water, hardens and binds the aggregate materials (sand and gravel) together. This combination creates a solid and durable material that can withstand significant weight and pressure. Once the concrete has cured—through a process of chemical reactions called hydration—it becomes incredibly strong and resilient, making it essential for construction projects of all sizes.
Why Is Concrete So Important?
Concrete is crucial because of its strength, versatility, and longevity. It forms the backbone of most modern structures, from towering skyscrapers to simple garden pathways. Its ability to be molded into almost any shape while wet and its enduring toughness after curing make it indispensable in construction. Without concrete, our buildings, roads, and infrastructure wouldn’t stand the test of time.
Applications of Concrete in New Zealand
In New Zealand, concrete is a preferred material for many home and construction projects. Kiwi homeowners commonly use concrete for driveways, providing a solid, low-maintenance surface that can handle heavy vehicles and resist weathering. Patios and outdoor entertaining areas are also frequently built with concrete, valued for its durability and modern aesthetic.
Concrete is essential in the foundations of homes, offering the stability required to support structures over time, even in areas prone to earthquakes. Concrete flooring has also gained popularity, with polished concrete becoming a stylish, durable option for both indoor and outdoor spaces. Moreover, concrete retaining walls are often used in landscaping to manage slopes and prevent soil erosion in New Zealand’s varied terrain.
The Growing Demand for Concrete in NZ
New Zealand is experiencing a boom in construction, driven by factors such as housing shortages and an increase in home renovations. This has led to a growing demand for concrete, especially as the trend of modern, minimalist home designs continues to rise. New subdivisions, multi-unit housing projects, and infrastructure developments across the country all require substantial quantities of concrete. Additionally, as homeowners look to upgrade or expand their living spaces, concrete remains a popular choice due to its durability, cost-effectiveness, and wide range of applications. Whether it’s laying the foundation for new homes or enhancing outdoor living areas, concrete is a key player in shaping the future of construction in New Zealand.
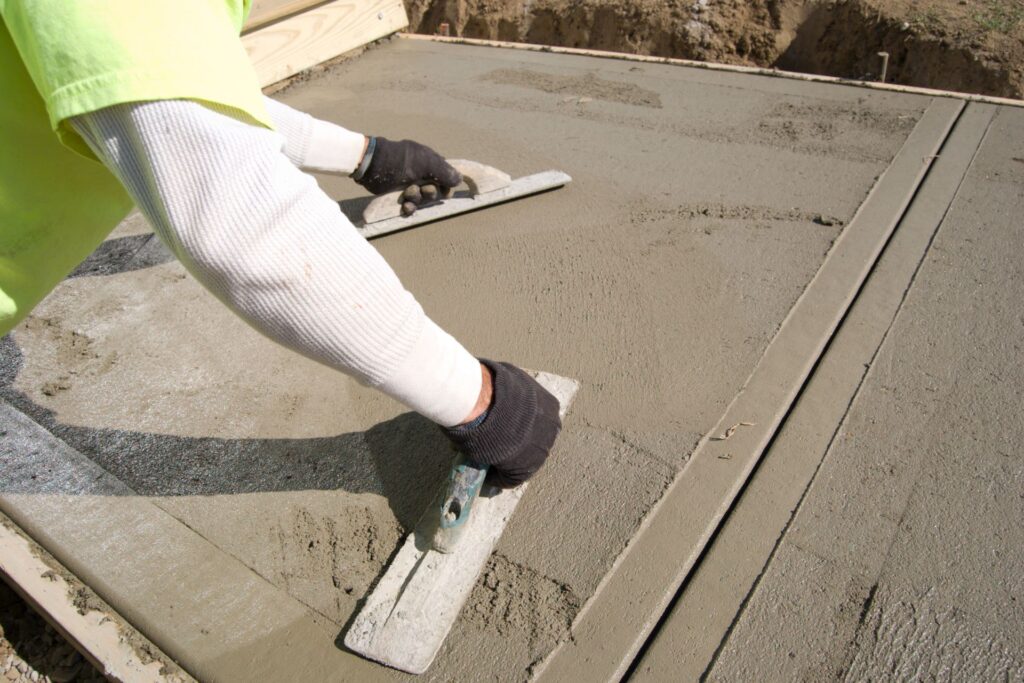
How Much Does Concrete Cost In NZ?
When you’re planning a project that involves concrete, one of the most important factors to consider is cost. In New Zealand, the price of concrete can vary significantly depending on several factors, from the type of project to the region you’re located in. Understanding these variables can help you budget more accurately and avoid unexpected expenses.
Average Cost of Concrete in NZ
In New Zealand, the average cost of concrete generally ranges between $150 to $300 NZD per cubic meter. However, this price can fluctuate based on your location, the quality of the concrete, and the supplier you’re working with. For instance, regions with higher demand or those further from suppliers may experience higher costs due to transportation and logistical expenses. It’s essential to check with local suppliers for the most accurate and up-to-date pricing specific to your area.
Breaking Down the Cost
To understand what contributes to the overall price of concrete, let’s break down the various factors that influence the total cost.
Raw Material Costs
The core components of concrete include cement, sand, gravel, and water. Each of these materials contributes to the cost of the final product:
- Cement: The primary binding agent in concrete, cement prices can vary depending on quality and supplier. Generally, higher-grade cement will cost more but may provide better durability.
- Sand and Gravel: These aggregates make up the bulk of the concrete mix. Prices may depend on local availability and quality, with premium aggregates potentially increasing the cost.
- Water: While water may seem insignificant in terms of cost, the quality and amount of water used can influence the overall strength and workability of the concrete mix.
Labor Costs
Hiring professionals to pour and finish your concrete adds another significant expense to your project. Labor costs can vary depending on the complexity of the job and the contractor’s rates. Generally, contractors charge either by the hour or per project, with labor costs ranging from $50 to $100 NZD per hour. If your project is more intricate, such as stamped or polished concrete, you can expect these rates to be higher due to the specialized skills and time required.
Additional Fees
Beyond raw materials and labor, there are often additional fees associated with concrete projects that can affect your overall cost:
- Delivery Charges: If you’re ordering concrete from a supplier, expect to pay delivery fees. These can range from $60 to $200 NZD, depending on your location and the amount of concrete required.
- Mixing Fees: For ready-mix concrete, suppliers may charge a mixing fee, especially for small loads. This fee helps cover the costs of preparing and transporting smaller quantities of concrete.
- Add-ons: Depending on the project, you may need to include extra costs for items like reinforcement (steel rebar or mesh), site preparation, or finishing materials like sealants.
Examples of Concrete Projects and Their Costs
To provide a clearer idea of what concrete projects might cost, here are some real-world examples that are common in New Zealand:
Concrete Driveway
A standard concrete driveway typically costs between $65 and $150 NZD per square meter, depending on factors such as thickness, quality of materials, and any additional design features like decorative finishes. For an average driveway of around 30 square meters, you might expect to pay anywhere from $2,000 to $4,500 NZD.
Concrete Patio
For a small patio area, say around 10 square meters, the cost typically ranges from $1,000 to $3,000 NZD. This includes the price of the concrete, labor, and any additional features such as colored or stamped designs.
Concrete Foundations for a Home Extension
Laying concrete foundations for a home extension is a more substantial project, usually costing between $5,000 to $15,000 NZD. This cost depends on the size of the extension, the complexity of the foundation, and any additional requirements like waterproofing or extra reinforcement.
Final Thoughts
When planning a concrete project in New Zealand, it’s important to consider all these factors to get an accurate idea of the cost. The price of concrete per cubic meter is just one piece of the puzzle; you’ll also need to factor in material costs, labor, and any additional fees. Getting multiple quotes from local contractors and suppliers can help you find the best deal for your specific project, ensuring that you stay within budget while achieving the results you want.
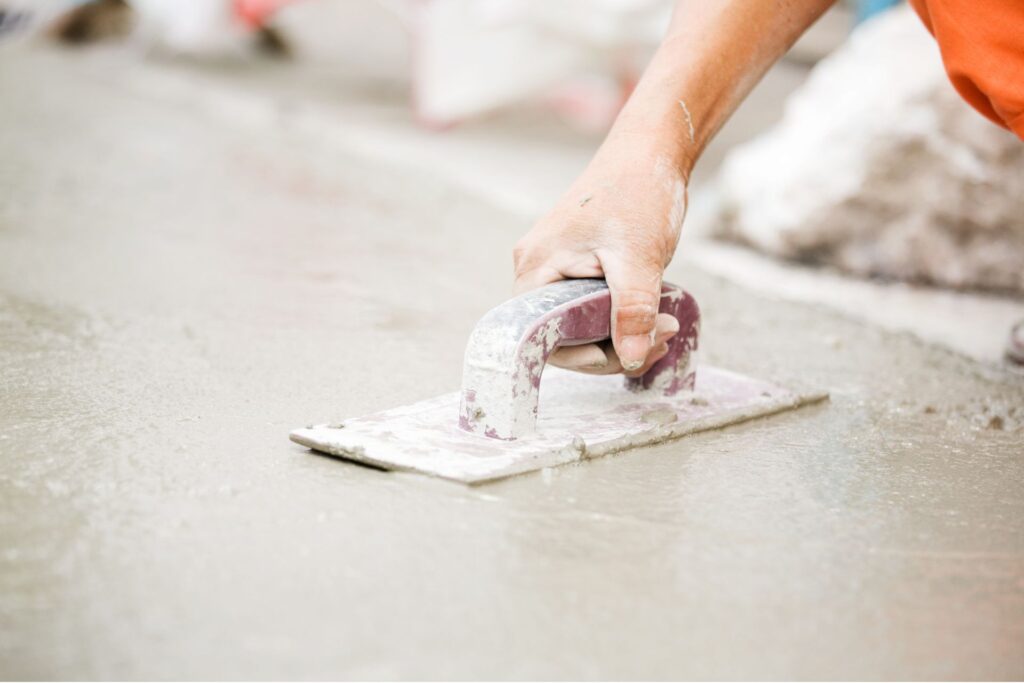
Factors That Affect The Cost Of Concrete In NZ
When considering concrete projects in New Zealand, it’s essential to understand the key factors that influence the overall cost. Concrete pricing can vary significantly depending on a range of variables, from the type of concrete you select to the complexity of the job. Here’s a detailed look at the most significant factors affecting concrete costs in New Zealand.
Material Type
One of the first factors to consider is the type of concrete being used. Not all concrete is created equal, and the choice of material can have a considerable impact on your budget. For instance:
- Standard Concrete is typically the most cost-effective option. It’s commonly used for basic driveways, footpaths, and foundations.
- Colored Concrete adds aesthetic value but comes at a higher price due to the addition of pigments and the specialized mixing process.
- Exposed Aggregate Concrete is another premium option. This type of concrete leaves the aggregate (like stones and pebbles) exposed on the surface, giving a decorative finish. However, the process requires extra materials and labor, which increases the cost.
Choosing between these different types depends on both your budget and the intended function and appearance of the finished surface.
Concrete Thickness and Strength
The thickness and strength of the concrete also play a crucial role in determining the overall cost. Concrete strength is measured in megapascals (MPa), with higher MPa indicating stronger concrete.
- Standard Residential Concrete typically ranges from 20 to 25 MPa, sufficient for driveways and footpaths.
- Heavy-duty concrete might require 30 MPa or more, especially for areas with heavy traffic or industrial use.
Increasing the thickness and strength of the concrete directly raises costs due to the additional material required and the need for higher-grade mixes. A thicker slab or stronger concrete is often needed for structural integrity, particularly for larger-scale projects like commercial developments or heavy vehicle pathways.
Location
Location is a critical factor that can greatly affect the price of concrete in New Zealand. The cost will vary depending on whether your project is in an urban or rural area.
- Urban Areas: In larger cities, competition among suppliers tends to be higher, which can help keep prices lower. However, traffic congestion and parking restrictions may add logistical challenges, potentially increasing labor and transportation costs.
- Rural Areas: In contrast, rural locations may face higher costs due to transportation expenses. If a concrete supplier is far from the construction site, the delivery fees can add up. Additionally, rural areas may have limited supplier options, giving fewer opportunities to negotiate on price.
Ultimately, proximity to a concrete plant and the ease of access to the job site are major factors influencing the final price.
Seasonality and Demand
Concrete costs in New Zealand can fluctuate depending on the time of year and overall demand for construction materials.
- Peak Seasons: During the warmer months (spring and summer), when construction activity is at its highest, concrete prices often rise due to increased demand. Suppliers may charge premium rates as they juggle multiple projects.
- Off-Peak Seasons: Conversely, during colder or rainy months, there may be fewer construction projects, leading to lower prices. However, adverse weather conditions during these months can sometimes delay or complicate concrete pouring, potentially increasing labor costs.
Being strategic about your timing can help you secure better rates, especially if you can plan your project for the off-peak season.
Site Preparation
Another significant cost factor is the amount of site preparation required before the concrete can be poured. The condition of the existing site will influence the extent of the preparatory work needed.
- Minimal Preparation: If the site is already level and clear, preparation costs will be minimal. Simple slab pours over prepared ground usually incur the lowest expenses.
- Extensive Preparation: However, if the ground needs significant grading, excavation, or the removal of old concrete or other structures, the costs will increase. The more complex and time-consuming the site preparation, the higher the labor charges and potential equipment rental fees.
Proper site preparation is essential for ensuring the longevity and quality of the concrete, so it’s worth investing in this stage, even if it adds to the upfront costs.
Complexity of the Project
The complexity of your concrete project is another vital factor that affects pricing.
- Basic Projects: A simple concrete slab, such as a driveway or foundation, is usually the most cost-effective. These projects are straightforward and require minimal custom work.
- Custom or Decorative Work: More intricate designs, such as stamped or decorative concrete, can significantly increase the price. These projects demand additional labor, and specialized tools, and often take longer to complete. Custom designs might also require special mixes, dyes, or finishes, all of which contribute to a higher overall cost.
In addition to the concrete work itself, factors like accessibility to the site and the need for specialized equipment can influence labor and material costs, particularly for complex jobs.
In New Zealand, several factors can affect the cost of concrete for your project. The type of concrete, required thickness and strength, geographic location, seasonal fluctuations, site preparation, and the complexity of the job all play crucial roles in determining the final price. Understanding these factors will not only help you budget more effectively but also ensure that you choose the right type of concrete for your specific needs. By being informed and planning ahead, you can achieve the perfect balance between cost and quality for your concrete project.
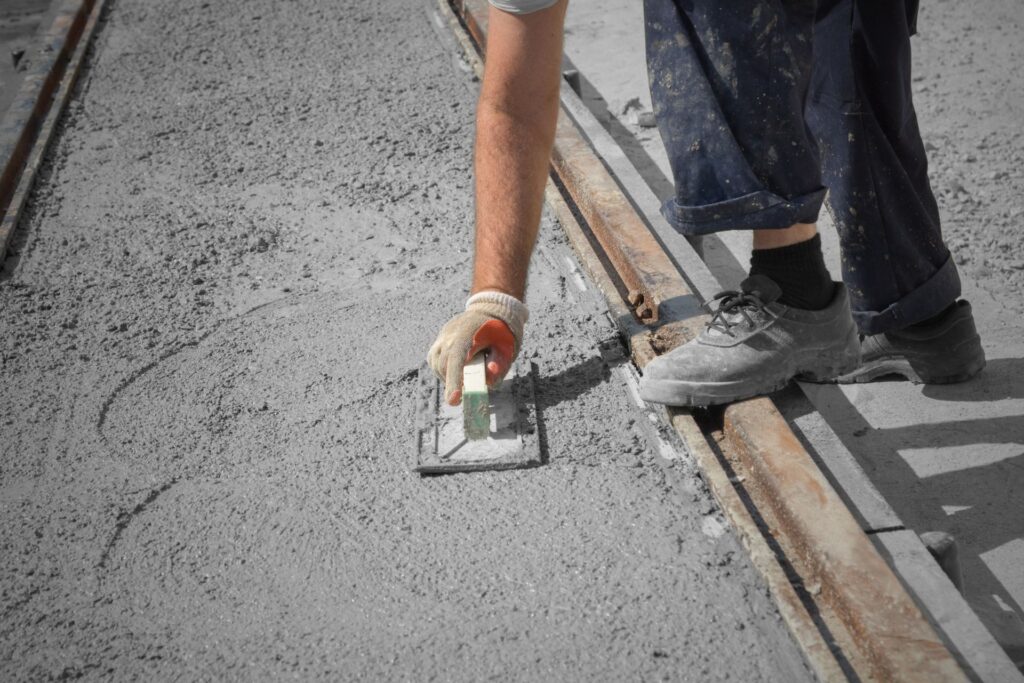
Types Of Concrete And Their Costs
Concrete comes in various forms, each with unique characteristics, advantages, and price points. When planning a construction project, it’s essential to choose the right type of concrete based on your needs and budget. Below, we’ll dive into some of the most common types of concrete and their associated costs.
Standard Concrete
Standard concrete is the most widely used type of concrete in construction, thanks to its simplicity and affordability. It’s the go-to choice for basic foundations, driveways, sidewalks, and general building needs. Standard concrete typically consists of cement, water, and aggregates (such as sand and gravel), making it both cost-effective and reliable.
From a cost perspective, standard concrete is the most economical option, usually ranging from $100 to $150 per cubic yard, depending on the region, supplier, and quality of materials used. For projects that don’t require intricate designs or special finishes, standard concrete offers the best value for money while still ensuring strength and durability.
Decorative Concrete
If you’re looking to add a touch of style to your project, decorative concrete might be the answer. This type of concrete goes beyond functionality to also serve as a design element. Decorative concrete can be stamped, colored, stained, or polished to mimic the appearance of stone, brick, tile, or even wood. Exposed aggregate concrete, which reveals the texture of natural stones, is another popular choice in the decorative category.
However, the beauty of decorative concrete comes at a higher cost. Expect to pay anywhere from $8 to $18 per square foot, depending on the complexity of the design and the materials used. While more expensive than standard concrete, decorative concrete offers unique aesthetic appeal, enhancing the look and feel of patios, walkways, driveways, and even interior floors.
Ready-Mix Concrete
Ready-mix concrete offers convenience and consistency by delivering pre-mixed concrete straight to your job site. This type of concrete is mixed at a central plant and then transported by a truck in the exact quantities needed for your project. The primary advantage of ready-mix concrete is its quality control, ensuring a precise mix every time, which is crucial for large-scale or complex projects.
In terms of cost, ready-mix concrete typically runs between $120 and $150 per cubic yard, with additional fees for delivery, especially for smaller loads. While it may be more expensive than mixing on-site, ready-mix concrete saves time, reduces labor, and minimizes the risk of inconsistent batches. It’s an excellent option for projects where precision and efficiency are critical.
Precast Concrete
Precast concrete refers to concrete elements that are cast and cured in a controlled factory environment before being transported to the construction site. Common precast elements include walls, panels, beams, and stairs. The use of precast concrete can significantly speed up construction time since the pieces arrive ready to install.
The cost of precast concrete varies based on the complexity of the piece, its size, and transportation logistics. Precast concrete panels, for example, can range from $50 to $100 per square foot. While the upfront costs may be higher compared to other types of concrete, the efficiency, quality control, and long-term durability often make precast concrete a cost-effective solution for larger projects or those with specific architectural requirements.
Choosing the right type of concrete depends on your project’s scope, design preferences, and budget. Whether you prioritize cost, convenience, or aesthetics, understanding the various types of concrete and their costs can help you make an informed decision that meets your construction goals.
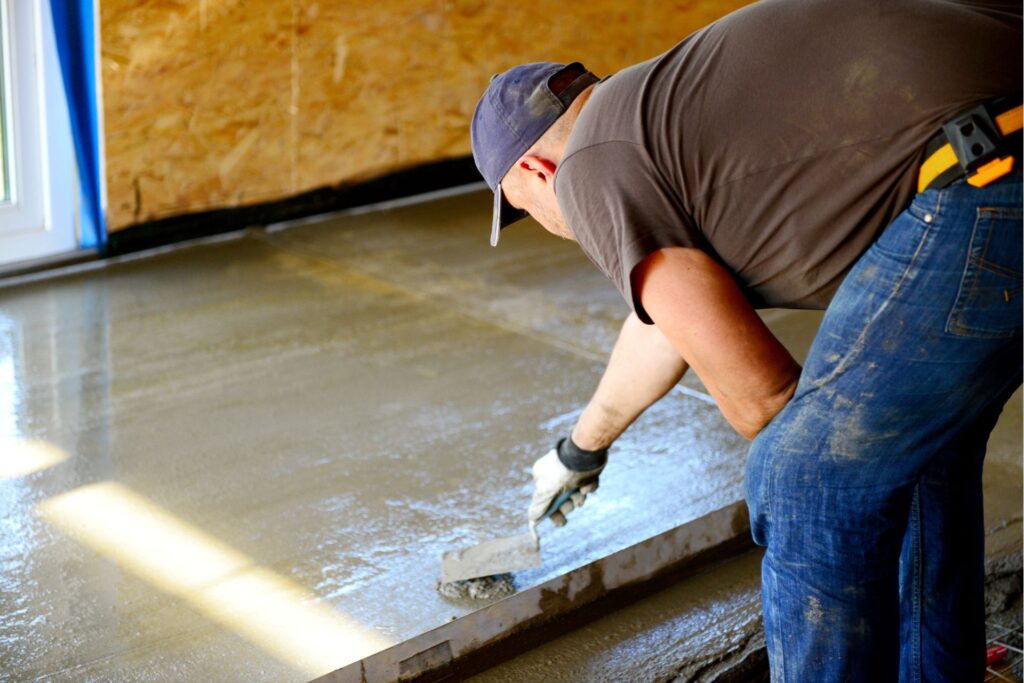
Tips To Save Money On Your Concrete Project
When you’re embarking on a concrete project, whether it’s for a driveway, patio, or a more complex construction, cost is always a major factor. Fortunately, there are several strategies you can use to keep expenses in check without sacrificing quality. Here are five valuable tips to save money on your concrete project.
Plan and Budget Early
One of the most effective ways to control costs is by planning and budgeting early. Having a clear plan for your project allows you to identify what materials and labor you’ll need, and gives you time to shop around for the best prices. Don’t just settle for the first supplier or contractor you find—get multiple quotes from different companies. This helps you compare costs and find the best value for your budget. Additionally, by planning ahead, you can schedule your project at a time when demand for contractors may be lower, which could result in lower pricing.
DIY vs. Hiring a Pro
Deciding whether to handle the project yourself or hire a professional is another key decision that impacts your budget. If you’re dealing with a small project or have some experience with concrete work, doing it yourself could save you a significant amount of money on labor. However, it’s essential to know your limits. Concrete work requires skill and precision; mistakes can lead to costly repairs. For larger or more complex projects, it’s often worth the investment to hire a pro. They have the expertise to ensure the job is done right the first time, which can save you money in the long run by preventing mistakes that could be expensive to fix.
Bulk Purchasing
Another smart way to cut costs is by purchasing materials in bulk. If you’re working on multiple projects or can batch several tasks together, buying concrete and other supplies in larger quantities can reduce your overall material costs. Suppliers often offer discounts for bulk purchases, and this can lead to significant savings, especially on larger projects. Additionally, buying in bulk can help you avoid frequent trips to the supplier, which can save time and transportation costs.
Using Local Suppliers
Sourcing materials from local suppliers can have a dual benefit: supporting your community and potentially saving you money. Local suppliers often have lower transportation costs, which can be a huge advantage when dealing with heavy materials like concrete. Additionally, they may be more flexible and responsive, which could result in better service and faster delivery times. By reducing the distance your materials need to travel, you can also help lower your project’s carbon footprint, making it an eco-friendly choice as well.
Proper Maintenance
Once your concrete project is complete, it’s important to maintain it properly to avoid costly repairs or replacements in the future. Regular cleaning, sealing, and addressing minor cracks or issues early can significantly extend the life of your concrete. A well-maintained concrete surface can last for decades, while neglected concrete may deteriorate much faster, leading to expensive fixes. By taking proactive steps to care for your concrete, you’ll save money in the long term by avoiding the need for premature replacements or major repairs.
By following these tips, you can effectively manage and reduce costs on your concrete project without compromising on quality. Early planning, making informed decisions about DIY vs. professional help, purchasing materials in bulk, sourcing locally, and practicing good maintenance habits are all smart ways to save money. Whether your project is large or small, these strategies will help you stay within your budget and ensure a successful outcome.
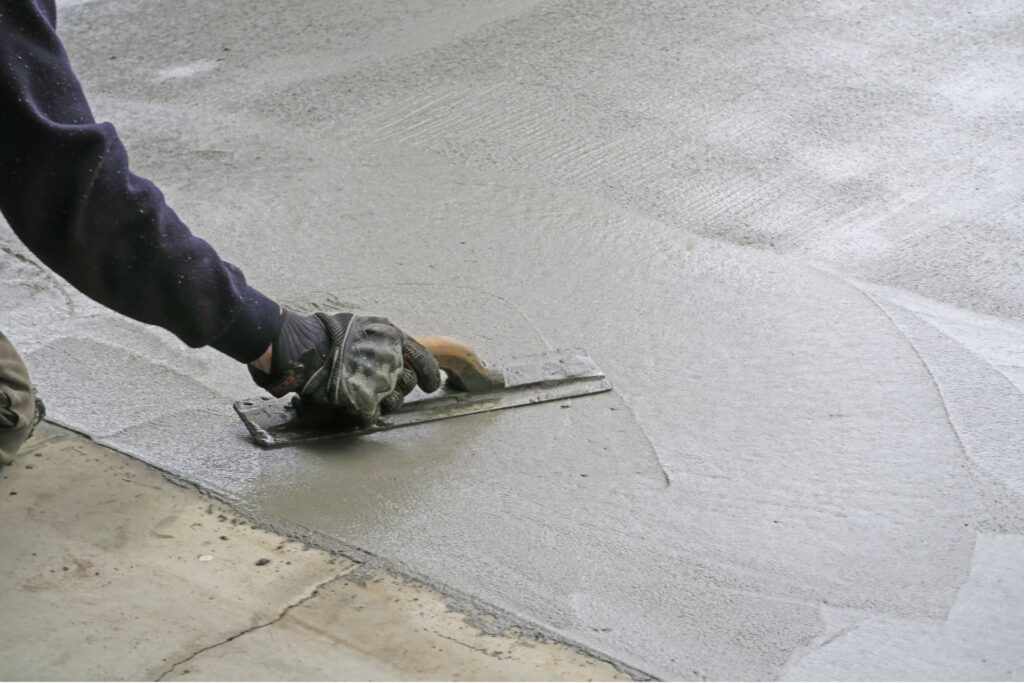
What To Expect When Hiring A Contractor
When embarking on any home improvement or construction project, hiring the right contractor is crucial to ensuring the success of the job. Whether you’re planning to build, renovate, or install new concrete, working with a reliable contractor can save you time, money, and stress. Here’s what you should expect when hiring a contractor, and some helpful tips to make sure you choose the right one for your needs.
Choosing the Right Contractor
Selecting the best contractor for your project is the first and most important step. Unfortunately, not all contractors are created equal, so it’s essential to vet potential hires thoroughly. Start by researching local contractors with experience in the specific work you need to be done. Look for online reviews, ask for recommendations from friends or neighbors, and check out past projects. Many contractors showcase their previous work through photos or even site visits, which can help you get a sense of their craftsmanship and reliability.
Certifications are another vital factor. Reputable contractors often carry certifications or belong to trade organizations, which means they adhere to industry standards and best practices. Additionally, make sure the contractor is properly licensed in your state or region, which ensures they meet local regulations and have the expertise to handle the job. Failure to check these credentials could lead to poor-quality work or even legal troubles down the road.
Getting a Quote
Once you’ve narrowed down your list of potential contractors, the next step is to request quotes. A quote is more than just a price tag; it’s a detailed breakdown of the work to be done, the materials that will be used, and the estimated timeframe for completion.
When reviewing a contractor’s quote, pay close attention to the specific materials they plan to use. For example, if you’re hiring someone to pour a concrete driveway, make sure the quote specifies the type of concrete mix, reinforcement options, and finishing details. Cheaper isn’t always better—low-cost materials can lead to poor results or even future repairs, costing you more in the long run.
Labor costs should also be clearly outlined. This includes not only the wages of the workers but also any subcontractors or specialists the contractor might hire. Make sure the timeframe for the project is realistic, and ask the contractor to outline any possible delays or issues that could arise. It’s also wise to ask about hidden costs, such as permits, waste removal, or additional materials, which might not be included in the initial quote. By thoroughly understanding the quote, you’ll avoid unpleasant surprises later.
Questions to Ask Your Contractor
Before committing to a contractor, it’s important to ask the right questions. These questions will help you gauge their reliability, professionalism, and ability to deliver what you expect. Here are a few key questions you should ask before signing any agreements:
1. Are You Licensed and Insured? – Make sure the contractor has the appropriate licensing to legally operate in your area. Insurance is equally important, as it protects you from liability in case of accidents or damages during the project.
2. Do You Provide Warranties for Your Work? – Warranties can give you peace of mind by ensuring that if something goes wrong after the job is completed, the contractor will fix it without additional costs. Ask about both material and workmanship warranties.
3. What’s the Estimated Timeline for the Project? – Have a clear understanding of the start and end dates. Unexpected delays can happen, but knowing the projected timeline will help you manage expectations and coordinate with other aspects of your project.
4. Can You Provide References? – A reputable contractor should be more than willing to provide references from previous clients. Speaking to someone who has worked with the contractor can give you valuable insight into their work ethic, reliability, and the overall quality of their job.
5. What Is the Payment Schedule? – Be wary of contractors who demand a large upfront payment. A typical payment schedule involves an initial deposit, followed by milestone payments throughout the project, and a final payment upon completion.
6. How Will You Handle Unexpected Issues? – Construction projects often encounter unforeseen problems, from weather delays to hidden structural issues. Ask your contractor how they typically manage these problems and whether they will notify you immediately if something arises.
Final Thoughts
Hiring a contractor is a big decision that can impact the success of your project. By carefully vetting potential contractors, thoroughly reviewing quotes, and asking the right questions, you’ll be better equipped to choose someone who will deliver high-quality work, on time, and within budget. Taking these steps can save you from headaches down the road and help ensure that your project is a success from start to finish.
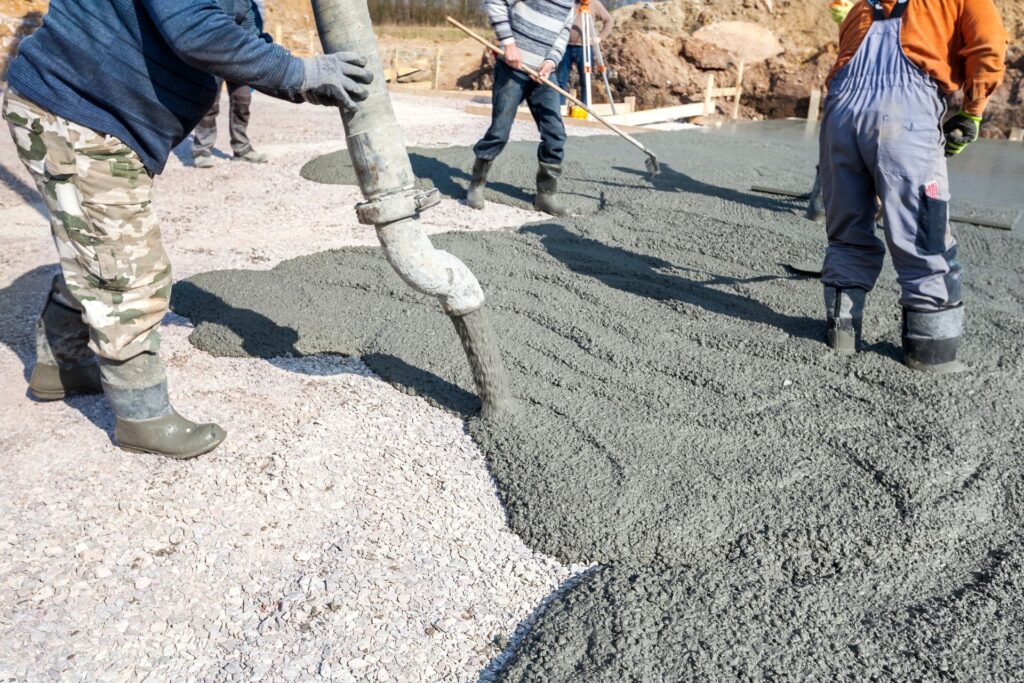
Environmental Impact And Sustainable Options For Concrete In NZ
Concrete is a foundational material in construction, but its environmental impact is increasingly under scrutiny, especially in a country as environmentally conscious as New Zealand. Understanding the carbon footprint associated with concrete production and exploring sustainable alternatives are essential steps toward greener building practices. Here’s a comprehensive look at these topics, along with actionable tips to make your concrete projects more eco-friendly.
The Carbon Footprint of Concrete
Concrete production is responsible for a significant portion of global CO2 emissions. The process of creating cement, the key binding component in concrete, involves heating limestone (calcium carbonate) to high temperatures, which releases carbon dioxide. In fact, cement production alone accounts for approximately 8% of global carbon emissions, making it a notable contributor to climate change. For New Zealand, which places a high emphasis on reducing its carbon footprint, addressing the environmental costs of concrete is a crucial issue.
One of the primary concerns is the sheer volume of concrete used in construction. From roads to buildings and infrastructure projects, concrete is everywhere. This widespread use, combined with the high energy demand and carbon output from cement production, results in a substantial environmental impact. This has led to an increased focus on finding ways to mitigate these effects and make the use of concrete more sustainable.
Eco-Friendly Alternatives
As awareness of the environmental impact of concrete grows, so does the development of eco-friendly alternatives. In New Zealand, several sustainable concrete options are gaining traction.
- Recycled Aggregate Concrete: This type of concrete uses recycled materials, such as crushed concrete from demolished buildings, as part of the aggregate mix. By reusing existing materials, recycled aggregate concrete reduces the demand for virgin resources and helps divert waste from landfills.
- Low-Carbon Concrete: Another promising option is low-carbon concrete, which reduces the amount of cement required. This can be achieved by incorporating supplementary cementitious materials like fly ash, slag, or silica fume, which are industrial by-products that would otherwise go to waste. These materials can partially replace cement in the concrete mix, thus lowering the overall carbon footprint.
- Geopolymer Concrete: A newer, more innovative option, geopolymer concrete, uses industrial by-products and waste materials, such as fly ash or slag, as the primary binder instead of traditional cement. This can result in up to 80% lower CO2 emissions compared to regular Portland cement concrete.
These alternatives not only reduce the environmental impact but also contribute to the development of a circular economy by reusing waste materials that would otherwise be discarded.
Sustainable Practices
Beyond choosing eco-friendly materials, there are several sustainable practices that can help reduce waste and lessen the environmental impact of concrete projects in New Zealand.
1. Optimize Mix Design: Careful mix design can significantly reduce the amount of cement needed in concrete, without compromising strength or durability. For example, using higher-quality aggregates or adjusting the water-cement ratio can result in a more efficient mix, leading to less material waste and lower emissions.
2. Use Local Materials: Sourcing materials locally can reduce the carbon emissions associated with transportation. This not only supports local economies but also reduces the environmental costs of moving heavy materials over long distances.
3. Minimize Over-Ordering: Construction projects often overestimate the amount of concrete needed, leading to waste. Precise calculations and careful planning can help minimize excess material, reducing waste and saving money in the process.
4. Recycle and Reuse Waste: Concrete waste from demolition or construction offcuts can be crushed and reused as aggregate in new projects. This reduces the demand for new raw materials and helps divert waste from landfills, promoting a more sustainable approach to construction.
5. Implement Energy-Efficient Techniques: Using energy-efficient curing methods, such as steam curing or using curing compounds, can help reduce the energy consumption associated with the curing process. Additionally, some methods may allow for quicker construction times, further minimizing the overall environmental impact.
As New Zealand continues to prioritize sustainability, it’s essential to consider the environmental impact of concrete in construction. By understanding the carbon footprint associated with traditional concrete, exploring eco-friendly alternatives, and adopting sustainable practices, we can work towards reducing the environmental impact of concrete projects across the country.
Incorporating recycled aggregate concrete, low-carbon options, or even exploring innovative materials like geopolymer concrete can make a significant difference. Meanwhile, reducing waste through optimized planning, reusing materials, and improving energy efficiency are practical steps that can be implemented in any project.
The future of construction in New Zealand lies in balancing the need for durable, long-lasting materials with the pressing demand for environmental responsibility. Through thoughtful material selection and sustainable practices, concrete can be part of the solution rather than the problem.
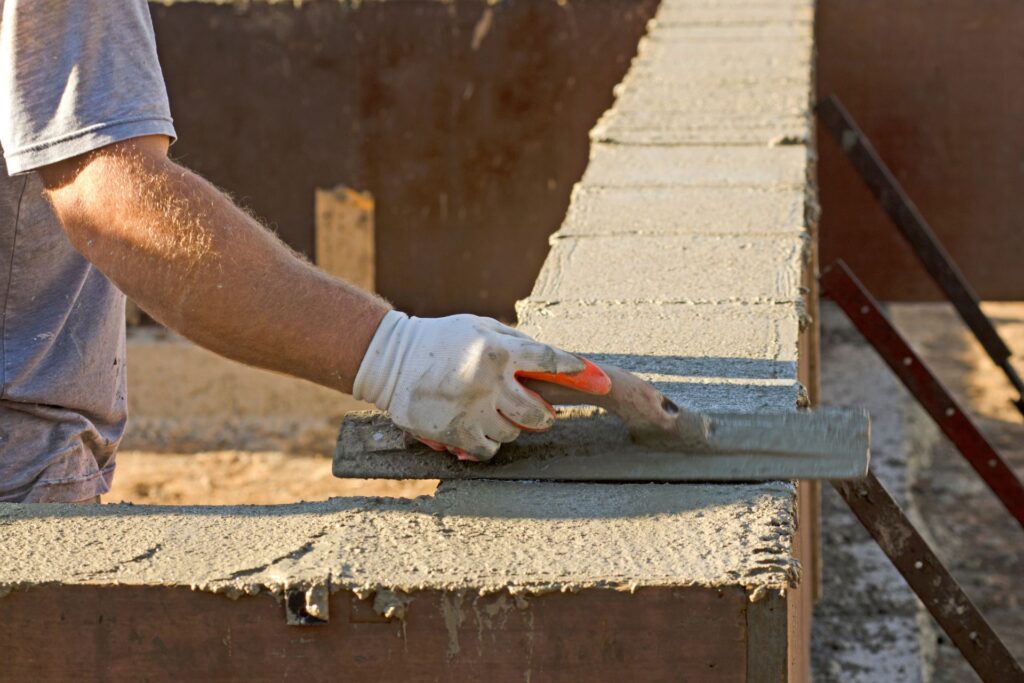
FAQs: About Cost Of Concrete NZ
Conclusion
In conclusion, when considering a project, it’s essential to understand the key factors that influence pricing, such as the average costs in your area, the scope of the work, and the specific materials or services required. By keeping these elements in mind, you can ensure you’re getting the best value for your investment. For more personalized and accurate estimates, it’s a good idea to reach out to local suppliers or contractors who can provide quotes tailored to your needs. We’d love to hear from you—whether you have further questions or want to share your own experiences, feel free to join the conversation in the comments below!
Find A Professional Concrete Company Near You!
- Asphalt Contractors Auckland
- Christchurch Concrete Services
- Concrete Contractors Nelson
- Concrete Contractors Tauranga
- Concrete Dannevirke
- Concrete Driveways Lower Hutt
- Concrete Driveways Upper Hutt
- Concrete Foundations Kapiti
- Concrete Layers Auckland
- Concrete Layers Cambridge
- Concrete Layers Hamilton
- Concrete Layers Invercargill
- Concrete Layers Kapiti
- Concrete Layers Leigh
- Concrete Layers Levin
- Concrete Layers Mangawhai
- Concrete Layers Matakana
- Concrete Layers Northland
- Concrete Layers Orewa
- Concrete Layers Palmerston North
- Concrete Layers Pukekohe
- Concrete Layers Rodney
- Concrete Layers Silverdale
- Concrete Layers Te Awamutu
- Concrete Layers Upper Hutt
- Concrete Layers Waikato
- Concrete Layers Warkworth
- Concrete Layers Wellington
- Concrete Layers Wellsford
- Concrete Manuwatu
- Concrete Services Rotorua
- Concrete Whangarei
- Hastings Concrete Company
- Hawkes Bay Concrete Company
- Napier Concrete Company
About the Author:
Mike Veail is a recognized digital marketing expert with over 6 years of experience in helping tradespeople and small businesses thrive online. A former quantity surveyor, Mike combines deep industry knowledge with hands-on expertise in SEO and Google Ads. His marketing strategies are tailored to the specific needs of the trades sector, helping businesses increase visibility and generate more leads through proven, ethical methods.
Mike has successfully partnered with numerous companies, establishing a track record of delivering measurable results. His work has been featured across various platforms that showcase his expertise in lead generation and online marketing for the trades sector.
Learn more about Mike's experience and services at https://theleadguy.online or follow him on social media: