Welcome to your ultimate guide on understanding the cost of concrete per cubic meter (m3) in New Zealand. Whether you’re planning a small DIY project at home or managing a large-scale construction, getting a clear picture of concrete costs is essential for staying on budget and avoiding surprises. In this article, we’ll break down everything you need to know about the factors that influence concrete prices in NZ, current market rates, and tips on how to get the best value for your money. By the end, you’ll be equipped with the knowledge to make informed decisions and ensure your project runs smoothly.
On average, the cost of concrete per cubic meter (m3) in New Zealand ranges from NZD $150 to $250, depending on factors such as the type of concrete, quantity ordered, and delivery location.
- What Is Concrete And Why It Matters
- Factors Influencing Concrete Cost Per M3 In NZ
- Average Concrete Cost Per M3 In NZ
- Hidden Costs To Consider
- How To Get The Best Value For Your Money
- Sustainable Options And Their Costs
- FAQs: About Concrete Cost Per M3 NZ
- Conclusion
- Find A Professional Concrete Company Near You!
What Is Concrete And Why It Matters
Concrete is one of the most fundamental building materials in the construction industry, forming the backbone of structures that are designed to last. Understanding what concrete is and why it matters is crucial for anyone involved in construction, whether you’re a seasoned professional or a homeowner planning a new project.
What is Concrete?
Concrete is a composite material that plays a vital role in modern construction. At its core, concrete is a mixture of three essential components: cement, water, and aggregates. The cement, usually made from a combination of limestone and clay, acts as the binding agent. When mixed with water, it undergoes a chemical reaction known as hydration, which hardens the mixture. The aggregates, typically a blend of sand, gravel, or crushed stone, provide the bulk and structural integrity of the concrete.
This simple yet effective combination results in a versatile material that can be molded into virtually any shape, making it indispensable for construction. Its ability to withstand immense pressures and its durability in varying environmental conditions have made concrete a cornerstone of the building industry for centuries.
Common Uses of Concrete
Concrete’s versatility is evident in its widespread applications across various sectors of the construction industry. It’s the go-to material for laying foundations, where its strength provides a solid base for buildings. Driveways are another common use, as concrete’s durability allows it to withstand heavy vehicles and resist weathering over time. Floors, both residential and commercial, often use concrete due to its capacity to support significant weight and endure constant foot traffic.
Walls, too, benefit from concrete’s robustness, especially in New Zealand, where the material is favored for its ability to endure the country’s diverse climate conditions. Whether it’s for a high-rise in Auckland or a home in a more rural area, concrete is a preferred material because it offers long-term durability and requires minimal maintenance.
In New Zealand’s construction industry, concrete is particularly valued not just for its strength, but for its resilience in the face of natural disasters. With the country’s susceptibility to earthquakes, the material’s inherent flexibility and robustness make it an ideal choice for building structures that can withstand seismic activity.
Concrete matters because it provides the foundation—both literally and figuratively—of modern infrastructure. Its importance cannot be overstated, as it ensures that the structures we build are safe, durable, and sustainable.
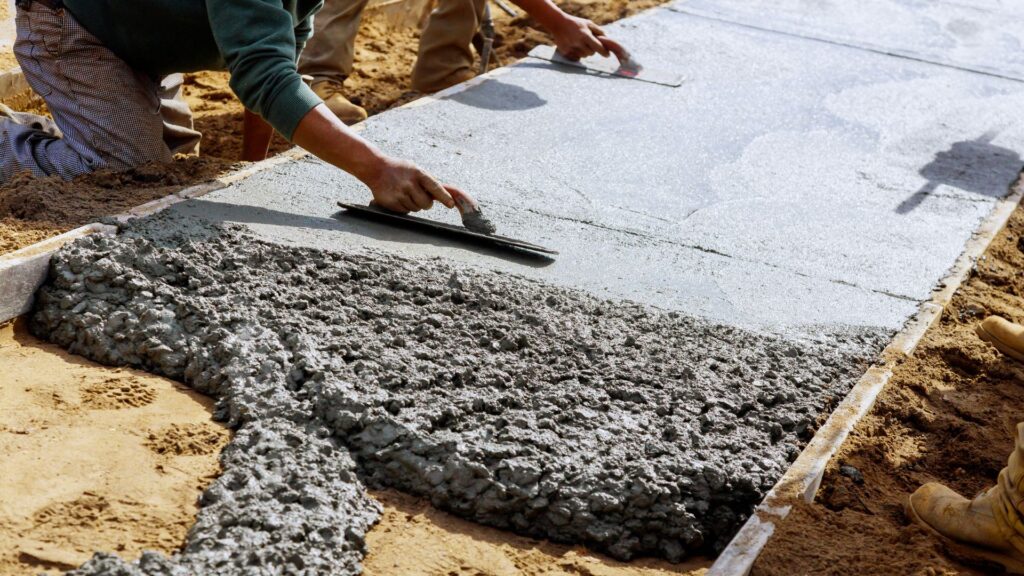
Factors Influencing Concrete Cost Per M3 In NZ
Understanding the factors that influence the cost of concrete per cubic meter (m3) in New Zealand is crucial for anyone involved in construction or renovation projects. The price of concrete can vary significantly based on a variety of factors, each of which plays a key role in determining the final cost. Here’s an in-depth look at these factors:
Type of Concrete
The type of concrete you choose is one of the most significant determinants of cost. In New Zealand, several types of concrete are commonly used, each with its own price point:
- Standard Concrete: This is the most commonly used type of concrete for general construction purposes. It is typically the most affordable option, ideal for foundations, driveways, and basic structural work.
- High-Strength Concrete: Designed to bear heavier loads, high-strength concrete is more expensive than standard concrete. It’s used in projects that require added durability and load-bearing capacity, such as commercial buildings and industrial structures.
- Decorative Concrete: This type of concrete is aesthetically designed, often used for driveways, patios, and interior flooring. Due to the additional materials and techniques required, decorative concrete is usually the most expensive option.
The type of concrete you select will significantly impact the overall cost per cubic meter, so it’s essential to choose the one that meets your specific needs without unnecessarily inflating your budget.
Quantity Ordered
The quantity of concrete you order also has a direct impact on the price per cubic meter. In general, the larger the order, the lower the cost per unit. This is due to the concept of bulk pricing, where suppliers offer discounts for larger purchases:
- Small Orders: Ordering just a few cubic meters may incur higher costs per m3, as suppliers often charge a premium for smaller loads.
- Bulk Orders: When you order in larger quantities, the cost per cubic meter typically decreases. This is particularly advantageous for larger projects, where the savings can add up significantly.
Planning your project to maximize the volume of concrete ordered in one go can help reduce overall expenses.
Delivery Location
Where the concrete is being delivered can significantly affect the final cost. The location of your project—whether it’s in an urban or rural area—will influence delivery charges:
- Urban Areas: Delivery costs in urban areas are generally lower due to better infrastructure, shorter distances, and higher competition among suppliers.
- Rural Areas: In contrast, rural locations often incur higher delivery fees. The increased distance from the supplier’s plant, along with potential accessibility issues, can drive up costs.
It’s important to consider the logistics of your location when budgeting for concrete, as these delivery charges can add up quickly.
Site Preparation
The condition and readiness of your site also play a critical role in the overall cost of concrete:
- Leveling: If your site needs extensive leveling or grading before the concrete can be poured, this can increase your costs. A well-prepared site requires less time and effort, thereby reducing the overall expense.
- Accessibility: Sites that are difficult to access—due to narrow roads, steep inclines, or other obstacles—may also incur higher costs. Extra labor or specialized equipment may be required to transport the concrete to the site, adding to the final bill.
Ensuring your site is adequately prepared and easily accessible can help keep costs down.
Additives and Special Mixes
The use of additives and special mixes in your concrete can also affect the price:
- Additives: Common additives like accelerants (which speed up curing time) or retarders (which slow down the curing process) can increase the cost per cubic meter. These are often used to meet specific project timelines or environmental conditions.
- Special Mixes: Custom concrete mixes, designed for specific applications or performance characteristics, are generally more expensive than standard mixes. This might include concrete with enhanced durability, reduced shrinkage, or specific aesthetic qualities.
While these options can provide the necessary performance or appearance for your project, they also come at an added cost.
Time of Year
Finally, the time of year when you order concrete can influence its cost. Seasonal variations can lead to price fluctuations:
- Peak Construction Seasons: During the warmer months, when construction activity is at its peak, demand for concrete is higher. This often leads to increased prices due to the higher demand and limited supply.
- Off-Peak Seasons: In contrast, during the cooler months, demand typically drops, which can lead to lower prices. Suppliers may offer discounts or promotional pricing during these periods to stimulate demand.
Timing your project to align with off-peak seasons can be a strategic way to minimize costs.
In summary, the cost of concrete per cubic meter in New Zealand is influenced by a variety of factors, including the type of concrete, the quantity ordered, delivery location, site preparation, additives, and the time of year. By understanding these factors and planning accordingly, you can optimize your budget and ensure that you get the best value for your project.
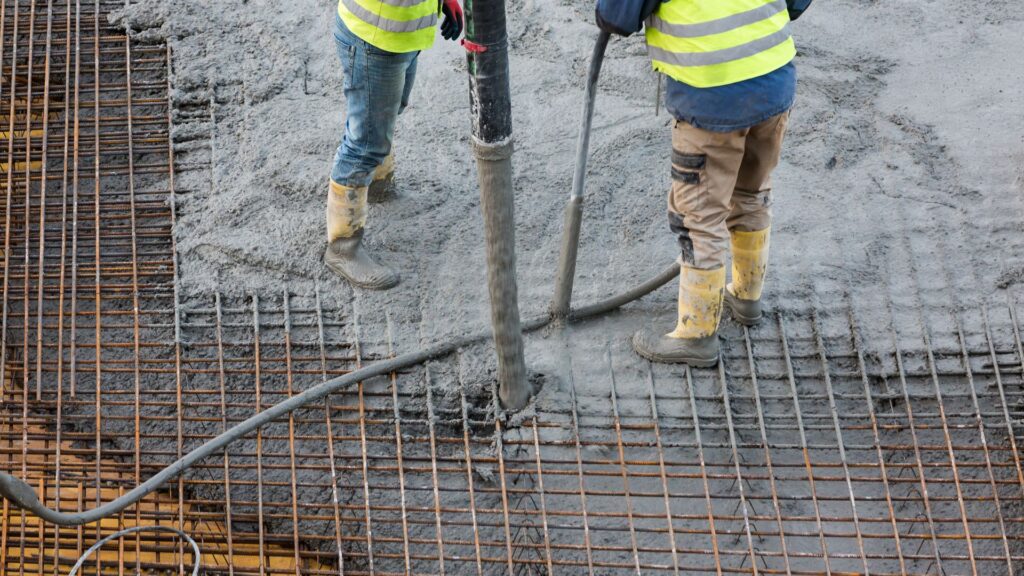
Average Concrete Cost Per M3 In NZ
When planning a construction project in New Zealand, one of the critical factors to consider is the cost of concrete. Whether you’re building a small home extension or a large commercial structure, understanding the current market rates for concrete is essential for budgeting. In this section, we’ll explore the average concrete cost per cubic meter (m3) in New Zealand, taking a closer look at regional differences, price comparisons with other countries, and real-world case studies to provide a comprehensive overview.
Current Market Rates
The cost of concrete in New Zealand varies depending on several factors, including the region, type of concrete, and current market demand. On average, the price per cubic meter of concrete across New Zealand ranges from NZD $150 to $250. However, this range can fluctuate based on the specific mix required and the location of the project.
- Auckland: In Auckland, the price tends to be on the higher end, typically between NZD $180 and $250 per m3. The city’s higher prices are driven by increased demand, urban density, and transportation costs.
- Wellington: Wellington offers slightly lower rates, with prices generally ranging from NZD $170 to $240 per m3. The cost here is influenced by the city’s topography and the logistical challenges of transporting materials.
- Christchurch: In Christchurch, prices are more competitive, usually falling between NZD $150 and $220 per m3. This region has seen more stable prices post-earthquake reconstruction, with steady demand contributing to these rates.
It’s important to note that these prices can vary further based on the type of concrete used. For instance, specialty concretes like high-strength or decorative options can command higher prices, often reaching upwards of NZD $300 per m3.
Price Comparisons
To better understand the concrete costs in New Zealand, it’s helpful to compare them with those in other countries like Australia and the UK.
- Australia: In Australia, the average cost of concrete ranges from AUD $200 to $300 per m3 (approximately NZD $210 to $320 per m3). While similar to New Zealand, the slightly higher prices are influenced by larger urban centers and differing market dynamics.
- United Kingdom: In the UK, the average cost of concrete is about GBP £65 to £85 per m3 (around NZD $130 to $170 per m3). The UK’s lower prices can be attributed to more mature supply chains and greater market competition.
This comparison highlights that while New Zealand’s concrete prices are competitive, they are slightly higher than in the UK but generally lower than in Australia. This information is crucial for contractors and project planners who may be working on international projects or comparing costs across borders.
Case Studies
To illustrate the impact of concrete costs on real-world projects, let’s consider a few case studies:
- Residential Driveway in Auckland: A homeowner in Auckland decided to upgrade their driveway using exposed aggregate concrete. The project required 15 m3 of concrete, with the total cost coming to NZD $3,750. Although the material cost was slightly above the standard mix due to the decorative finish, the homeowner was pleased with the aesthetic result and found the investment worthwhile.
- Commercial Building in Wellington: A medium-sized commercial development in Wellington utilized 200 m3 of high-strength concrete for its foundation. The cost for the concrete alone was NZD $46,000. This choice of material increased the project’s upfront costs but provided long-term savings due to the reduced need for maintenance and repairs.
- Post-Earthquake Reconstruction in Christchurch: In the wake of the Christchurch earthquakes, a significant rebuild project required the use of 500 m3 of standard concrete. The total cost was approximately NZD $100,000, which was within the budget, thanks to competitive pricing in the region. This project highlighted the importance of balancing cost with quality, particularly in seismic zones.
These case studies underscore how the type and volume of concrete used can significantly impact the overall budget of a project. By considering both the immediate costs and long-term benefits, contractors and property owners can make informed decisions that align with their financial goals.
Understanding the average concrete cost per cubic meter in New Zealand is vital for anyone involved in construction. With regional variations, price comparisons, and real-world examples in mind, you can better anticipate costs and plan accordingly. Whether you’re working on a small residential project or a large-scale commercial development, being informed about concrete prices will help you stay within budget and achieve the best possible outcome for your build.
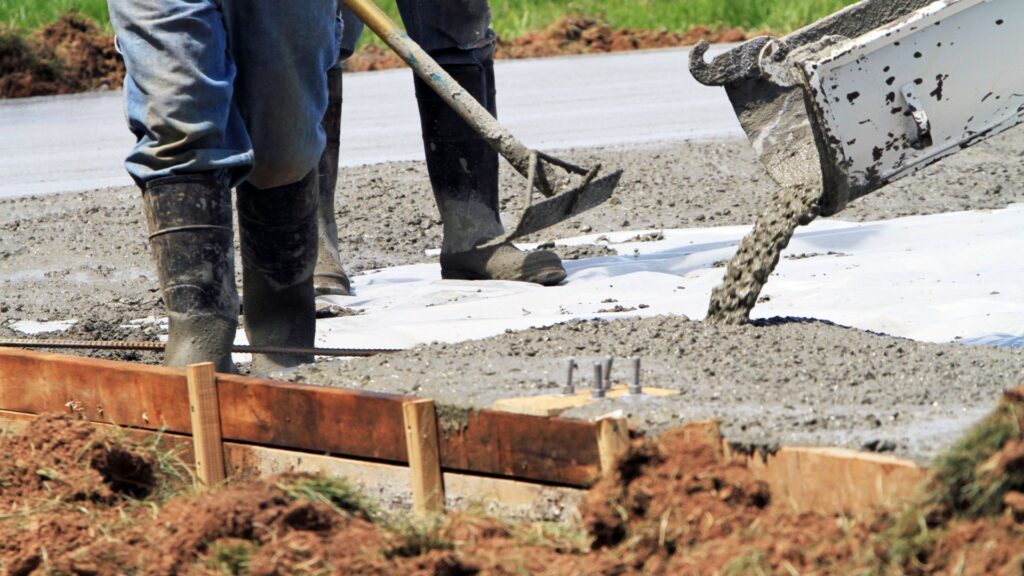
Hidden Costs To Consider
When planning your concrete project, it’s easy to focus solely on the cost of materials. However, several hidden costs can significantly impact your budget if not properly accounted for. Below, we’ll break down some of the most common additional expenses you might encounter.
Delivery Fees
One of the first hidden costs to consider is delivery fees. The cost of getting the concrete to your site can vary greatly depending on several factors. The distance from the supplier to your location is a primary determinant—longer distances naturally incur higher charges. Additionally, if your site is in a remote area or difficult to access, this can further increase delivery costs. For instance, narrow roads, steep inclines, or areas that require special permits might result in extra fees. It’s essential to discuss these details with your supplier upfront to avoid surprises on your final bill.
Pump Hire
In some cases, getting the concrete exactly where you need it requires more than just a simple delivery. If your site has challenging access points, such as being on a higher floor or a location far from where the truck can park, you may need to hire a concrete pump. Pump hire is another cost that can add up quickly, especially for larger projects or sites with complex layouts. This equipment is crucial for ensuring that the concrete is placed efficiently and accurately, but it’s an expense that needs to be factored into your budget from the beginning.
Wastage and Over-Ordering
Concrete is not a material you want to run out of mid-project, which often leads to over-ordering as a precaution. However, this can result in additional costs if you’re left with excess material that goes to waste. Wastage is a common issue in concrete projects, where even a small percentage of over-ordered material can lead to unnecessary expenses. To minimize this, work closely with your supplier to calculate the exact amount you need, and have a clear plan for handling any excess. Proper planning and precise ordering can help you avoid the financial impact of wastage.
Labor Costs
While the focus of many concrete projects is on the material itself, the labor involved in pouring and finishing the concrete is another crucial cost to consider. Skilled labor is required to ensure that the concrete is poured correctly and achieves the desired finish. These costs can vary depending on the complexity of the job, the experience level of the workers, and the local labor market. Ignoring labor costs in your budget can lead to a significant underestimation of your total project expenses. Therefore, it’s important to account for the full scope of labor required to complete your concrete project.
When budgeting for a concrete project, it’s crucial to consider these hidden costs to avoid unexpected financial strain. Delivery fees, pump hire, wastage, and labor costs can all add up, turning a seemingly simple project into a more expensive endeavor. By planning ahead and discussing these potential costs with your supplier and contractors, you can ensure a more accurate budget and a smoother project overall.
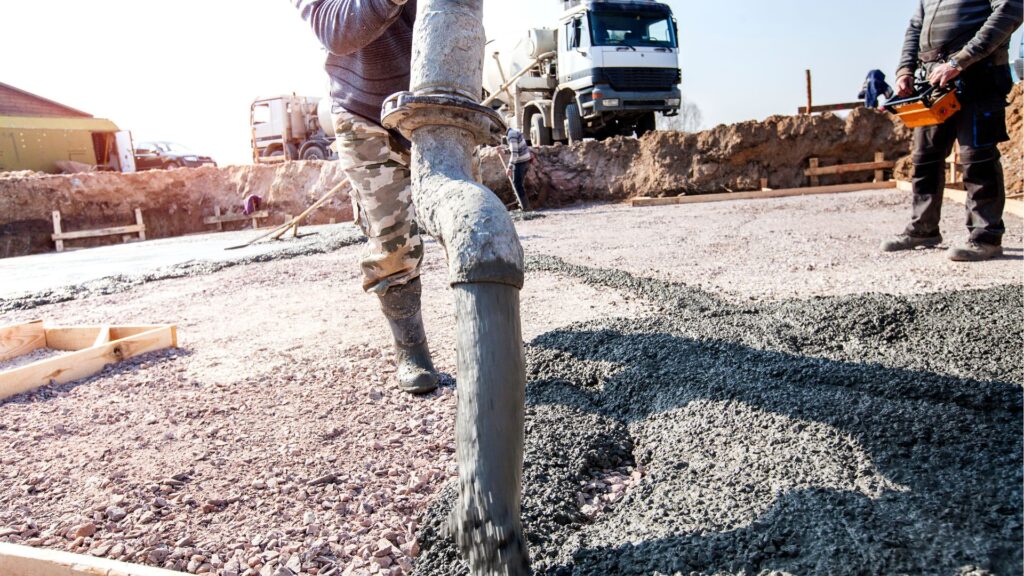
How To Get The Best Value For Your Money
When it comes to managing a concrete project, every penny counts. Whether you’re working on a large-scale construction site or a smaller home improvement project, maximizing the value of your investment is crucial. Here’s how you can ensure you’re getting the most for your money.
Sourcing Multiple Quotes
One of the most effective ways to ensure you’re getting a fair price is by sourcing multiple quotes from different suppliers. Don’t just settle for the first offer you receive. Reach out to at least three to five suppliers to get a sense of the market rate. By doing this, you’ll have the leverage to negotiate better prices, and you can also gauge the reliability and service quality of each supplier. Remember, the cheapest option isn’t always the best—consider factors like delivery times, payment terms, and the supplier’s reputation.
Bulk Ordering
If your project allows for it, consider ordering your concrete in bulk. Suppliers often provide discounts for large orders, which can significantly reduce your overall costs. Bulk ordering is especially beneficial for larger projects where you know the exact quantity of concrete needed. However, even for smaller projects, teaming up with nearby projects to place a joint order could unlock bulk rates that you wouldn’t access otherwise. Make sure your supplier has the capacity to deliver and handle bulk orders efficiently.
Efficient Planning
Time is money, especially in construction. Delays can lead to additional costs, from labor to extended equipment rentals. Therefore, meticulous planning is essential. Ensure that your project timeline is realistic and that all resources, including concrete, are scheduled to arrive when needed. Avoid over-ordering or under-ordering by accurately calculating your concrete needs ahead of time. Moreover, having a backup plan in case of unforeseen issues, like weather delays, can save you from unexpected costs.
Negotiation Tips
Negotiation isn’t just about asking for a lower price—it’s about finding a mutually beneficial arrangement. When discussing terms with your supplier, highlight your commitment to future projects or referrals if they offer you a good deal. Be transparent about your budget constraints, and ask if there are any ongoing promotions or discounts for which you could be eligible. Also, consider negotiating for added value, such as quicker delivery times or better payment terms, rather than focusing solely on the price.
Use of Ready-Mix Concrete
Ready-mix concrete can be a game-changer for many projects. Although it might seem more expensive upfront, its advantages can lead to cost savings in the long run. Ready-mix concrete is prepared under controlled conditions, ensuring consistency and reducing the chances of error. This type of concrete also cuts down on labor costs and saves time since it’s delivered ready to pour. For projects where precision and efficiency are crucial, the investment in ready-mix concrete can be well worth it. Additionally, by eliminating the need for on-site mixing, you reduce waste and cleanup costs, adding even more value to your project.
By following these strategies, you can make informed decisions that not only keep your project within budget but also ensure you’re getting the best possible value for your money. From careful planning and smart negotiation to the strategic use of materials like ready-mix concrete, every step counts toward maximizing your investment.
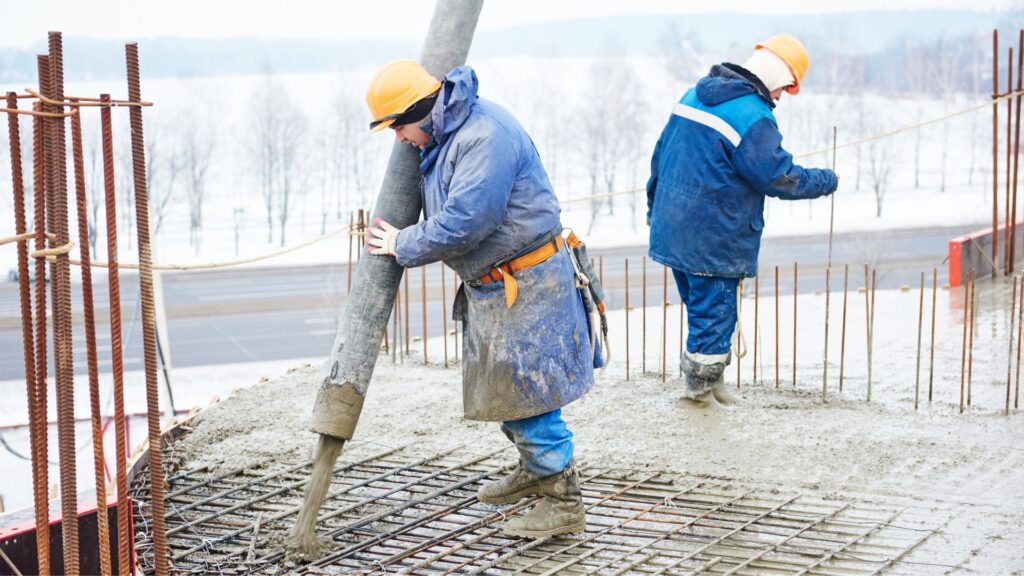
Sustainable Options And Their Costs
When considering construction materials in New Zealand, the environmental impact of concrete is a growing concern. Traditional concrete production is known for its significant carbon footprint, but the good news is that sustainable alternatives are becoming more accessible. This section delves into eco-friendly concrete options, compares their costs to standard concrete, and explores the potential long-term savings these alternatives can offer.
Eco-Friendly Concrete Alternatives
In New Zealand, the construction industry is increasingly adopting sustainable practices, and one of the most promising developments is the use of eco-friendly concrete alternatives. A popular option is recycled aggregate concrete. This type of concrete replaces natural aggregates with recycled materials, such as crushed concrete from demolition sites or recycled industrial by-products like slag. Not only does this reduce the need for virgin materials, but it also diverts waste from landfills, making it a more sustainable choice.
Another innovative solution is geopolymer concrete, which uses industrial waste materials such as fly ash or slag as a binder instead of traditional Portland cement. This results in significantly lower carbon emissions during production. These alternatives are particularly relevant in New Zealand, where the construction industry is increasingly focused on reducing its environmental impact without compromising on the quality and durability of materials.
Cost Comparison
When it comes to costs, eco-friendly concrete alternatives can vary. Recycled aggregate concrete, for example, is often competitively priced compared to standard concrete, especially when the cost savings from reduced material transport and waste disposal are factored in. However, the price of geopolymer concrete can be higher due to the specialized production processes involved. Despite this, the gap in costs is closing as demand increases and production techniques improve.
It’s important to consider that while the upfront costs of sustainable concrete might be slightly higher in some cases, this is not always the case. Many contractors and builders in New Zealand find that these costs are offset by the benefits of using recycled or locally sourced materials, which can reduce transportation expenses and contribute to a project’s sustainability credentials, potentially qualifying for green building certifications.
Long-Term Savings
Investing in sustainable concrete alternatives can lead to significant savings over time, making them an attractive option for long-term projects. One of the key advantages is durability. Recycled aggregate concrete and geopolymer concrete are known for their enhanced durability and resistance to chemical attacks, which can reduce maintenance costs and extend the lifespan of structures.
Moreover, these sustainable options often contribute to improved energy efficiency. For instance, some eco-friendly concrete has better thermal properties, helping to regulate building temperatures and reduce the need for heating and cooling. Over the life of a building, these energy savings can be substantial, further justifying the initial investment in sustainable materials.
In summary, while the initial cost of eco-friendly concrete options in New Zealand might be comparable to or slightly higher than traditional concrete, the long-term benefits, including lower maintenance costs, enhanced durability, and energy savings, make them a wise investment for the future. As the construction industry continues to prioritize sustainability, these alternatives are likely to become even more cost-effective and widely adopted.
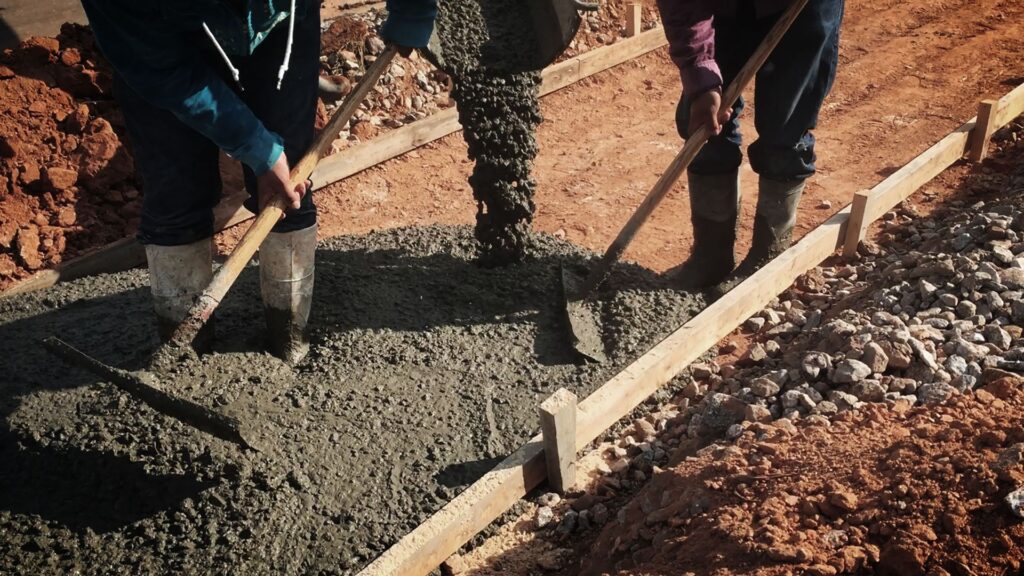
FAQs: About Concrete Cost Per M3 NZ
Conclusion
Understanding the costs of concrete is crucial for the success of any construction project in New Zealand. Knowing these costs allows for better budgeting, planning, and decision-making, ensuring that your project stays on track both financially and in terms of timing. If you have any experiences to share or questions about concrete costs, we’d love to hear from you—feel free to join the conversation in the comments below. And if you found this information helpful, consider sharing this post with others who might benefit from it as well.
Find A Professional Concrete Company Near You!
- Asphalt Contractors Auckland
- Christchurch Concrete Services
- Concrete Contractors Nelson
- Concrete Contractors Tauranga
- Concrete Dannevirke
- Concrete Driveways Lower Hutt
- Concrete Driveways Upper Hutt
- Concrete Foundations Kapiti
- Concrete Layers Auckland
- Concrete Layers Cambridge
- Concrete Layers Hamilton
- Concrete Layers Invercargill
- Concrete Layers Kapiti
- Concrete Layers Leigh
- Concrete Layers Levin
- Concrete Layers Mangawhai
- Concrete Layers Matakana
- Concrete Layers Northland
- Concrete Layers Orewa
- Concrete Layers Palmerston North
- Concrete Layers Pukekohe
- Concrete Layers Rodney
- Concrete Layers Silverdale
- Concrete Layers Te Awamutu
- Concrete Layers Upper Hutt
- Concrete Layers Waikato
- Concrete Layers Warkworth
- Concrete Layers Wellington
- Concrete Layers Wellsford
- Concrete Manuwatu
- Concrete Services Rotorua
- Concrete Whangarei
- Hastings Concrete Company
- Hawkes Bay Concrete Company
- Napier Concrete Company
About the Author:
Mike Veail is a recognized digital marketing expert with over 6 years of experience in helping tradespeople and small businesses thrive online. A former quantity surveyor, Mike combines deep industry knowledge with hands-on expertise in SEO and Google Ads. His marketing strategies are tailored to the specific needs of the trades sector, helping businesses increase visibility and generate more leads through proven, ethical methods.
Mike has successfully partnered with numerous companies, establishing a track record of delivering measurable results. His work has been featured across various platforms that showcase his expertise in lead generation and online marketing for the trades sector.
Learn more about Mike's experience and services at https://theleadguy.online or follow him on social media: