Concrete Cost Calculator NZ
Total Estimated Cost: NZD $0.00
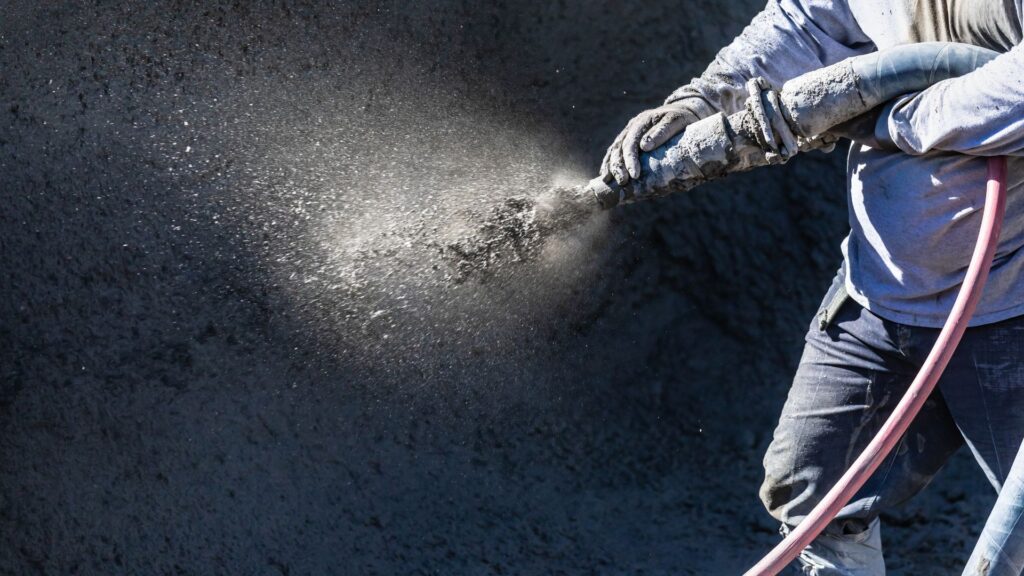
Welcome to our comprehensive guide on using a concrete cost calculator in New Zealand. Whether you’re planning a small DIY project or a large-scale construction job, accurately estimating the cost of concrete is crucial for staying on budget and avoiding unexpected expenses. In this post, we’ll walk you through everything you need to know about concrete pricing, the benefits of using a cost calculator, and the factors that can influence your total costs. By the end, you’ll have a clear understanding of how to plan your project more effectively, save money, and make informed decisions.
On average, the cost of concrete in New Zealand ranges from NZD $150 to $250 per cubic meter, depending on factors such as the type of concrete, location, and additional services required. Using a concrete cost calculator can help you accurately estimate your project’s total expenses based on these variables.
- Concrete Cost Calculator NZ
- General Overview of Concrete Pricing
- Types of Concrete and Their Costs
- Factors Influencing Concrete Costs
- What is a Concrete Cost Calculator
- Benefits of Using a Concrete Cost Calculator
- Material Costs
- Labor Costs
- Transportation and Delivery
- Site Preparation and Additional Costs
- Gathering the Necessary Information
- Inputting Data into the Calculator
- Interpreting the Results
- Tips for Adjusting the Results
- Buying in Bulk
- Opting for Local Suppliers
- Reusing Formwork and Materials
- Timing Your Purchase
- Seeking Professional Advice
- Underestimating Waste
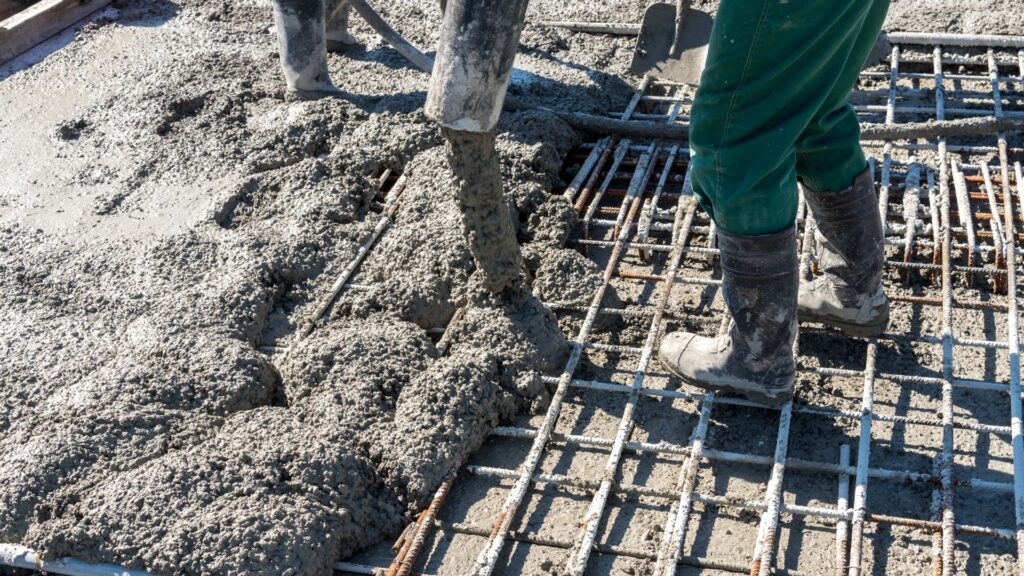
Understanding Concrete Costs In New Zealand
Concrete is a fundamental building material widely used in various construction projects across New Zealand. Whether you’re building a driveway, laying a foundation, or constructing a commercial structure, understanding the costs associated with concrete is crucial for budgeting and planning. In this article, we’ll break down the general pricing of concrete, factors affecting its cost, and the different types of concrete available in New Zealand, helping you make informed decisions for your next project.
General Overview of Concrete Pricing
The cost of concrete in New Zealand varies depending on several factors, but on average, you can expect to pay between NZD $100 and $150 per cubic meter. This range can fluctuate based on a variety of influences, including the location of your project. For example, concrete prices tend to be higher in urban areas compared to rural regions due to differences in demand, transportation costs, and the availability of suppliers.
In urban centers like Auckland and Wellington, the cost of living and business operations are generally higher, which contributes to increased concrete prices. On the other hand, in rural areas, although transportation might be more expensive due to distance, the overall lower cost of doing business can sometimes offset these expenses, making concrete slightly more affordable. Additionally, regional availability of raw materials can also affect pricing; areas closer to quarries or manufacturing plants may benefit from reduced costs.
Types of Concrete and Their Costs
Concrete is not a one-size-fits-all material; various types are available, each tailored to specific uses and projects. The most common types of concrete used in New Zealand include.
- Standard Mix Concrete: This is the most commonly used type of concrete for general construction purposes. It’s a versatile mix suitable for a wide range of projects, including driveways, patios, and general building foundations. The cost of standard mix concrete typically falls within the NZD $100 to $130 per cubic meter range, depending on the strength and the specific mix required.
- Reinforced Concrete: Reinforced concrete is embedded with steel bars or mesh, providing additional strength and durability, making it ideal for structural applications like beams, columns, and load-bearing walls. Due to the added materials and labor involved, reinforced concrete is more expensive, typically costing between NZD $140 and $170 per cubic meter.
- Decorative Concrete: As the name suggests, decorative concrete is used primarily for aesthetic purposes. This type can include various finishes, such as colored, stamped, or polished concrete. Decorative concrete is popular for outdoor spaces, walkways, and interior flooring. Given the specialized nature and additional processes involved, decorative concrete can be more expensive, ranging from NZD $150 to $200 per cubic meter or more, depending on the complexity of the design.
Each type of concrete serves a specific purpose, and choosing the right one depends on the requirements of your project. It’s essential to consider both the functional and aesthetic needs to select the appropriate type that aligns with your budget.
Factors Influencing Concrete Costs
Several factors contribute to the variation in concrete costs across New Zealand.
- Project Location: As mentioned earlier, whether your project is in an urban or rural area can significantly impact the price due to differences in transportation, demand, and supplier competition.
- Concrete Volume: Larger projects typically benefit from economies of scale, meaning the more concrete you order, the lower the price per cubic meter. Small projects, however, might face higher per-unit costs.
- Concrete Strength: Different projects require concrete with varying strengths, measured in megapascals (MPa). Higher-strength concrete mixes are more expensive due to the additional materials required to achieve the desired strength.
- Additives and Custom Mixes: Any special requirements, such as faster curing times, water resistance, or colored concrete, can increase the cost. Custom mixes tailored to specific project needs will generally be priced higher than standard mixes.
Understanding the costs associated with concrete in New Zealand is essential for planning any construction project. By considering the type of concrete, the location of your project, and the specific needs of your construction, you can better estimate the expenses and make informed decisions. Whether you opt for standard, reinforced, or decorative concrete, knowing what factors influence pricing will help you manage your budget effectively and ensure the success of your project.
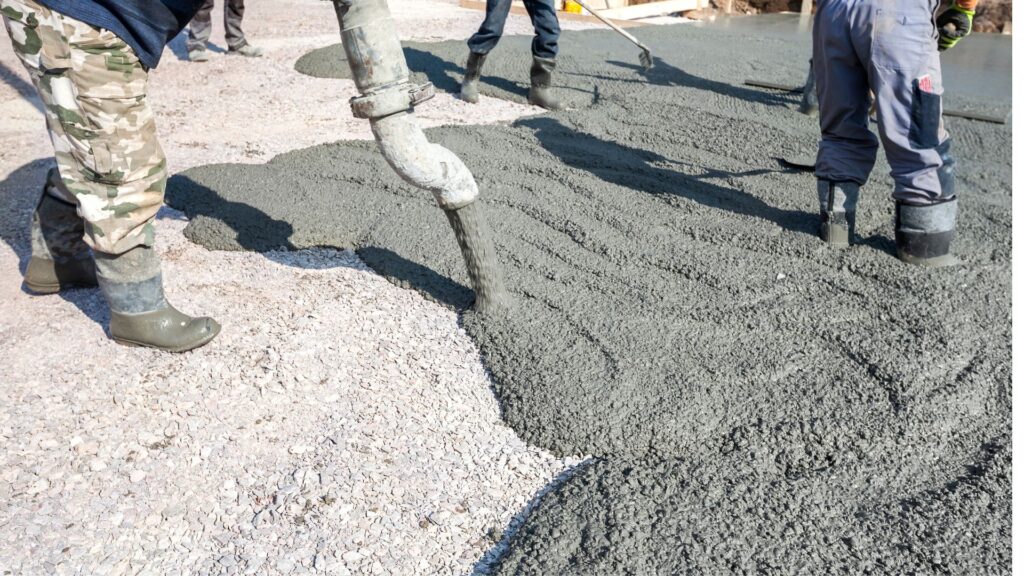
The Role Of A Concrete Cost Calculator
When planning any construction project, whether it’s a small DIY job or a large-scale professional endeavor, accurately estimating costs is crucial. This is where a concrete cost calculator becomes an invaluable tool. Understanding its role can significantly impact your project’s success by ensuring that you are well-prepared financially and logistically.
What is a Concrete Cost Calculator
A concrete cost calculator is an online or digital tool designed to help users estimate the amount of concrete needed for a specific project, as well as the associated costs. It takes into account various factors such as the dimensions of the area to be covered, the thickness of the slab, and the cost per cubic yard or meter of concrete. Some advanced calculators also allow you to input additional variables like the type of concrete mix, labor costs, and other related expenses.
The primary function of a concrete cost calculator is to streamline the process of cost estimation. For both professionals in the construction industry and DIY enthusiasts, this tool offers a quick, reliable way to determine the amount of materials needed and the expected cost, thus eliminating the guesswork that often leads to costly mistakes.
Benefits of Using a Concrete Cost Calculator
Saves Time
One of the most significant advantages of using a concrete cost calculator is the time it saves. Traditionally, estimating concrete costs involved complex calculations, manual measurements, and often, a margin for error. With a concrete cost calculator, you can input your project details and get an immediate, accurate estimate. This efficiency is particularly beneficial for contractors and professionals who manage multiple projects simultaneously, as it allows them to allocate their time to other critical aspects of the project.
Improves Budgeting
Accurate budgeting is essential to the success of any construction project. A concrete cost calculator helps you avoid unexpected expenses by providing a clear and detailed cost estimate upfront. This precision ensures that you don’t over-budget or, worse, run out of funds mid-project. By knowing exactly how much concrete you need and what it will cost, you can plan your finances better, allocate resources more effectively, and avoid the financial strain that often comes with poor budgeting.
Enhances Planning
Beyond just saving time and improving budgeting, a concrete cost calculator enhances overall project planning. With accurate cost estimates, you can make informed decisions about the scale of your project, the materials you can afford, and the timeline for completion. This level of detailed planning is crucial for resource allocation, ensuring that everything from labor to materials is accounted for before the project begins. Moreover, it allows you to adjust your plans if necessary, ensuring that your project remains on track and within budget.
A concrete cost calculator is a powerful tool that brings convenience, accuracy, and efficiency to any construction project. Whether you’re a seasoned professional or a DIY enthusiast, using a concrete cost calculator can make a significant difference in how you approach your project, ultimately leading to better outcomes and greater satisfaction.
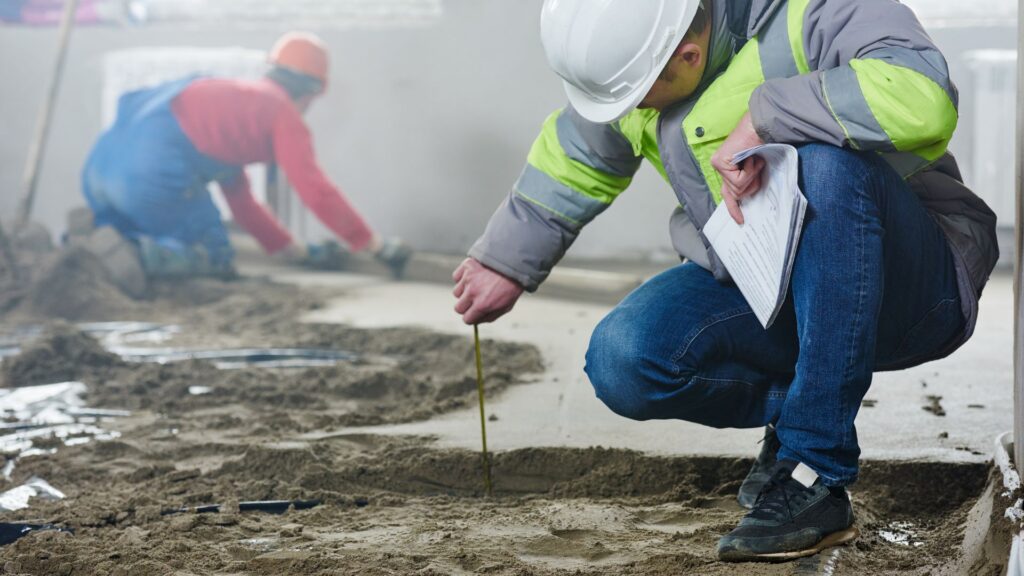
Key Factors That Influence Concrete Costs In New Zealand
Concrete is a fundamental element in construction, offering durability and strength to a wide range of projects. However, the cost of concrete in New Zealand can vary significantly depending on several key factors. Understanding these factors can help homeowners, builders, and contractors make informed decisions, ensuring that projects are both cost-effective and of high quality.
Material Costs
Cement, Sand, and Aggregate Prices
One of the most critical factors affecting the cost of concrete is the price of raw materials, cement, sand, and aggregate. These materials are the primary components of concrete, and their prices can fluctuate due to various reasons such as supply chain issues, changes in demand, or even global economic conditions. For instance, if there is a shortage of high-quality sand in a particular region, the price can surge, directly impacting the overall cost of concrete. Similarly, fluctuations in the price of cement, which is often influenced by global markets, can significantly alter the final cost. Staying informed about these market trends can help in planning and budgeting for construction projects more effectively.
Quality of Materials
The quality of materials used in concrete plays a pivotal role not only in the final product’s durability but also in its cost. Opting for higher-grade materials, such as premium cement or well-graded aggregate, may increase the initial cost. However, these materials often provide better longevity and performance, potentially reducing long-term maintenance costs. Investing in quality materials can be particularly beneficial for projects that require high structural integrity or are exposed to harsh environmental conditions. In essence, while the upfront costs may be higher, the long-term benefits often outweigh the initial expenditure.
Labor Costs
Regional Variations
Labor costs in New Zealand are not uniform and can vary significantly across different regions. In larger cities like Auckland or Wellington, labor costs tend to be higher due to the increased cost of living and higher demand for skilled workers. In contrast, rural or less densely populated areas may have lower labor costs, but this can also mean a limited availability of specialized labor, which might affect project timelines. When planning a project, it’s essential to consider these regional variations, as they can have a substantial impact on the overall budget.
Complexity of the Project
The complexity of the project is another crucial factor influencing labor costs. Projects that involve intricate designs, such as curved structures, or those located on challenging terrains, such as steep slopes, typically require more skilled labor and more time to complete. This increased demand for specialized labor and extended project timelines can significantly raise the overall cost. Therefore, it’s important to assess the complexity of the project during the planning stages to ensure accurate budgeting and to avoid unexpected cost overruns.
Transportation and Delivery
Distance from the Supplier
The proximity of your construction site to concrete suppliers is another significant factor that can influence costs. Transportation costs increase with distance, and for projects located far from suppliers, this can become a considerable expense. Additionally, if the site is located in a remote area, finding suppliers willing to deliver to such locations might also result in higher delivery charges. To mitigate these costs, it’s advisable to source materials from suppliers as close to the project site as possible, or to consider batch mixing on-site if feasible.
Access to the Site
The ease of access to the construction site is often an overlooked factor that can influence costs. If the site is difficult to access due to narrow roads, steep inclines, or other obstacles specialized vehicles or equipment may be required to deliver the concrete. These additional logistical challenges can add to the transportation costs, and in some cases, may also extend the project timeline, further increasing labor costs. Proper planning and site assessment are crucial to avoid unexpected expenses related to site access.
Site Preparation and Additional Costs
Excavation, Ground Leveling, and Formwork
Before concrete can be poured, the site often requires preparation, which can include excavation, ground leveling, and the construction of formwork. These preparatory steps are essential for ensuring the structural integrity of the concrete, but they also add to the overall cost. The extent of these preparations depends on the nature of the project; for instance, sites with uneven terrain or those requiring deep foundations will incur higher preparation costs. Additionally, the type of formwork used whether it’s standard or custom can also affect the budget.
Additional Services
Beyond the basic pouring and setting of concrete, there are additional services that can increase the cost of a project. Reinforcement, which involves adding steel bars or mesh to the concrete for added strength, is often necessary for structural projects but comes at an additional cost. Curing, the process of keeping the concrete moist to achieve optimal strength, may require additional time and resources. Furthermore, specialized finishes, such as stamped or polished concrete, can also add to the expense. While these services enhance the quality and appearance of the final product, they should be factored into the budget from the outset to avoid unexpected cost increases.
The cost of concrete in New Zealand is influenced by a variety of factors, including material prices, labor costs, transportation, and site preparation. Understanding these factors and how they interact is crucial for effective project planning and budgeting. By considering the quality of materials, regional labor variations, transportation logistics, and the specific requirements of your site, you can ensure that your project remains on budget while still achieving the desired level of quality and durability. Whether you’re undertaking a small residential project or a large-scale commercial build, being informed about these key factors will help you make the best decisions for your construction needs.
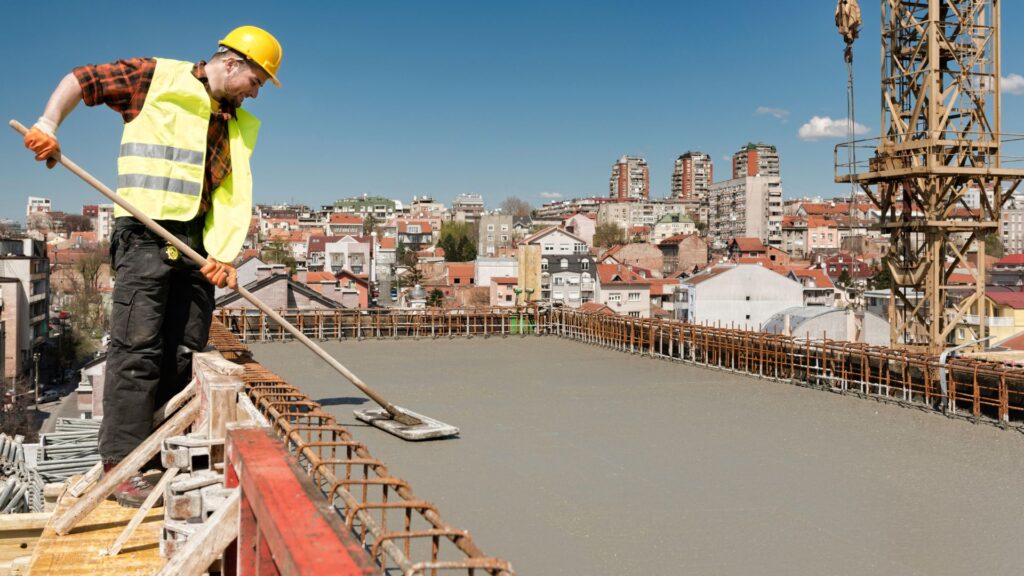
Step-By-Step Guide To Using A Concrete Cost Calculator
When planning a construction project that requires concrete, estimating the total cost is crucial to staying within budget. A concrete cost calculator is a practical tool that helps simplify this process. This guide will walk you through each step, ensuring you have all the information needed to get an accurate estimate for your project.
Gathering the Necessary Information
Before you start using a concrete cost calculator, it’s essential to gather all the relevant information. Here’s what you’ll need.
- Project Dimensions: Measure the length, width, and depth of the area where the concrete will be poured. These dimensions are typically measured in feet or meters, depending on your calculator’s settings.
- Concrete Type: There are different types of concrete mixes available, each with varying costs. Decide on the type of concrete you need, whether it’s a standard mix, reinforced concrete, or a specialty mix designed for specific conditions.
- Site Location: The location of your project can influence the cost due to varying prices for materials and labor in different regions. Additionally, if the site is in a hard-to-reach area, there might be additional charges for transportation or delivery.
Having this information at hand will streamline the calculation process, ensuring that you get an accurate estimate.
Inputting Data into the Calculator
Once you have all the necessary details, it’s time to input the data into the concrete cost calculator. Here’s a step-by-step guide to help you.
- Select the Units: Start by choosing the units for your measurements feet or meters. This will set the calculator to the correct scale for your project.
- Enter the Project Dimensions: Input the length, width, and depth of your project area. Make sure to double-check these figures to avoid any errors in the calculation.
- Choose the Concrete Type: Select the type of concrete mix you plan to use. If you’re unsure, the calculator might offer standard options or even a brief description to help you choose the right one.
- Input the Site Location: Add your project’s location. This could be as simple as entering your ZIP code or selecting your region from a dropdown menu.
- Additional Costs: Some calculators allow you to add potential extra costs, such as reinforcement materials, labor costs, or special finishing options. If applicable, include these to get a more comprehensive estimate.
- Calculate: Hit the ‘Calculate’ button to generate your estimate. The calculator will process your inputs and provide an estimated cost breakdown.
Interpreting the Results
After calculating, you’ll receive a detailed breakdown of the estimated costs. Here’s how to interpret the results.
- Material Cost: This section shows the cost of the concrete mix itself based on the volume required for your project. It’s usually presented as a total sum and may also show a price per cubic foot or cubic meter.
- Labor Cost: If labor costs were included, this will indicate the estimated expense for the work needed to pour and finish the concrete. Keep in mind that actual labor costs can vary depending on local rates and the complexity of the project.
- Additional Costs: Any extra expenses you’ve included, such as reinforcement or special finishes, will be itemized here. This gives you a clear view of how these factors impact the overall budget.
- Total Cost: The calculator will sum all the components to give you a total estimated cost. This is the figure you can use to compare with your budget or with quotes from contractors.
Tips for Adjusting the Results
- Review Your Inputs: If the estimate seems off, go back and review the inputs. Ensure that all measurements are correct and that you’ve selected the right concrete type.
- Consider Local Variations: Material and labor costs can vary significantly based on location. If your project is in an area with higher costs, consider this when interpreting the results.
- Plan for Contingencies: Always allow for a margin of error. Construction projects often face unforeseen challenges, so it’s wise to budget an additional 10-15% above the calculated estimate to cover any unexpected expenses.
Using a concrete cost calculator can greatly simplify the budgeting process for your construction project. By following this guide, you’ll ensure that you gather the right information, input it accurately, and understand how to interpret the results effectively. This approach will help you manage your project’s costs more efficiently and avoid surprises down the road.
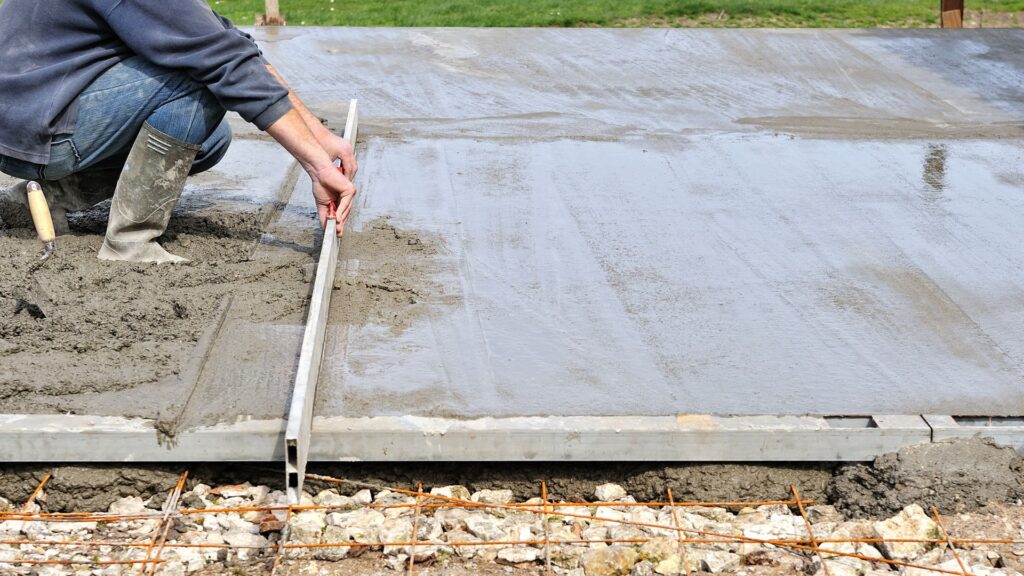
Practical Tips For Reducing Concrete Costs
Reducing concrete costs is essential for staying within budget on any construction project. Whether you’re working on a small backyard patio or a large commercial building, the following tips will help you cut expenses without compromising quality.
Buying in Bulk
One of the most effective ways to reduce concrete costs is by purchasing in bulk. When you order concrete in larger quantities, suppliers often offer discounts on the per-unit price. This is particularly beneficial for larger projects, where the volume of concrete required is substantial. By consolidating your orders, you can significantly lower the overall cost. However, it’s essential to accurately estimate the amount of concrete you need to avoid overordering, which could offset the savings.
Opting for Local Suppliers
Choosing a local supplier for your concrete needs can have a significant impact on cost reduction. The closer the supplier is to your project site, the lower the transportation costs. Concrete is a heavy material, and transporting it over long distances can quickly become expensive due to fuel costs and potential delivery fees. Additionally, local suppliers are more likely to understand the specific needs of your area, including local weather conditions and soil types, which can influence the quality and durability of the concrete.
Reusing Formwork and Materials
Another practical tip for cutting concrete costs is reusing formwork and other materials whenever possible. Formwork, which is used to mold and shape the concrete, can be a significant expense if new materials are purchased for each project. However, by carefully removing and storing formwork after each use, you can reuse it for future projects, leading to considerable savings. Additionally, other materials like reinforcing steel bars and mesh can sometimes be salvaged and reused, further reducing costs. This approach not only saves money but also supports sustainable building practices by reducing waste.
Timing Your Purchase
The timing of your concrete purchase can also play a crucial role in cost savings. Prices for concrete can fluctuate based on demand, which is often higher during peak construction seasons, such as spring and summer. By planning ahead and purchasing concrete during off-peak seasons, you may be able to secure lower prices. Additionally, some suppliers offer discounts at the end of their fiscal quarters or during promotions, so keeping an eye out for these opportunities can result in significant savings.
Seeking Professional Advice
For complex projects, it’s wise to consult with professionals before making any major decisions. While it may seem like an added expense, professional advice can prevent costly mistakes that could arise from incorrect estimates, poor material choices, or inefficient construction methods. Experienced professionals can provide insights into the most cost-effective ways to approach your project, potentially saving you more in the long run than their consultation fees. They can also help you navigate local building codes and regulations, ensuring your project meets all necessary standards without incurring fines or additional costs for rework.
Reducing concrete costs requires a strategic approach, from buying in bulk to seeking professional advice. By implementing these practical tips, you can manage your budget more effectively while still achieving high-quality results. Remember, every dollar saved on concrete can be reinvested in other aspects of your project, enhancing its overall value and success.
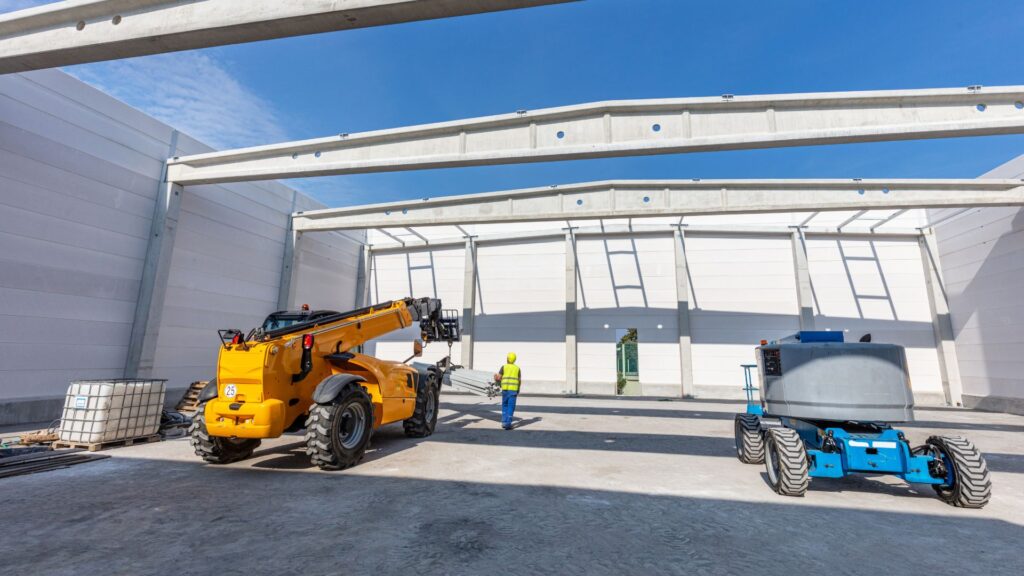
Common Mistakes To Avoid When Estimating Concrete Costs
Estimating concrete costs is a crucial part of any construction project, but it’s easy to make mistakes that can lead to budget overruns and delays. To ensure your project stays on track, it’s important to be aware of common pitfalls and how to avoid them. Here are some key mistakes to watch out for.
Ignoring Site Conditions
One of the most significant errors in estimating concrete costs is overlooking the impact of site conditions. Every construction site is unique, and factors like soil type, slope, and accessibility can dramatically affect the cost. For instance, a site with poor soil conditions might require additional excavation, reinforcement, or specialized equipment, all of which can increase costs. Similarly, sites that are difficult to access may require more time and labor, leading to higher expenses. Failing to account for these variables can result in significant underestimates that disrupt your project timeline and budget.
Overlooking Hidden Costs
Hidden costs are another common issue that can throw off your concrete cost estimates. These often include expenses that aren’t immediately obvious but are nonetheless essential to the completion of your project. For example, permits and taxes are often overlooked but can add substantial amounts to your final costs. Additionally, there may be a need for unexpected materials, such as additional rebar for reinforcement or special additives for the concrete mix. It’s crucial to conduct a thorough review of all potential expenses, including local regulations and material requirements, to ensure that no hidden costs catch you by surprise.
Underestimating Waste
Concrete is a material where waste is inevitable, yet it’s often underestimated in cost calculations. Whether it’s due to over-ordering, spillage, or changes in design, there’s almost always excess concrete that isn’t used. This waste can quickly add up, increasing both material costs and disposal fees. Therefore, it’s essential to include a buffer for waste in your estimates. Industry standards suggest adding an extra 5-10% to your concrete order to account for these potential losses. By factoring in waste, you can create a more accurate and realistic budget, preventing unexpected costs down the line.
Avoiding these common mistakes when estimating concrete costs requires attention to detail and careful planning. By considering site conditions, accounting for hidden costs, and including waste in your calculations, you can create a more accurate and comprehensive estimate. This proactive approach not only helps keep your project within budget but also reduces the likelihood of costly delays, ensuring a smoother construction process overall.
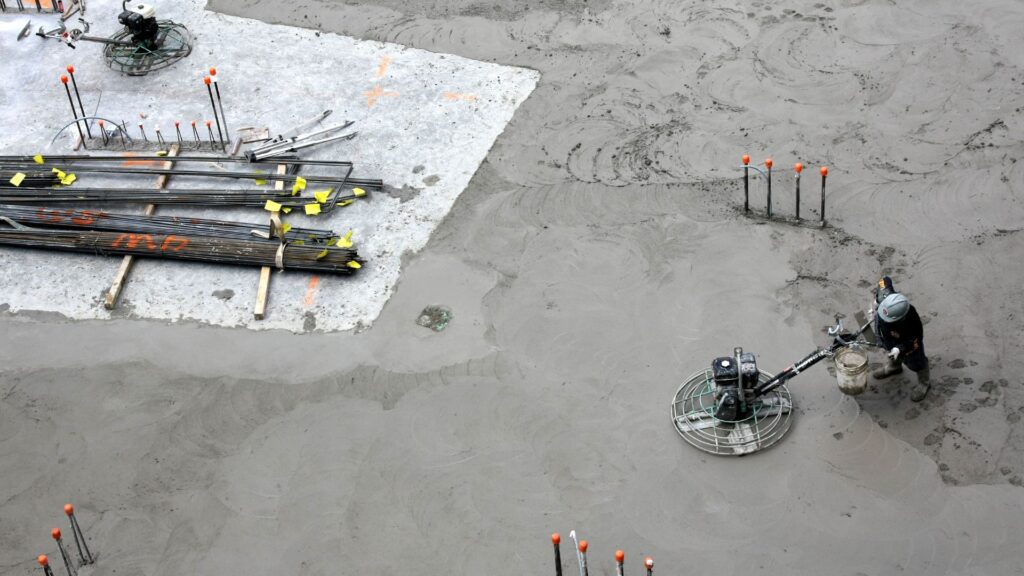
FAQs: About Concrete Cost Calculator In NZ
Conclusion
In conclusion, accurate cost estimation is vital for the success of any construction project, and utilizing a concrete cost calculator can significantly streamline this process. By summarizing the key points, we’ve highlighted the benefits of these tools, from saving time to ensuring budget accuracy. As you plan your next project, we strongly encourage you to use a reliable concrete cost calculator to avoid unexpected expenses and make informed decisions. To get started, check out our recommended calculators and resources. We’d love to hear your experiences please feel free to share your thoughts or ask questions in the comments below to keep the conversation going.
Find A Professional Concrete Contractors Near You!
- Asphalt Contractors Auckland
- Christchurch Concrete Services
- Concrete Contractors Nelson
- Concrete Contractors Tauranga
- Concrete Dannevirke
- Concrete Driveways Lower Hutt
- Concrete Driveways Upper Hutt
- Concrete Foundations Kapiti
- Concrete Layers Auckland
- Concrete Layers Cambridge
- Concrete Layers Hamilton
- Concrete Layers Invercargill
- Concrete Layers Kapiti
- Concrete Layers Leigh
- Concrete Layers Levin
- Concrete Layers Mangawhai
- Concrete Layers Matakana
- Concrete Layers Northland
- Concrete Layers Orewa
- Concrete Layers Palmerston North
- Concrete Layers Pukekohe
- Concrete Layers Rodney
- Concrete Layers Silverdale
- Concrete Layers Te Awamutu
- Concrete Layers Upper Hutt
- Concrete Layers Waikato
- Concrete Layers Warkworth
- Concrete Layers Wellington
- Concrete Layers Wellsford
- Concrete Manuwatu
- Concrete Services Rotorua
- Concrete Whangarei
- Hastings Concrete Company
- Hawkes Bay Concrete Company
- Napier Concrete Company
About the Author:
Mike Veail is a recognized digital marketing expert with over 6 years of experience in helping tradespeople and small businesses thrive online. A former quantity surveyor, Mike combines deep industry knowledge with hands-on expertise in SEO and Google Ads. His marketing strategies are tailored to the specific needs of the trades sector, helping businesses increase visibility and generate more leads through proven, ethical methods.
Mike has successfully partnered with numerous companies, establishing a track record of delivering measurable results. His work has been featured across various platforms that showcase his expertise in lead generation and online marketing for the trades sector.
Learn more about Mike's experience and services at https://theleadguy.online or follow him on social media: