Welcome to our comprehensive guide to understanding the cost of concrete roads in New Zealand. Whether you’re planning a driveway, a residential street, or a larger infrastructure project, getting a clear picture of the expenses involved is crucial for making informed decisions. In this blog, we’ll delve into the factors that influence the cost of concrete roads, from material quality and labor to design and location, and provide you with insights into the average costs you can expect. We’ll also explore the benefits and potential drawbacks of choosing concrete, helping you weigh your options and plan your project with confidence.
On average, the cost of constructing a concrete road in New Zealand ranges from NZD 100 to $150 per square meter, depending on factors such as the quality of materials, labor costs, road design, and location.
- Why Choose Concrete Roads In New Zealand?
- Factors Affecting The Cost Of Concrete Roads In NZ
- Average Costs Of Concrete Roads In New Zealand
- Pros And Cons Of Concrete Roads
- Tips For Budgeting And Planning Your Concrete Road Project
- FAQs: About The Concrete Road Cost NZ
- Conclusion
- Find A Professional Concrete Company Near You!
Why Choose Concrete Roads In New Zealand?
When it comes to selecting the best material for road construction in New Zealand, concrete stands out for several compelling reasons. Here’s a closer look at why concrete roads are an excellent choice for the unique conditions found in New Zealand.
Durability and Longevity
Concrete roads are renowned for their durability, particularly in a country like New Zealand, where the weather can be unpredictable and varied. From the wet, cold climates of the South Island to the warmer, more temperate conditions of the North Island, concrete roads consistently perform well.
One of the key benefits of concrete is its ability to withstand heavy loads and resist deformation, even under the constant stress of traffic and varying temperatures. This resilience is especially important in New Zealand, where roads must endure everything from torrential rain to intense UV exposure. For example, the Christchurch Northern Corridor, a major infrastructure project, utilized concrete to ensure longevity, minimizing the frequency of repairs and disruptions. This project is a testament to how concrete can handle New Zealand’s diverse environmental challenges while providing a stable, long-lasting surface.
Low Maintenance Costs
Another significant advantage of concrete roads is their low maintenance requirements. Unlike asphalt, which can soften in extreme heat and require frequent resurfacing, concrete remains stable and durable. This stability translates to fewer repairs and less frequent maintenance, ultimately saving money over the road’s lifespan.
In New Zealand, where road maintenance can be a logistical challenge due to remote locations and harsh weather conditions, the reduced need for frequent repairs is a major benefit. For instance, the use of concrete on the Waikato Expressway has significantly cut down on maintenance costs, as the road requires fewer interventions compared to its asphalt counterparts. Over time, these savings can add up, making concrete a cost-effective option for both urban and rural roadways across the country.
Environmental Considerations
Environmental sustainability is increasingly becoming a priority in infrastructure projects around the world, and New Zealand is no exception. Concrete roads offer several eco-friendly benefits that align with this goal. First, the durability of concrete means fewer resources are needed for repairs and resurfacing, leading to a reduction in overall material usage and waste. Additionally, concrete’s long lifespan reduces the need for frequent repaving, which in turn lowers the carbon footprint associated with road maintenance.
Moreover, advancements in concrete technology have led to the development of more sustainable options, such as the use of recycled materials and lower-carbon cement blends. These innovations further enhance the environmental benefits of concrete roads, making them a responsible choice for New Zealand’s road infrastructure. Projects like the Kapiti Expressway have incorporated such sustainable practices, demonstrating a commitment to reducing environmental impact while still delivering a high-quality roadway.
In conclusion, the choice of concrete for road construction in New Zealand is supported by its exceptional durability, low maintenance costs, and environmental advantages. These factors make concrete an ideal material for creating long-lasting, cost-effective, and eco-friendly roads that can withstand the diverse and demanding conditions found across the country. Whether in urban centers or rural areas, concrete roads offer a practical solution that benefits both the economy and the environment.
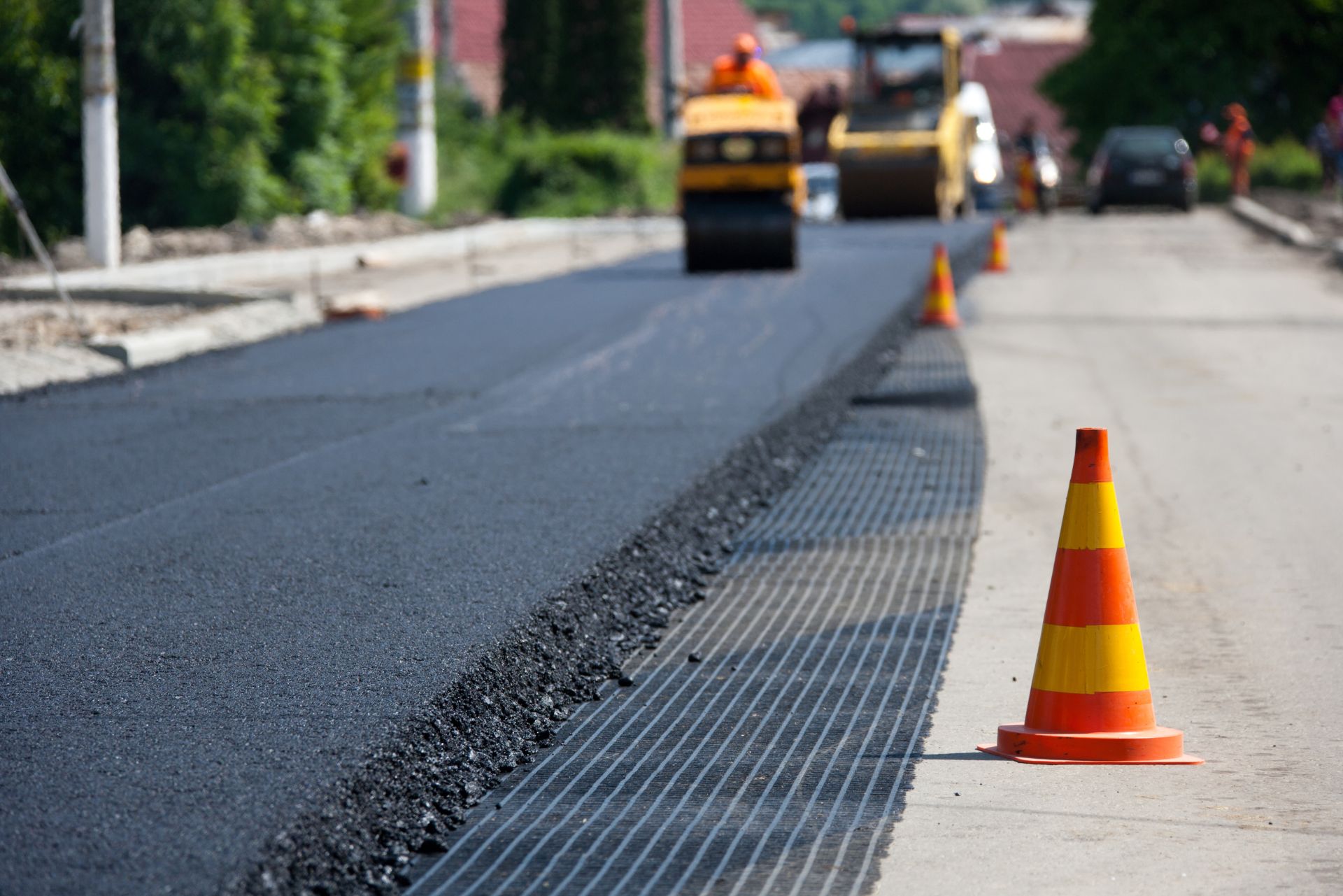
Factors Affecting The Cost Of Concrete Roads In NZ
When planning a concrete road project in New Zealand, it’s essential to understand the various factors that influence the overall cost. Each element, from material selection to regulatory requirements, can significantly impact the final budget. Let’s delve into the key factors that drive the cost of concrete roads in NZ.
Materials and Quality of Concrete
The type and quality of concrete used are among the most significant cost determinants in any road construction project. In New Zealand, a range of concrete mixes is available, each with distinct properties and price points. For instance, standard concrete mixes may be more cost-effective, but high-performance concrete mixes, which offer greater durability and strength, come at a premium.
The choice of aggregates, cement types, and the inclusion of admixtures can further influence the cost. High-quality concrete with superior compressive strength and durability will undoubtedly raise the initial investment, but it can lead to long-term savings by reducing maintenance and repair costs. Therefore, selecting the right concrete mix is a balancing act between upfront costs and the longevity of the road.
Labor Costs
Labor costs are another critical factor in determining the overall cost of concrete roads. These costs can vary widely depending on the region within New Zealand. For example, labor rates in urban areas like Auckland or Wellington might be higher due to the increased cost of living and demand for skilled workers, whereas rural areas may offer more competitive rates.
The experience and expertise of the contractors also play a crucial role. Hiring a skilled and reputable team may increase labor costs initially, but it ensures that the job is done correctly, reducing the likelihood of costly mistakes and rework. Experienced contractors are also more likely to complete the project efficiently, which can further help in controlling costs.
Road Design and Specifications
The design and specifications of the road are fundamental in shaping the project’s overall cost. Factors such as the thickness and width of the concrete slab, the preparation of the roadbed, and the inclusion of features like drainage systems or curbs all contribute to the final price tag.
For instance, thicker concrete slabs are required for roads that will bear heavy traffic loads, which increases material costs. Similarly, a well-prepared roadbed is essential for the longevity of the road, but it requires additional time and resources. Specialized designs, such as those incorporating reinforced concrete for added strength or decorative concrete for aesthetic appeal, will further increase costs due to the need for specialized materials and skilled labor.
Location and Accessibility
The location of the project site can significantly impact the cost of concrete roads in New Zealand. Urban projects often face challenges such as limited space, higher labor rates, and more stringent regulations, all of which can drive up costs. Conversely, rural projects may benefit from lower labor costs and fewer regulatory hurdles, but they can incur higher transportation costs for materials and equipment.
Accessibility to the site is another important consideration. If the site is difficult to reach, whether due to remoteness, challenging terrain, or traffic congestion, the costs associated with transporting materials and machinery will increase. Additionally, projects in isolated areas might require more logistical planning and resources, further contributing to the overall cost.
Permits and Regulations
In New Zealand, obtaining the necessary permits and ensuring compliance with local regulations is a crucial aspect of any construction project. These legal requirements can add to the total cost, both in terms of time and money. For example, environmental regulations may necessitate the use of specific materials or construction methods, which could be more expensive.
Moreover, safety standards must be adhered to, which may require additional safety measures on-site, further adding to the cost. It’s also important to consider that the process of securing permits can be time-consuming, potentially delaying the project and increasing labor and overhead costs. Being aware of and planning for these regulatory costs from the outset can help in managing the overall budget effectively.
By understanding and considering these factors, stakeholders can better anticipate the costs involved in constructing concrete roads in New Zealand, allowing for more accurate budgeting and planning. While the initial costs might be high, investing in quality materials, experienced labor, and thorough planning can lead to a durable, long-lasting road that offers value for years to come.
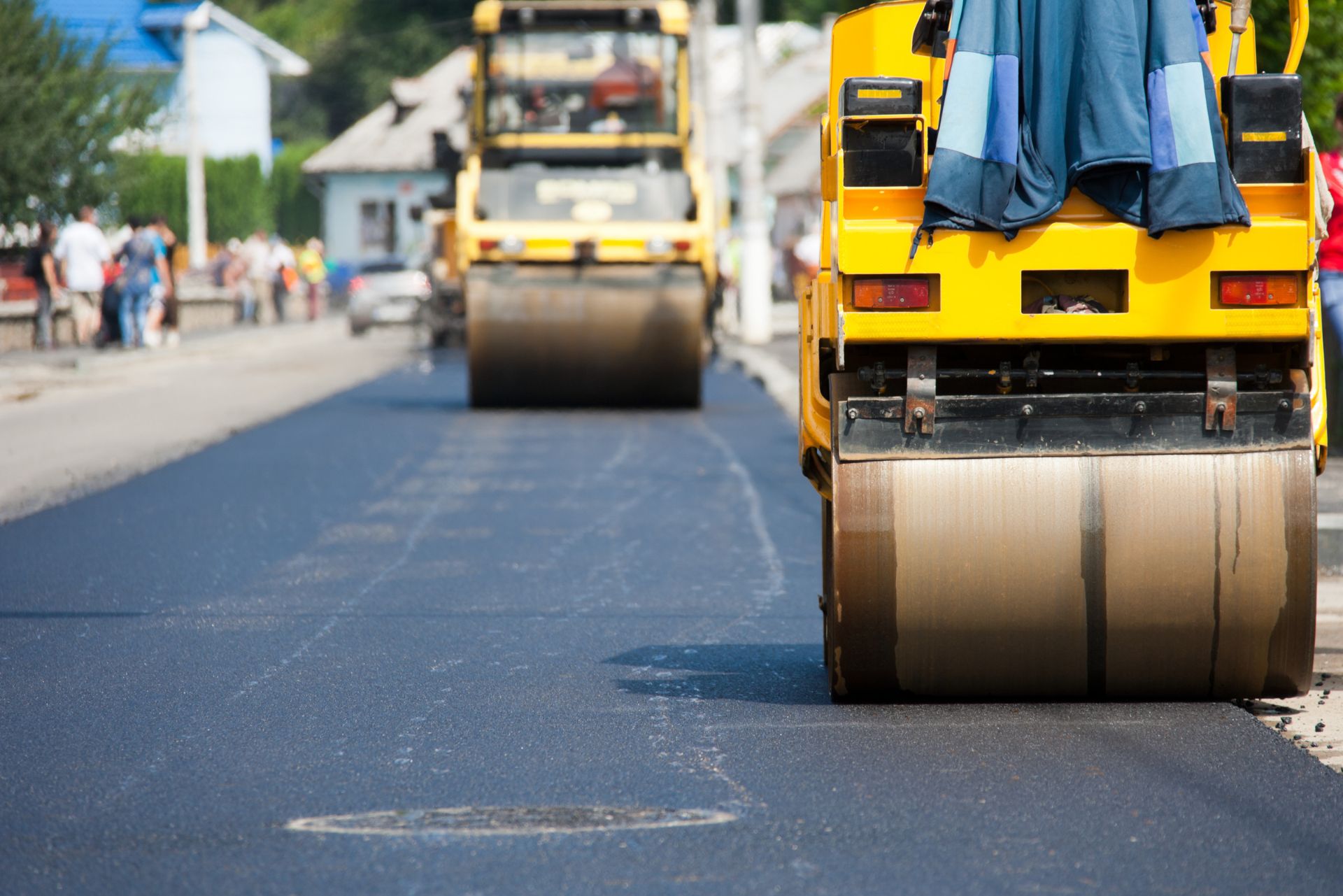
Average Costs Of Concrete Roads In New Zealand
When planning the construction of a concrete road in New Zealand, understanding the financial implications is crucial. The cost of concrete roads can vary widely depending on several factors, including the scale of the project, the quality of materials used, and additional hidden expenses that may arise. In this section, we will break down these costs, offer comparisons with alternative materials, and discuss some real-life examples from recent projects across the country.
Cost Per Square Meter: A Detailed Breakdown
The average cost of concrete roads in New Zealand is typically measured on a per-square-meter basis. For a standard concrete road, you can expect the cost to range between NZD 120 to NZD 180 per square meter. This price range reflects the typical quality of materials used in most public and private projects. However, if you’re looking for high-end options that include superior quality concrete mixes, enhanced durability, or additional aesthetic finishes, the cost can escalate to between NZD 200 to NZD 250 per square meter.
Comparing Concrete to Asphalt
Concrete roads generally have a higher upfront cost compared to asphalt. While asphalt may cost around NZD 80 to NZD 120 per square meter, it often requires more frequent maintenance and has a shorter lifespan than concrete. Over time, the total cost of ownership for asphalt roads can surpass that of concrete, making concrete a more cost-effective option in the long run, especially for high-traffic areas.
Cost Variations for Different Project Scales
The scale of a project significantly influences the overall cost of concrete road construction. For smaller projects like residential driveways, the cost per square meter can be on the lower end of the spectrum. This is because smaller projects typically require less intensive preparation and fewer resources.
For example, constructing a small concrete driveway might cost around NZD 100 to NZD 150 per square meter, depending on the complexity of the design and the terrain. On the other hand, large-scale road construction projects, such as those undertaken by municipal or national government bodies, tend to have higher costs. These projects might include additional requirements such as reinforced sub-bases, sophisticated drainage systems, and extensive road markings, pushing the cost towards the higher end of the range often NZD 180 to NZD 250 per square meter.
Case Study – Recent Road Projects in New Zealand
A notable example is the construction of a new arterial road in Auckland, where the cost per square meter of concrete used was approximately NZD 220. This included enhanced durability features to support heavy vehicle traffic and extended lifecycle expectations, showcasing how specific project requirements can drive up costs.
Hidden Costs to Consider
When budgeting for a concrete road project, it’s essential to consider more than just the surface construction costs. Several hidden costs can significantly impact the overall budget:
- Drainage Systems: Proper drainage is crucial for the longevity of concrete roads. Poor drainage can lead to water accumulation, which may cause the concrete to crack or erode over time. The installation of adequate drainage systems can add NZD 20 to NZD 50 per square meter to the overall cost.
- Road Markings and Signage: Once the concrete road is laid, additional features like road markings and signage are necessary to ensure safety and compliance with New Zealand road standards. These can add another NZD 10 to NZD 30 per square meter.
- Ongoing Maintenance: While concrete roads are known for their durability, they are not maintenance-free. Costs for periodic inspections, minor repairs, and maintenance to ensure the road remains in optimal condition over decades can add up. Although these costs are spread over time, they are an essential part of the total cost of ownership.
Understanding the full scope of costs associated with concrete road construction in New Zealand is essential for accurate budgeting and project planning. From the basic cost per square meter to the hidden expenses that may arise, being well-informed will help ensure that your project stays within budget and meets all necessary standards. While concrete roads may have a higher initial cost compared to alternatives like asphalt, their durability, and lower long-term maintenance needs often make them a more economical choice in the long run. By considering all aspects of the project from material quality to potential hidden costs you can make a well-informed decision that will serve your needs for many years to come.
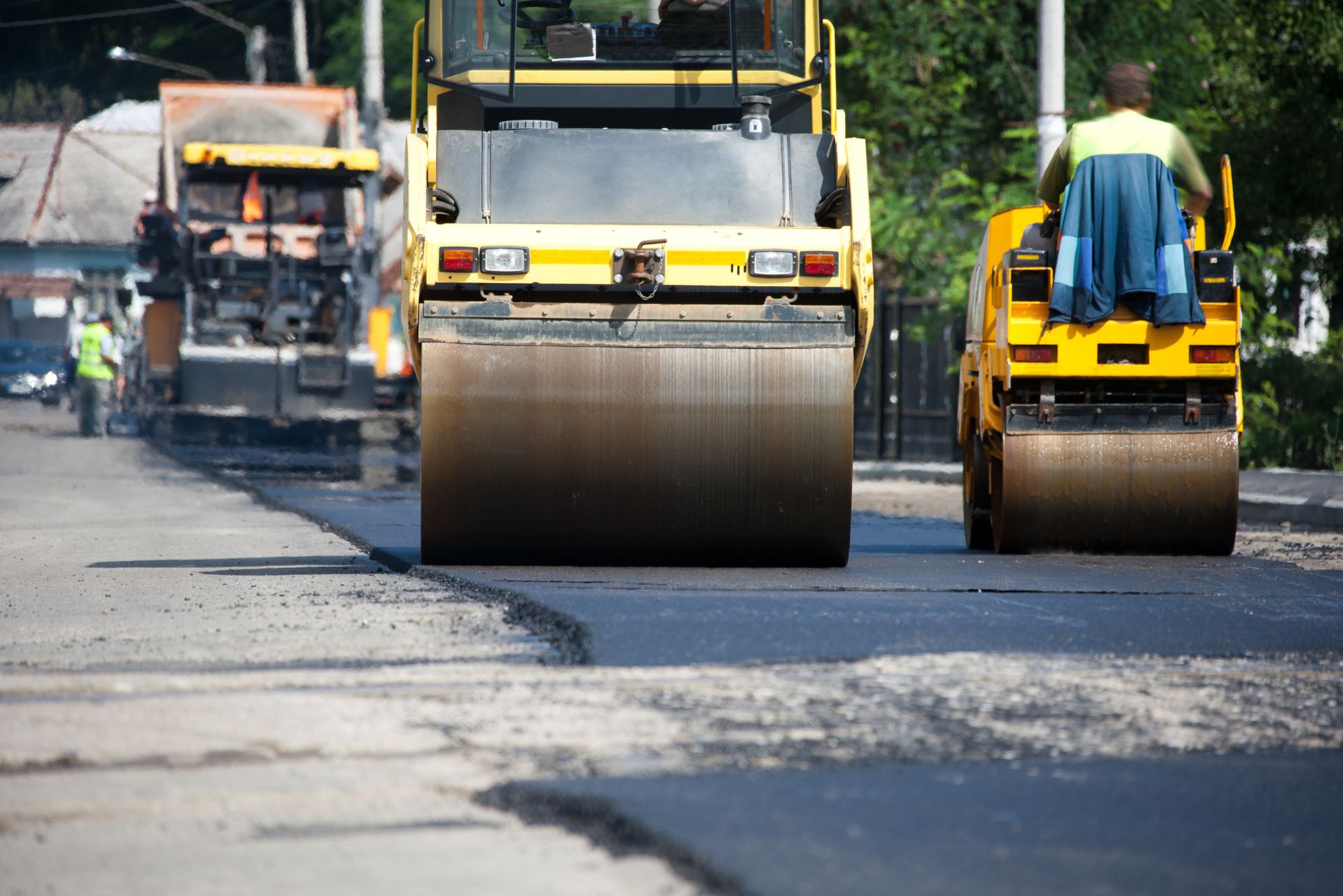
Pros And Cons Of Concrete Roads
When considering materials for road construction, concrete stands out as a popular choice due to its numerous advantages. However, like any material, it also has its drawbacks. Let’s delve into the pros and cons of concrete roads to provide a balanced perspective for anyone considering this option.
Advantages of Concrete Roads
Concrete roads offer several significant benefits that make them a preferred choice for many road construction projects:
1. Durability: Concrete is known for its exceptional durability. Unlike asphalt, which can become damaged due to heavy traffic and extreme weather conditions, concrete can withstand significant wear and tear over time. This makes it an excellent choice for roads that experience high volumes of traffic or are subjected to harsh environmental conditions.
2. Low Maintenance: One of the most compelling advantages of concrete roads is their low maintenance requirements. Due to their robust nature, concrete roads generally require fewer repairs and less frequent maintenance than asphalt roads. This leads to fewer disruptions for road users and reduced costs for municipalities and other stakeholders.
3. Environmental Benefits: Concrete roads contribute to environmental sustainability in several ways. They reflect more sunlight, which helps in reducing the urban heat island effect, particularly in hot climates. Additionally, concrete is often made from locally sourced materials, which reduces transportation emissions. Moreover, concrete is recyclable, and at the end of its life cycle, it can be crushed and reused as a base material for new roads.
4. Long-term Cost Savings: While the initial cost of constructing a concrete road may be higher than that of an asphalt road, the long-term cost savings can be substantial. Due to their durability and low maintenance needs, concrete roads often result in lower overall costs over their lifespan. Fewer repairs mean less money spent on materials and labor, making concrete a cost-effective choice in the long run.
Disadvantages of Concrete Roads
Despite the numerous advantages, concrete roads are not without their downsides. Understanding these drawbacks is crucial for making an informed decision:
1. Higher Initial Costs: The upfront cost of constructing a concrete road is typically higher than that of an asphalt road. This can be a significant factor, especially for projects with limited budgets. The higher cost is due to the materials used in concrete, as well as the specialized labor required for its installation.
2. Longer Curing Times: Concrete roads require a longer curing time before they can be opened to traffic. Unlike asphalt, which can be driven on shortly after being laid, concrete needs several days to set and gain strength. This extended curing period can lead to longer road closures, which may not be feasible for projects requiring quick turnaround times.
3. Situations Favoring Asphalt: While concrete is an excellent choice for many scenarios, there are situations where asphalt might be more appropriate. For instance, in areas where the road may need to be modified or expanded in the future, asphalt is easier and less costly to remove and replace. Additionally, in regions with extreme cold, the flexibility of asphalt can help it withstand freeze-thaw cycles better than concrete.
In conclusion, the decision to use concrete for road construction should be based on a careful consideration of both its advantages and disadvantages. While concrete roads offer durability, low maintenance, and environmental benefits, the higher initial costs and longer curing times are factors that need to be weighed against these benefits. In some cases, asphalt may be a more suitable option depending on the specific requirements of the project.
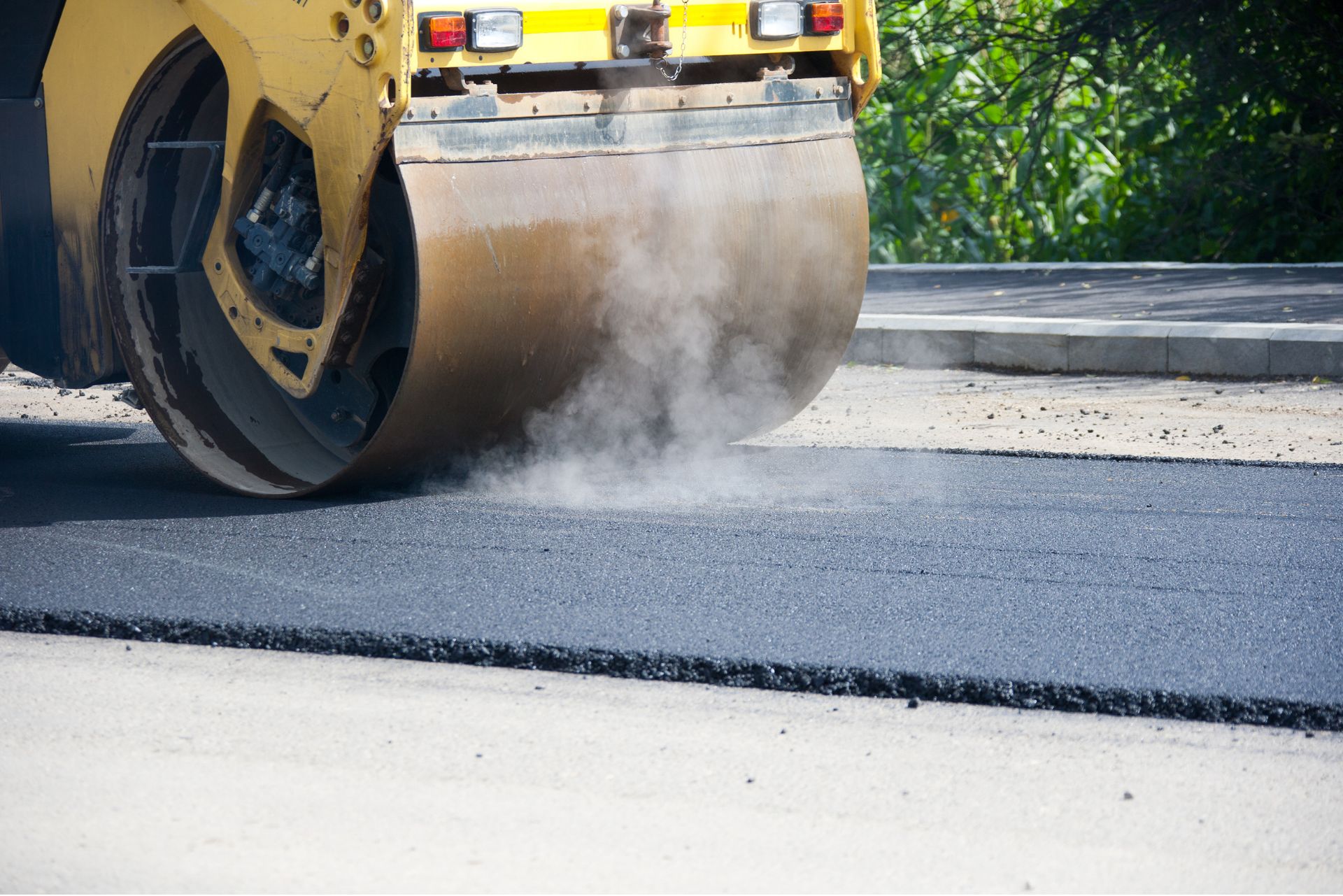
Tips For Budgeting And Planning Your Concrete Road Project
When embarking on a concrete road project, careful budgeting and planning are crucial to ensure the project’s success without unexpected financial strain. Here are some expert tips to help you navigate the process:
Get Multiple Quotes
Before committing to a contractor, it’s essential to obtain quotes from multiple sources. This step not only gives you a range of pricing to compare but also allows you to evaluate the scope of services each contractor offers. When reviewing quotes, look beyond the bottom line. Examine the details of each estimate, including the quality of materials, project timelines, and the specific services provided. Additionally, research the reputation and reliability of each contractor. Look for reviews, ask for references, and ensure they have the necessary licenses and insurance. A lower price might be tempting, but it’s vital to weigh the cost against the quality and reliability of the work.
Plan for Contingencies
Even with meticulous planning, unexpected costs can arise during a concrete road project. Ground conditions might require additional work, or there could be unforeseen regulatory requirements that need to be met. To avoid financial surprises, set aside a contingency budget. A good rule of thumb is to allocate an additional 10-15% of your total budget for these unexpected expenses. This reserve will give you peace of mind, knowing that you are prepared to handle any issues that may arise without compromising the overall project.
Consider Long-Term Costs
While the initial cost of a concrete road project is a significant factor, it’s equally important to consider the long-term financial implications. Concrete is known for its durability and low maintenance needs, which can lead to substantial savings over time compared to other materials. Encourage yourself to think beyond the upfront expenses and consider the total cost of ownership. Investing in quality concrete now can reduce repair and maintenance costs in the future, making it a more cost-effective option in the long run.
Work with Experts
Engaging with road construction experts or engineers early in the planning process can be invaluable. These professionals can provide insights into the most efficient and cost-effective ways to approach your project. They can help with everything from choosing the right materials to ensuring that your plans meet local regulations. By collaborating with experts, you can avoid common pitfalls, streamline the construction process, and ultimately achieve a higher-quality outcome. Their guidance can also help you optimize your budget by identifying areas where costs can be reduced without sacrificing quality or longevity.
By following these tips securing multiple quotes, planning for contingencies, considering long-term costs, and working with experts you can effectively manage your budget and ensure the success of your concrete road project. Thoughtful planning and expert advice are the cornerstones of a project that not only meets your financial expectations but also stands the test of time.
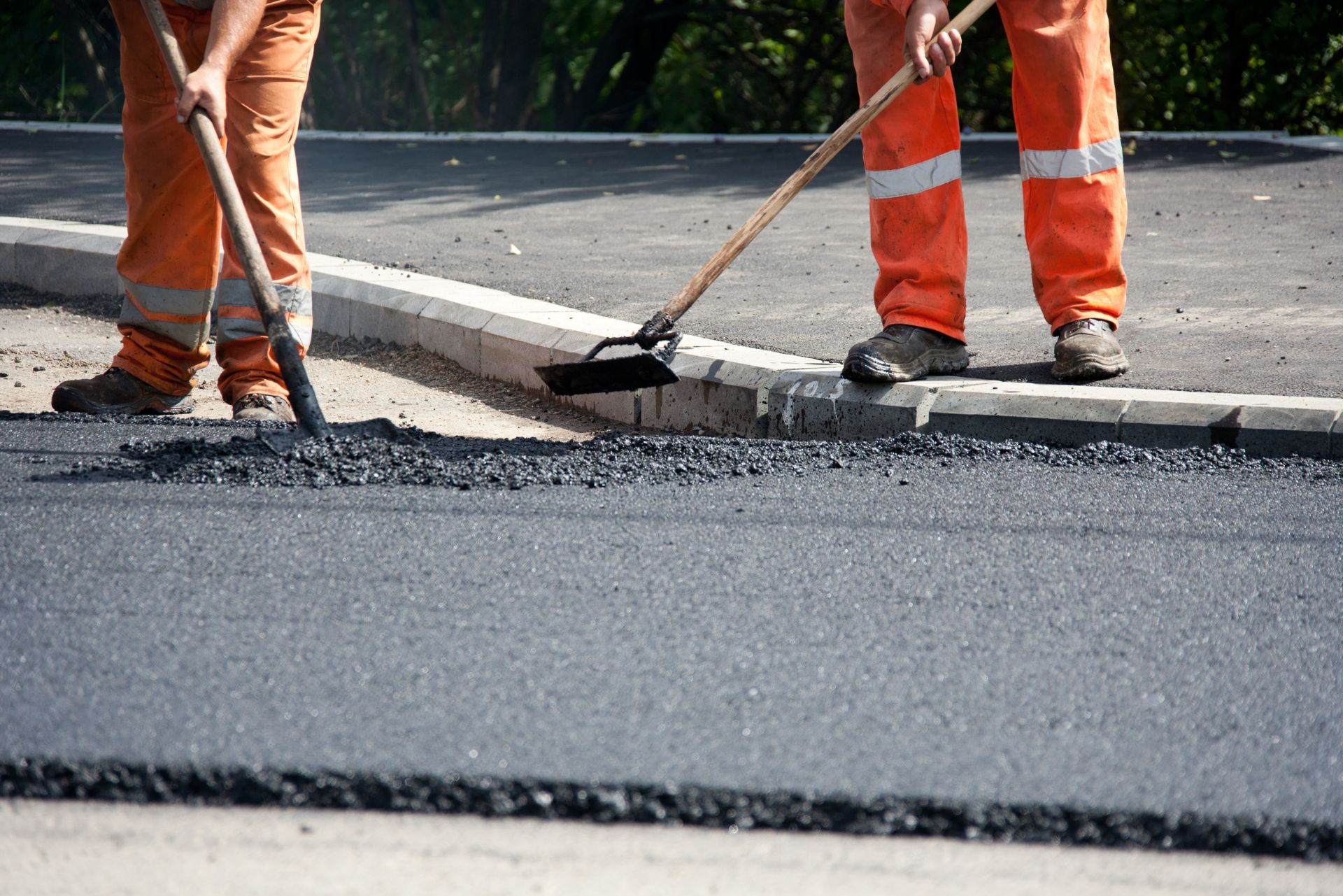
FAQs: About The Concrete Road Cost NZ
Conclusion
Understanding the key factors that influence the cost of concrete roads is crucial for making informed decisions. By investing in concrete, you can enjoy long-term savings and durability, making it a smart choice for infrastructure projects. It’s important to fully grasp all aspects of the costs involved before starting any project, ensuring that you are well-prepared and can maximize the benefits of your investment. If you’re considering a concrete road project in New Zealand, we encourage you to reach out for personalized quotes, consult with our experts, or explore more of our resources to guide your next steps.
Find A Professional Concrete Company Near You!
- Asphalt Contractors Auckland
- Christchurch Concrete Services
- Concrete Contractors Nelson
- Concrete Contractors Tauranga
- Concrete Dannevirke
- Concrete Driveways Lower Hutt
- Concrete Driveways Upper Hutt
- Concrete Foundations Kapiti
- Concrete Layers Auckland
- Concrete Layers Cambridge
- Concrete Layers Hamilton
- Concrete Layers Invercargill
- Concrete Layers Kapiti
- Concrete Layers Leigh
- Concrete Layers Levin
- Concrete Layers Mangawhai
- Concrete Layers Matakana
- Concrete Layers Northland
- Concrete Layers Orewa
- Concrete Layers Palmerston North
- Concrete Layers Pukekohe
- Concrete Layers Rodney
- Concrete Layers Silverdale
- Concrete Layers Te Awamutu
- Concrete Layers Upper Hutt
- Concrete Layers Waikato
- Concrete Layers Warkworth
- Concrete Layers Wellington
- Concrete Layers Wellsford
- Concrete Manuwatu
- Concrete Services Rotorua
- Concrete Whangarei
- Hastings Concrete Company
- Hawkes Bay Concrete Company
- Napier Concrete Company
About the Author:
Mike Veail is a recognized digital marketing expert with over 6 years of experience in helping tradespeople and small businesses thrive online. A former quantity surveyor, Mike combines deep industry knowledge with hands-on expertise in SEO and Google Ads. His marketing strategies are tailored to the specific needs of the trades sector, helping businesses increase visibility and generate more leads through proven, ethical methods.
Mike has successfully partnered with numerous companies, establishing a track record of delivering measurable results. His work has been featured across various platforms that showcase his expertise in lead generation and online marketing for the trades sector.
Learn more about Mike's experience and services at https://theleadguy.online or follow him on social media: